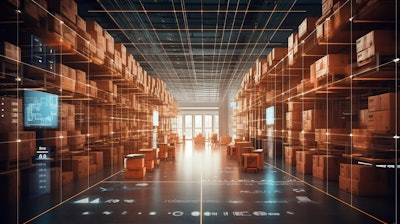
Technology has significantly advanced the logistics industry in recent years, and it couldn’t come at a better time when eCommerce sales have skyrocketed and supply chain issues have persisted. But what if warehouses could directly communicate low inventory or pick items? It might sound like the warehouse of the future, but the technology is already here – It’s called smart warehousing.
What is a Smart Warehouse?
A smart warehouse is a technology-driven facility that stores inventory or raw materials, using various solutions to monitor inventory and optimize warehouse processes. Unlike traditional warehouses, a smart warehouse leverages the latest technology to streamline internal processes.
According to Research and Markets, roughly 80% of warehouses still have no automation solutions, and the rate of investment in these areas is soaring, with the market for warehouse automation technology expected to grow to $37.6 billion by 2030. Another survey found that 27% of warehouse decision-makers plan to invest in this technology by 2024.
Benefits of Smart Warehousing
Smart warehousing requires time and money, but the payoffs are worth it for most companies. The benefits of a smart warehouse include better productivity levels, improved accuracy (fewer errors), reduction in overhead, less paperwork, fewer injuries, greater customer satisfaction, and more.
Top 10 Trends in Smart Warehousing to Revolutionize Your Processes
Building a smart warehouse can elevate processes, but what are the most impactful ways to create a smart warehouse, and how can they affect your processes from end to end? Here are some of the top trends in smart warehousing that can help businesses improve their receiving, storing, inventorying and order fulfillment.
1. A Robust Warehouse Management System
The foundation of any smart warehouse will be its warehouse management system (WMS), which can be run locally or as a cloud-based service. A WMS allows users to manage all essential supply chain functions from a single system, some of which you can share with your partners and customers to provide more visibility.
Using a WMS should complement other automation processes, giving you various benefits like real-time access to quality data, improved inventory accuracy, better supplier and customer relationships, enhanced safety and security, and more.
2. Implementing RFID Tags
With so many items moving in and out of a warehouse, you need the most efficient way to track them. Enter RFID tags. Short for Radio Frequency Identification, RFID uses radio wave-based technology to record and report the location of items with tags in real time.
RFID tags are small, affordable tags that attach to assets like products or pallets. An RFID scanner can read up to 1,000 tags per second simultaneously, reporting the data to a WMS. Employees can use this information for inventory management, order tracking and much more.
3. Internet of Things (IoT)
The Internet of Things (IoT) is another must-have for any smart warehouse. This consists of having sensors connected to vital machinery or assets to control all the moving parts within a warehouse. For example, sensors in cold storage or throughout the warehouse allow users to monitor and control the climate to prevent product spoilage. Other sensors can alert you if a piece of machinery operates outside established parameters, meaning it needs immediate servicing.
4. Increasing Use of Wearables
Wearables are an excellent smart warehouse solution since employees work in fast-paced environments with strict deadlines and must perform repetitive tasks efficiently. To do this, they need to be able to move around as freely as possible with few constraints, and wearables can assist in completing tasks quicker and safer.
Examples of wearables include smart glasses, headsets and even exoskeletons. Workers can wear a headset while picking to get voice commands for their next assignment and can even confirm completion via voice to create a new record in the WMS.
5. Artificial Intelligence & Machine Learning
Artificial intelligence (AI) is the ability of a machine to gather knowledge from experiences and act on those experiences. Machine learning is the ability of a machine to perform tasks well by creating self-learning algorithms. Warehouses use both solutions in areas like warehouse layout optimization, inventory management, staff scheduling, picking and packing processes, and more.
When you apply AI, machine learning and data analysis together, your warehouse can leverage predictive analytics to optimize its logistics processes, better understand customer behavior, and anticipate market changes before they happen. According to a recent report from Deloitte, 31% of businesses already use predictive analytics, which is expected to increase by 48% throughout the next five years.
6. Immersive Reality
Smart warehouses leverage various immersive reality solutions, such as virtual and augmented reality, to improve warehouse operations. For example, workers can use VR or AR to optimize warehouse layouts and VR is an excellent technology for heavy machinery training.
AR solutions can expedite the identification of item details or malfunctioning equipment, streamlining maintenance processes to bring equipment back into safe operating condition.
7. Automated Picking Tools
Picking, which is the process of locating and getting ordered items from warehouse shelves, is one of the most labor-intensive processes. It can also be inefficient and prone to errors due to the repetitive nature of the work.
Various technology solutions can automate some or all of the picking process. For example, pick-to-light, voice automated order picking, and robotic order picking are common. Using RFID tags in combination with mobile-powered carts in the warehouse can also streamline the picking process.
8. Automated Guided Vehicles (AGVs)
Storing and retrieving products is another warehouse management area ripe for automation. Automated guide vehicles (AGVs) can perform a variety of functions, such as storing racks, pallets, or other containers, horizontal and vertical reel storage, storing pallets in warehouse racks, and automated trailer loading and unloading.
9. Collaborative Robots
Collaborative robots, or “cobots,” are fully autonomous robotic technologies meant to work with existing employees, not replace them. Warehouses using cobots usually keep most of their existing infrastructure and processes but can optimize workflows using cobots. These solutions can be used for picking, packing, and inventory management.
10. Automated Storage and Retrieval Systems (AS/RS)
Automated storage and retrieval systems have been around for decades. Examples are pallet lifting and lowering devices, conveyors, product retrieval machines and warehouse control systems. These systems are durable and offer consistent performance in product handling to improve efficiency and supplement human labor.
The Future of Smart Warehouses
Smart warehouses and processes are quickly becoming the norm in today’s business world, and it’s easy to see why—facilities equipped with advanced solutions allow them to operate more efficiently and autonomously. By implementing smart warehousing processes, your business can streamline operations, reduce costs, increase efficiency and improve the overall customer experience.