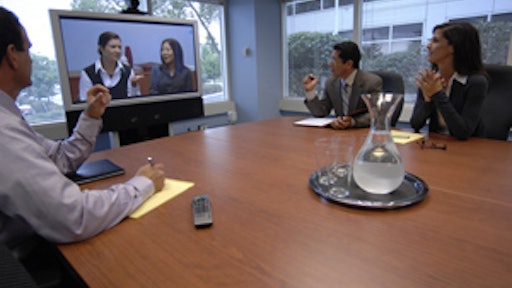
Early in my career, I had the great opportunity to work directly with Dr. Shigeo Shingo as we worked to transform the plant I was managing. I had discovered some of his early publications in a small bookstore in Cambridge, Mass., in the mid-1980s, and after reading the few books available I was stunned at the precision and effectiveness of his ideas. As others in my company read these books we collectively came to believe that we had discovered real solutions to the problems with which we were dealing.
Based on Dr. Shingo’s concepts, we put together a small team and crafted our own training program at our manufacturing facility, ultimately leading to a multi-year journey of understanding and implementing the foundations of what is now known as “lean manufacturing” or the Toyota Production System (TPS). After about a year and a half of implementation, we invited Dr. Shingo to the plant to view our progress, and while noting our solid start, he let us know how far we still had to go. He reminded us that one of the core tenets of TPS is that it is a process not a destination; a system inherently contains inefficiencies and waste. The TPS journey involves identifying the waste, then removing the cause.
In these early years of learning and implementing TPS, I was focused on how powerful some of the tools were and how effective they were at solving classic manufacturing problems. Now, after years in the manufacturing trenches and some reflection, I have come to understand that an essential element of these improvement efforts was the collaboration between the line worker, engineer and anyone else involved in the analysis and improvement process. Structured collaboration sessions can lead to both small and sometimes significant innovations that result in increased throughput or reductions in the opportunities for errors, leading ultimately to increased competitive advantage. The foundation of the TPS is management’s facilitation and encouragement of collaboration, tied to the constant search for a better method and a general expectation that you will be doing your job a little differently tomorrow than you did it today. This methodology can be applied to processes other than manufacturing. Many of these processes touch or support the manufacturing system and can be viewed as the “sphere of collaboration” within companies. The degree to which businesses integrate this sphere of activities and the resources management dedicates to this collaborative approach will be a key factor for success in the coming century.
The Logistics of Collaboration
In the 21st century, competitive advantage is created by an organization's ability to develop innovations that solve problems quicker and create new products or services in less time. Such innovations can enable people or organizations to accomplish objectives faster, easier and with fewer resources. Innovations have been the engine for the tremendous advancements in productivity in recent decades. As organizations become more global and more reliant on outsourcing, the ability to collaborate becomes more difficult because employees who touch a process are located in many different time zones and locations. Outsourcing can be a successful business approach in part because companies can take advantage of their suppliers’ core competencies, allowing those who outsource to use their internal resources to strengthen their own core competencies. The risk with this model is that often all competencies — internal and outsourced — are needed during a collaboration session to solve a new problem or develop a new product. When these skills are spread out around the globe the collaboration process can be cumbersome and anemic. This is one of the reasons that in the early implementation of TPS suppliers were expected to be near the main production facility, delivering small lots and being physically available to consult on problems.
Technology in the Internet age can now deliver supplier intimacy on a global scale, without the need for physical presence. It is the “end of distance” and the beginning of a whole new approach to addressing the inherent wastes and latencies that geographic barriers represent for global businesses.
I have had the opportunity to work with several organizations as they wrestled with the challenges of time and distance implementing process improvements and elimination of wastes. Project teams would wait for team meetings to exchange ideas, suppliers would be surprised by recent design changes from the customer, and management would wait for their periodic in-person meeting to redirect a team or project. I often refer to these delays and wasted time as the products of “human latency.” The natural tendency is to batch ideas until the team gets together or until the supplier is in town or until the next time an in-person meeting is “absolutely necessary.”
For many companies, the communications revolution has provided the ability to embrace a methodology for moving ideas in a “unit of one” despite the geographic distances that organizations are facing. Visual communication technologies are transforming many key business processes in the manufacturing environment. Supply chains are compressed, customers are being brought directly into your organizations, field maintenance teams are getting the expert support they need when and where they need it. These technologies are removing the human latency that has challenged global processes. Technology and enhanced collaboration are allowing organizations to follow Dr. Shingo’s mantra: identify waste in your systems and remove the waste to uncover new capabilities.
The growth of IP networks worldwide has facilitated the integration of video into work processes with significant productivity increases. For example, Volkswagen of Mexico Dealership Association connected the dealerships into a center of expertise where training was delivered over video to each of the dealerships, eliminating the need for the dealership technicians to travel to the training center for four days of training. Additionally, the video solution allowed more frequent training sessions on technical updates that came up between the main scheduled training events.
In a second step, Volkswagen has combined data and video delivered to and from the same repair event, enabling new levels of performance. It used to be that complex repairs required the dealership to hold the car for three to five days until a more highly skilled technician could work on the car or for a less skilled technician to work through the troubleshooting process. Using the IP networks, the data from the dealership’s engine analyzer was transmitted to the center of expertise at the same time a video session was initiated with the technician working on the car. A mobile camera used at the dealerships allowed the engineers at the center to coach the dealership’s technician through the intricate troubleshooting process while being able to see real-time data coming from the engine analyzer. This real-time access to a few experts hundreds of miles away, collaborating and coaching technicians in over 200 dealerships, has allowed VW to improve turn-around on repairs from several days to one, a 300 percent improvement in repair time. First- time resolution rates improved through the quick access to remote experts. Customer satisfaction has increased significantly as a result of the repair time improvement performance.
