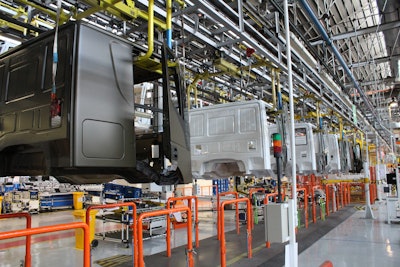
IVECO selects Comau’s MATE exoskeleton to reduce the fatigue on the upper limbs suffered by operators engaged in the heaviest activities.
The technology used in the industrial world should always be considered as a useful tool to support people’s activities, as it improves production efficiency and working conditions while preserving the health of the employees. This is the reason why more and more manufacturers invest resources in the search for solutions to improve the ergonomics of all workstations, and in particular, of those characterized by physically stressful tasks. Among these companies is IVECO, which is continuously at the forefront when it comes to 360-degree technology innovation. The company is also dedicated to health and respect for the environment, giving these issues the same attention as the various aspects of production. The recent introduction of Comau’s MATE exoskeleton in one of the production lines of the IVECO’s Brescia, Italy, plant to preserve the health of its employees while improving their comfort, and consequently, the quality of their work.
Over 100 years in the business
Marco Colonna, Plant Manager of the Brescia plant, says, “The Brescia factory, which now hosts IVECO, has a long history. It was opened in the early 1900s with the brand Officine Meccaniche (OM), the car and truck manufacturing company [that] became famous after winning the first edition of the 1927 Mille Miglia race with a car built in the plant. After that, OM directed its activities toward the production of industrial vehicles. It became part of what was then the Fiat Group, and in 1975, joined forces with four international automobile brands – Fiat Veicoli Industriali and Lancia Veicoli Speciali (Italy), Unic (France) and Magirus-Deutz (Germany) – to create IVECO, which stands for Industrial Vehicle Corporation. During all these changes, the Brescia plant has always played a strategic role, while evolving and adopting new production strategies and technologies. Good evidence of this is that Eurocargo, which was created in 1991 and is still being produced in the Brescia plant, even after being renovated and re-styled several times.”
The Eurocargo line is one of the highlights of the Brescia plant for many reasons. It is in fact a very complex system: everything starts in the bodywork department, where various stamped panels are welded together to build the cabin of the vehicle. Once assembled, it enters the painting area, a fully automated line where six robots apply enamel to the body after a cataphoresis painting process. Later, the cabin moves to the upholstering line, where the seats and dashboard are assembled, together with other necessary parts. In the meantime, the chassis is being built in another department, after which it will be paired with the cabin. The frame enters another assembly line where the engine, gearbox, power pack, suspension system and mechanical components are mounted. The cabin and chassis are should complete their cycles at the same time, so that they can be paired and the Eurocargo vehicle can start its journey all over the world.
Total efficiency
“The production of Eurocargo makes us proud because its huge range of configurations allows us to offer our customers about 13,000 different versions, with a projected repeatability index of about 2.85 for 2019,” adds Colonna. “In other words, it’s very rare that two identical vehicles are delivered at the same time. Obviously, keeping high production efficiency with such significant product variability is not simple, and requires a structured logistic organization because many materials are delivered to the various stations on a just-in-time basis and according to the production cycle. Consequently, the flow of information must be managed correctly as well, in order to ensure that everyone knows what to do at any given time, and has all the necessary tools available for their tasks. This applies to all the company levels.”
Such accurate and efficient organization is the result of the application of the world-class manufacturing (WCM) philosophy, a strategy that incorporates the methodologies of total productive maintenance (TPM), lean manufacturing and total quality management.
Paolo Gozzoli, WCM Plant Support of IVECO, says, “WCM is a production approach that involves the company at every level and function, from production to safety, logistics and maintenance activities. The goal is to achieve efficiency in every department in an integrated way by means of tests and designed tools to manage specific inefficiencies. All our workforce must be involved and made aware that everyone’s contribution is essential to the improvement of our business efficiency.”
The natural consequence of the application of WCM was the redeployment of some of the employees to the interior construction of minibuses with Daily engines. It’s an almost artisanal production that IVECO is standardizing as much as possible and, like any other department, it is subject to constant analysis and research aimed at the continuous improvement of processes.
Gozzoli adds, “The aspects examined also include the working conditions of our operators. This department features many activities that must be carried out while lifting the arms. A demanding condition in itself, which requires even more attention, considering that the average age of IVECO employees is around 49 years. For this reason, in the search for solutions that could make the work on minibuses the least burdensome possible, we started a collaboration with the Ideal Production System (IPS) division, whose task is to search for new ideas and tools in an Industry 4.0 perspective to guarantee the best operating conditions at every time for the people and the plant as a whole.”
A foreseen success
IVECO’s research was completed in 2018 on the occasion of the Automatica fair in Munich, where Comau’s MATE exoskeleton showed its capabilities in a number of tasks.
Gozzoli says, “During the event, we considered different types of exoskeletons, but Comau’s MATE immediately stood out as the ideal solution for our needs. First of all, we required a tool which could help our operators in activities involving the upper limbs without reducing their mobility due to its structure or size. Another crucial feature for us was our conviction that a wearable device should be easy to wear and lightweight, also considering summer heat as a detrimental factor in terms of comfort. Comau’s exoskeleton meets all these requirements.”
After a positive first impression, IVECO assessed the potential of MATE, trying to identify the most suitable tasks for an exoskeleton. An extremely complex operation, which was made simple by a specific app developed by Comau, that quickly and objectively identifies how the exoskeleton can help in carrying out a given task.
Gozzoli says, “We have a long-term relationship with Comau, and this is confirmed by the 116 robots we have in our factory, which are constantly engaged in various activities. Besides being successful and long-lasting, this partnership represents a privilege for us, because we are among the companies which use their innovative products first. In some cases, we can even test them before they are introduced in the market, as in the case of the MATE assessment app, which has allowed us to quickly identify the most suitable tasks for the use of an exoskeleton.”
Reduced fatigue
IVECO therefore provides MATE to some of the operators involved in the construction of minibuses. They used the exoskeleton for a few hours and they could immediately notice a clear improvement in their working conditions. In one specific station, the operator is assisted by MATE in the placement of reinforcements and accessories in the upper part of the minibus. For these tasks, the operators have to keep their arms raised overhead, resulting in trapezius-deltoid muscle fatigue, which was immediately reduced with the introduction of the exoskeleton. This is a remarkable benefit for the employees, who can perform their jobs in a more comfortable situation.
The improvement is witnessed everyday by the operators who count on the support of MATE, including Antonio Maccarinelli, the team leader of Section 1 of the minibus line.
He adds, “I have used the MATE exoskeleton for a few months now, and I must say that I immediately found relief, especially for my shoulders. When mounting the reinforcements in the upper part of the vehicle, I have to keep my arms raised for a long time, often while I’m holding the tools I need to mount the various components. Even though they are all light objects, at the end of my shift I always noticed that this apparently minimal effort took its toll on my body. Now, my shoulders are in an excellent condition. Moreover, I must say that the device is really easy to wear. It’s like carrying a backpack, and just needs a few initial settings to be immediately operational. Adjusting the shoulder straps is also quick and easy, which is really important, because I share MATE with other operators. Each of us has a slightly different build, but we can easily adapt it and feel comfortable.”