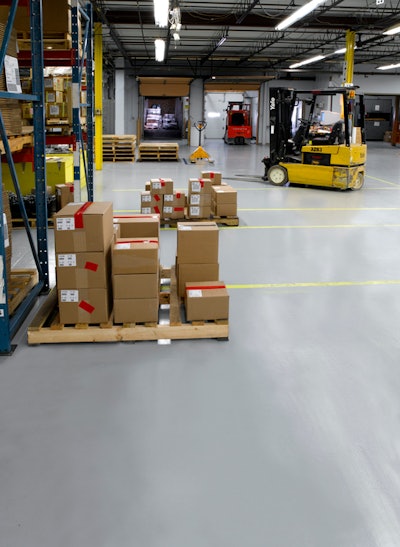
As with the selection of any construction materials you will be using in your facility, the process of selecting the best flooring for a loading dock should start with a thorough analysis of how an area will be used and what it will be subjected to.
When it comes to harsh treatment and potential damage, few areas of the facility’s floor surface are likely to suffer more than the loading docks. Unlike most other areas within the building, loading docks are actually part outdoor and part indoor, so it must withstand the effects of weather, the abuse from heavy traffic and diverse challenges specific to each facility, for example:
- The accumulation of precipitation, snowmelt compounds or traction sand in cold winter regions, abrasive dirt and soil blown or tracked into the facility.
- Dragged pallets, spilled boxes, untold numbers of dropped items impacting the dock surface
- High traffic flow of dollies, hand trucks, heavy equipment, loaded forklifts and pedestrians.
- Oil, fuel and other vehicle fluids that can leak from delivery, transport and drayage vehicles
- The risk of a range of harsh chemicals in both liquid and powder form.
- High levels of moisture within the concrete slab
Over time, these conditions can cause various forms of deterioration to the concrete substrate, such as nicks, cracks, spalls, potholes and worn or low spots.
When ignored, what may seem like a small surface imperfection can quickly turn into severe unevenness that tips a forklift load, damages vehicles, and worse, increases the potential for workplace injury. Expensive repair or replacement of equipment is often just the beginning. Refurbishment of the protective floor topping, and perhaps even replacement of the entire concrete slab, may eventually be warranted.
What to Consider when Evaluating the Needs of a Loading Dock
Safety and efficiency are two top priorities in any facility. Much of this can be addressed by design and layout. However, regardless of how well thought out the traffic patterns may be, lack of traction is lack of traction, and even the best blueprint cannot make a floor abrasion or chemical resistant or provide shock absorbency. The proper coating system can help perform these vital tasks.
So, what are the issues to consider?
- Volume and types of traffic – This is one of the most critical assessments that can be made, both for the design as well as the finish, because no flooring system can totally compensate for an inadequate layout. It helps determine the durability requirements which, in turn, influence the choice of floor coating system. Often underestimated, the volume and types of traffic passing over a loading dock within a specific period of time should be measured and, if there are shifts, measurements should be taken separately, during each.
- The types of chemicals, oils, fuel, battery acid or other corrosives the flooring may be subjected to, as well as the typical exposure time, otherwise known as the approximate period of time likely to elapse before clean-up can take place -- This is especially important in laboratories, chemical processing and automotive plants, but can apply to nearly any industry. Even when both shipped and received materials are properly packaged, occasional drips, seepage and broken pallets are nevertheless bound to occur.
- Whether the loading dock is exposed to rain or snow, dirt or mud, consideration for additional slip resistance, balanced with easy cleaning, is important. Slip inhibiting grit is available in various sizes and can be added to the topcoat of choice to create a light, medium or heavy surface texture. The larger the size of the grit, the rougher the texture.
- Some concrete substrates can exhibit high levels of moisture. Whether originating from a non-functioning below-slab vapor barrier, from “green” concrete still in process of curing, or from condensation droplets settling on the surface, moisture and moisture vapor can cause many floor coating systems to fail. Therefore it is vital that moisture testing be performed prior to any floor coating installation, followed by installation of the appropriate moisture vapor barrier coating, should test results warrant it.
Fluid-Applied Resinous Coatings for Loading Dock Floors
Both epoxies and urethanes provide great protection for concrete substrates. Each of the many epoxy and urethane coatings on the market, offers a unique set of benefits. Informed professional installers are able to take advantage of these various properties in creating the perfect flooring system, designed for your specific facility needs.
The Epoxy Family
Epoxy based coatings are some of the most frequently utilized protective floor finishes in commercial and industrial facilities. High quality epoxy floor coatings:
- Can provide remarkable durability and wear resistance.
- Are available to professional contractors in a range of formulations possessing different performance benefits, such as outstanding acid resistance, quicker cure or extra UV-resistance
- When of the elastomeric variety, can flex with the movement of the substrate to some degree, helping absorb shock and vibration, thus reducing the potential for cracking.
- Are available in a wide selection of standard and custom colors, enabling delineation of work areas, safety markings and traffic lanes.
- Are produced with very low to zero VOC, 100% solids formulations.
- Can often contribute to LEED® Green Building Credits.
Additionally, epoxy flooring requires no waxing, buffing or polishing, so maintenance is simple and inexpensive.
Why Choose a Urethane Topcoat
Urethanes are typically considered a step up from epoxies and thin film urethane topcoats, depending on formulation, can offer some additional benefits, including:
1. Enhanced abrasion resistance in areas exposed to the stress of high volume pedestrian and heavy vehicular traffic.
2. A higher level of, solvent and chemical resistance, which can help increase the coating system’s longevity and better protect the substrate from damage.
3. UV resistance and colorfast properties so the coating will not yellow over time.
Choosing the Right Product
As you see, not only do you have a choice between epoxies and urethanes, but also among the many different products within each of these category. While this might seem overwhelming, there is an easy fix: Simply schedule a consultation with an experienced factory-certified installer, who can assist with thoroughly analyzing your needs and laying out your floor design. Your professional resinous flooring contractor will be able to walk you through the benefits of each option and help you select products that will make the most sense for your needs and budget, as well as offer the best long-term value.