In the oil & gas exploration industry, visual communications is used to integrate a large collaborative supply chain. Over 160 different companies participate in a data and visual communications network maintained by service provider OilCamp. This network supports operations on the offshore oil rigs connecting them to onshore facilities and then on to the scores of suppliers that support this extensive operation. If the maintenance crew on a rig needs support for a critical repair or preventative maintenance task, they have immediate access to experts onshore. These experts can be engineers at an equipment supplier or members of their own engineering staff. The onshore experts can see exactly what is going on and immediately understand the context for the problem at hand. In another situation, geologists and other consultants can be linked in visually to help in the analysis of data and samples from the drilling activities. The video link between the offshore rig and on shore facilities is on 24 hours a day, seven days a week, providing the ability for around the clock collaboration.
Another capability of visual communication systems is that these events can be recorded. In situations where you have a talented technician that represents the best practice in a particular operation this can be recorded and becomes part of a training video to upgrade the skills of other technicians globally.
Visually-enabled Kaizen
A key methodology for team-based improvements is the technique of Kaizen meetings. Kaizen is word meaning continuous improvement, so the Kaizen technique is a collaborative process where a team works to improve a process or part they work with on a daily basis. These meeting are supported by data that characterize a process or condition that is being investigated. A team associated with the process and possibly some technical experts are assembled to work on improvements. These are structured collaborative events that build on the strengths of the team and their experiences. They start by understanding; what were the forces that created the present condition and brainstorm new ideas to create a new level of performance. These events work best when the team meets near the process they are studying and can “go see,” as Taiichi Ohno would say, the process for themselves. The other hallmark of good Kaizen projects is that they meet frequently for short periods of time, roughly 20 to 30 minutes, to quickly generate momentum and progress. The ability to tie a supplier into these improvement efforts with little cost using video, thereby extending the process improvement capabilities deeper into the supply chain, has powerful benefits.
In a multi-plant environment best practices can be shared across multiple locations much more easily. Operators in one plant can actually see how the other plant has solved a problem or implemented an innovation. However, this is often done through costly, time-consuming travel to each other’s plants. As a result, management can be reluctant to support such trips and have key people unavailable for extended periods of time. And while these trips have beneficial effects, they usually don’t happen very often so the effects are hard to sustain.
One of the values of a visually-connected supply chain or multi-plant environment is that teamwork and cooperation is constantly reinforced with frequent targeted video collaborations that build on each success the team experiences. Collaboration over distances becomes commonplace, and geographic separation becomes a transparent issue as innovation is implemented on a more global scale. To modify an old phrase “think global but act local,” now you can “collaborate and innovate globally while you act and stay local.”
Mobile Video Collaboration
Recent innovations in the field of wireless mobile video allow mobile field workers to communicate in real time with remote experts. This solution supports two-way voice calls and high resolution video stream. The video call allows an expert in the home office to work remotely, seeing exactly what the field worker is experiencing, and offer guidance to resolve the issue immediately. If there is a technician that represents the best practice in a certain operation, their approach to the problem and resolution can be recorded and this material can be integrated into future training sessions. In some situations the capability of an integral touch screen supports live annotation from both ends of the call on the live video stream or on freeze-frame jpg files. This greatly aids the real-time collaboration value of this technology.
Innovations like these are enabled by the ever-increasing capabilities of the Internet or IP networks. The unprecedented level of connectivity allows new ways to deliver product service, collaborate with suppliers and remote development teams, as well as preserve the knowledge of skilled experts in recorded training content.
One foundation of the TPS is to enable a “visual factory.” Let Kanban Systems (a process that limits overbuilding or builds just what is needed when needed) tell a process when to build and when to stop. A clean shop allows oil leaks to be spotted faster and initiate a maintenance activity to prevent down time. Being able to see an operation and all the contributing factors is essential for a successful continuous improvement strategy. When I was working with these methodologies I didn’t truly understand how essential they were in gaining cooperation and understanding for change and improvement. My understanding has grown, having worked with several different companies applying these “visual strategies.” When an effective visual communication strategy is integrated into the work process, enabling collaboration within the work activities, significant process improvements are achieved. The integration of visual communication into a business process enables a new level of performance and the process becomes more inclusive despite any geographic barriers. It allows executives, managers and employees to “see” their business well beyond the factory floor, both into the supply chain and into the customer’s applications. It is perhaps the most effective counter measure to the “eighth deadly waste” that Taiichi Ohno and Shigeo Shingo allude to: the untapped creativity of all the employees in the company and in the supply chain.
About the Author: John Paul Williams, TANDBERG Market Development manager, Manufacturing & Energy industries, is an experienced global operations executive leading innovations in manufacturing, quality and engineering. He has been a successful senior quality officer implementing Lean Manufacturing & Six Sigma methods, including developing strategic sourcing partnerships that increased competitive advantage. One of the plants he managed was the sole winner of the North American Shingo Prize for Manufacturing Excellence. Please contact John Paul Williams at [email protected] for more information. TANDBERG is a global provider of telepresence, high-definition videoconferencing and mobile video products and services with dual headquarters in New York and Norway. www.tandberg.com.