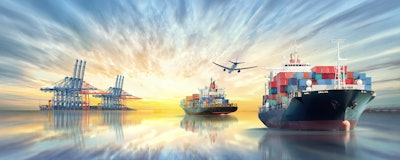
For the past 30 years, businesses have capitalized on the rise of globalization, and this is especially true for manufacturers. China has risen to dominate global trade since it was inducted into the World Trade Organization in 2001 thanks to low costs, a massive pool of qualified labor and unmatched production capacity.
But, 2020 brought a major test for those global supply networks, and when something is tested, weaknesses are exposed. Businesses received a sudden wake-up call, realizing just how much they didn’t know about their offshore suppliers and manufacturers and this lack of visibility caused major problems. A survey by the Institute for Supply Management revealed that 97% of businesses experienced or will experience supply chain disruptions. However, in March, only 44% said they had a plan to overcome these disruptions.
Suddenly, supply chain resilience became a popular topic and conversations around businesses reshoring their supply chains began forming. Sourcing and manufacturing locally make businesses more flexible and responsive, which improves resilience when the unforeseen strikes. Many are exploring this option – 55% of supply chain leaders told Gartner they expect to have a highly resilient supply chain in 2-3 years, up from 21% that said they have such a supply chain today. Though finding partners outside of China is not the only path to better resilience, 33% said they have or will move sourcing and manufacturing activities outside of China in the Gartner survey.
Here's what businesses need to consider when reshoring their supply chains:
1. It’s not an all-or-nothing proposition
For U.S. businesses that have been operating abroad for decades, it may seem cumbersome and unrealistic to replace an entire network of suppliers, manufacturers and distributors with partners in North America. But, you don’t have to. You could start by just adding secondary suppliers in the U.S. or using a contract manufacturer in Mexico while keeping your established partners overseas.
Additionally, there are alternative options that make supply chain relocation less daunting.
- The first is delayed differentiation or postponement, a process where a business outsources certain component manufacturing and then handles subsequent processing steps internally. A warehouse in North America receives components in bulk and employees handle light assembly, packaging, labeling and shipping to the final destination. Postponement can decrease lead times and works well for direct-to-consumer brands, as it enables them to keep more of the right end product on hand to quickly fulfill customer orders.
- The second is a joint venture model where a business can partner with other businesses in the same vertical to stand up a factory or supply a specific material. This enables the business to split the cost of capital and labor and as such, is particularly appealing to more risk-averse or midsize businesses.
Both of these options will help mitigate the impact of another major disruption without fully uprooting a long-standing network.
2. Greater flexibility and control
When China became the global hub for manufacturing, the rationale for many businesses was they were sacrificing flexibility for significant cost savings. This compromise set businesses back this year as long lead times in China made last-minute production changes almost impossible. The closer the supply chain, the shorter the lead time, meaning you can better accommodate a surge or decrease in demand for certain products.
The United States-Mexico-Canada Agreement (USMCA) also ensures local manufacturers and suppliers follow certain labor and environmental regulations, helping a business gain greater control both over their production process and end product. In North America, there is far less likelihood of a partner using a cheaper fabric than ordered or outsourcing labor to a third party that doesn’t offer fair wages or decent working conditions.
In addition to the labor practices mandated by the USMCA, the agreement also regulates greenhouse gas emissions. People are becoming more aware of the environmental impacts of their consumerism, with 81% of global consumers saying it’s very or extremely important businesses try to improve the environment. Another 38% say they will pay more for goods that use sustainable materials, according to a Nielsen report. This passion is shared greatly by the largest generation of consumers – Millennials and Gen Z - although their older relatives are also paying more attention to this issue. Having suppliers or manufacturers in North America provides more clarity around the sustainability of your operations, therefore giving you more confidence in communicating about the environmental impacts to your customer.
3. Costs may be lower than you think
Unsurprisingly, the number one reason China has dominated the global supply chain market is overall costs, and labor makes up a large piece of that. But, as the country became the world’s largest exporter, it lifted the entire economy, and wages increased. Now, the average hourly rate for a manufacturing employee in China is about $2 more than that of a worker in Mexico. Other capital costs in Mexico like real estate, land and machinery are also comparable to China. However, it’s worth noting that both Mexico and emerging manufacturing hubs like Vietnam do not offer the same production capacity as China.
If a business is looking to move parts of its supply chain onshore, it still may be looking to offset the cost of relocation. Automation can be a driver of those savings as automated material handling can help businesses with labor-intensive processes such as sorting, packing and packaging. The equipment is expensive and finding labor that can maintain the heavy machinery can be challenging, but the investment is often worth it in the long run. Keep in mind that automation is a better option for organizations in the hard goods space that can use robots to assemble products versus apparel, which must be sewn by a human.
4. Reshoring makes more sense for certain industries
Before deciding to reshore your supply chain, it’s important to consider your industry. As noted earlier, the production capacity of China is unrivaled with exports totaling $2.5 trillion in 2019, far more than the United States’ $1.65 trillion, according to Statista. Finding qualified labor in China, no matter what industry you’re in, is hardly an issue. Some other countries may not be able to support the needs of large businesses, especially in industries that went entirely offshore in the last few decades. There are other sectors that rely on components produced exclusively offshore – for example, a large electronics manufacturer that needs chips, processors and displays – making it nearly impossible to have a fully North American supply chain.
However, organizations that make essential or highly-regulated products such as pharmaceuticals, medical devices and construction materials have a stronger case for a local or even U.S.-based supply chain because greater control over the end product is critical. These types of businesses are also more likely to earn government subsidies to help with the higher costs of a predominately U.S.-based supply chain.
While a mass exodus of production from Asia by U.S. businesses is unlikely, the past six months have highlighted the limitations and risks of an entirely offshore supply chain. Many organizations should and will rethink their strategy and look to strengthen their supply chains to be better prepared for the next disruption. If your business is thinking about reshoring its supply chain, keeping these considerations in mind will help leaders figure out if it’s the best way for your business to improve supply chain resilience.