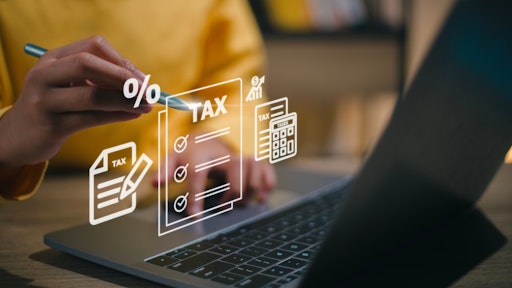
When you hear the term sales tax, the first reference that comes to mind is likely a retail setting. We have all had the experience of getting to the register and seeing a tax added onto the purchase price of our items. However, while retail may be the most common industry associated with sales tax, it’s not the most complex. With its thousands of stock-keeping units (SKUs) and taxability rules that differ across states, managing sales tax in the manufacturing industry is as complex as it gets. Much of the complexity around tax determination relates to purchasing – some of it is related to item taxability, but much of it is related to the taxability of the usage.
Businesses may have hundreds, if not thousands, of exemption certificates to track and keep customers up to date. And as manufacturing companies grow and expand operations, increases in customers and monthly order volumes create challenges in managing potential exemptions. This often leads to order delays and incorrect tax treatment on invoices which can cause a spike in customer complaints and/or defections to competitor offerings.
What Can You Do?
One of the most common and difficult challenges a manufacturing company’s tax team can face is not having real-time tax determination and exemption certificate data in an ERP system. Some tax teams using on-premises tax automation systems may still need to send a ticket to IT every time an exemption certificate is needed, causing unnecessary delays in processing an order. Also, if the tax team is responsible for setting up individual state certificates for each customer or distributor, they can lose valuable time waiting for IT to update multi-jurisdiction forms for pending orders.
It is a common practice for purchasing departments to make decisions on the taxability of parts or other items a manufacturer is purchasing, often leading to errors in filing and increased audit risk. What is needed is a streamlined process for validating the tax treatment on purchases, ensuring they are getting the proper exemptions and tax treatment applied from suppliers.
Driving taxability at the point of sale is critical so that purchasing can then just map the correct materials groups and determine the correct tax rates, cutting down on tax research time. With the help of sales and use tax automation, manufacturers can standardize and automate the AP process and put control back within the tax department, reducing interest and penalty liabilities on audits.
For a multi-billion-dollar manufacturer, a poor sales and use tax audit assessment can mean the difference between paying tens of thousands or hundreds of thousands of dollars in penalties and interest per audit. Sales and use tax automation enables tax teams to make more accurate decisions and can eliminate unfortunate audit cycle penalties, which for larger manufacturers can be in the hundreds of thousands of dollars.
As manufacturers begin to move their technology stack to the cloud, many in response to increased audit frequency and scrutiny, a cloud-based sales and use tax solution will enable tax teams to remove the IT backlog issue, improve jurisdictional-level accuracy and remove the need to manage tax rate and rule change updates, which will always be up to date with the current version of the software.
Aligning Sales Tax Obligations with Your Operations
How can manufacturers navigate the ever evolving and increasingly complex world of sales and use tax? There are several ways to evaluate your current and future approach to sales tax, maintaining compliance the entire way. Here are five considerations for manufactures to ensure sales tax compliance is always at the forefront of the operation.
1. Ensure alignment between IT and tax teams.
Far too often, IT-centric processes miss (or at least misunderstand) key compliance needs and requirements because tax-centric processes fail to consider the practicalities of automation. Both tax and IT must realize that they will need each other for ongoing maintenance and solution expansion initiatives.
2. The need to continually establish and share documentation.
Organizations would be well served to establish and share documentation around their compliance protocols and conduct periodic reviews to ensure best practices. Minimizing audit risk and ensuring company safety needs to be the priority.
3. Recognize the consequences of non-compliance.
There are both tactical and strategic questions at play here, and manufacturers must make thoughtful business decisions around the level of sales and use tax compliance that is sensible for the operation. Increased audit volume is here, and the industry must commit to meeting ever-growing compliance obligations.
4. Regularly review your sales and use tax strategy.
Although a sales and use tax strategy may be in place, continuous evaluation of the effectiveness of the current strategy is critical. Ensuring it is efficiently and accurately maintaining your compliance today with the scalability needed for tomorrow is essential.
5. Use automation and cloud-based solutions.
Automated sales and use tax solutions can ensure precision, while also streamlining reporting capabilities and reducing audit risk. Cloud-based solutions will streamline updates and keep the business moving forward.
Sales tax continues to evolve, and the increasing complexity shows few signs of slowing down. However, that does not mean manufacturers are helpless to improve their situation and become more efficient in sales tax management.
A thorough evaluation of current systems and processes is essential to meeting obligations. As is, modernizing the operation to take advantage of the latest technology and automation capabilities. It is not an easy job, but as with anything, it becomes that much easier when you have the right tools at your disposal.