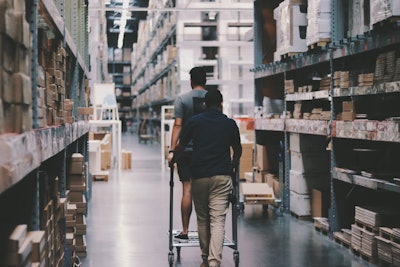
Maximizing efficiency is one of the best ways to reach your production and financial goals in the warehouse industry. Companies of all shapes and sizes are looking for the next tip or trick that will save them valuable time and money, while still helping them perform to the highest level.
If you’re looking to make your warehouse more efficient and a better place to work (for employee retention and recruitment efforts), ask yourself if any of the following things are missing from your operation. Here are seven essential warehouse updates that could be the ticket to getting ahead of your competition.
Upgrading to the RIGHT machinery
If high labor costs and turnover are effecting your business, consider robotic forklifts that will travel through your warehouse, working alongside their human counterparts but that don’t require a human operator.
If a configuration doesn’t call for a comprehensive automation solution, consider using autonomous mobile robots throughout your operation to take over the long travel distances performed on a daily basis by your labor force. These sorts of robots also work well in large warehouses: They’re compact, efficient, and don’t mind hauling pallets long distances to free up human workers for other tasks.
Hydrogen or Lithium Ion Energy Solutions
When you have a large fleet of trucks and warehouse equipment, it can be costly and time consuming to be sure that your equipment is properly fueled up and charged. Using hydrogen-powered equipment allows you to avoid almost all down time, as hydrogen can be made right in your warehouse from a process called steam methane reforming.
While this is becoming more and more feasible for smaller operations, warehousing and trucking giants like Wal-Mart have already invested in hydrogen-powered units for their fleets in the name of cost-effectiveness and establishing a ‘greener’ footprint.
As for your battery-powered forklifts and other machinery, switching your lead-acid batteries to lithium ion can speed up charge times and help you avoid dangerous acid spills and fumes. While lithium ion batteries do not hold a charge as long as the traditional battery, they can be recharged in as little as 1.5 hours. They’re also smaller, reducing the length of your equipment’s chassis, which can help with maneuverability and can allow you to optimize your warehouse by reducing the aisle size.
Incorporating the IoT for Fleet Tracking
Wireless fleet management technology can help you keep track of your trucks, stay on schedule with deliveries, observe driving habits to prevent breakdown and accidents, and monitor the performance of your trucks to prevent down time.
Sensors on your fleet of trucks can keep track of many functions and update you on their efficiency and performance. Truck parts with sensors can tell you when a part is close to needing replacement or can track tire pressure and therefore gas mileage. This data tracking can ultimately help reduce down time and unexpected breakdown.
Keep in mind that many, but not all, of these capabilities are only attainable with trucks that have already have IoT sensors in them, so this suggestion is most easily put into practice if you have an older fleet but could be an influencing factor as you look for newer vehicles.
Updated Storage Systems
Storage seems straight-forward, but there are probably more options out there that you haven’t heard of that could work better for your warehouse. A well-designed storage system can be the difference between profits and losses in a warehouse setting.
For example, you may have wire decking on your pallet racks, but does it make it difficult to see which products are actually on the rack? Certain wire decking allows for better visibility and organization, saving your pickers time and effort in their day-to-day tasks. A small, simple update like this could make all the difference when trying to optimize your employees time in the warehouse.
Investing in shelf racks to replace wheel rails can also help with efficiency, ergonomics and safety. They can be installed right into your existing shelving units and, unlike wheel rails, do not allow for packages to slip between rails and get stuck, causing down time in the overall process.
There are other rack types to consider to optimize workflow including push back racks (which push product to the front of the rack when the box in front of it is removed) and drive-in racks (where a truck or forklift can drive right into the rack itself, enabling operators to drive to the very back of the rack to pick up the last box in the row).
Customized Logistics Software
The right logistics software can gather your data to give you a picture of your operation and help you find areas that could be improved with things like automation.
Logistics software is used for everything from receiving and processing orders, checking inventory, customer service, payments, and keeping track of all documentation and paperwork that goes along with your operation. If you’re still manually processing invoices, looking into the right software to automate and digitize that process might save you time and money in the long run.
If you’re still using spreadsheets to keep track of inventory, an IMS (or inventory management system) could help you avoid human error and keep a closer eye on your inventory, alerting you automatically when stock is low, if you have excess stock or stock that is reaching the end of its shelf life.
One of the most important roles of logistics software is to keep track of your daily operations and your team members. Logistics software will keep track of your KPIs and help you see how and where your team is spending their time. Armed with this data, you can make informed decisions when deciding if you need to upgrade your machines, storage systems, and more.
Automated Conveyor and Picking Systems
Amazon has come up with a brilliant way to automate part of their picking process: Instead of pickers going to the product, Amazon brings the product to them. Using low-profile autonomous mobile robots, Amazon delivers goods to man, where a picker collects the items they need for their shipments. The main purpose of utilizing such robots is to eliminate long walking distances, and focus solely on picking faster and more efficient, which in return will reduce labor turnover and speed up order delivery time.
A second option that you might not have considered has been hanging over your head this whole time. Look up! If you have the vertical space and aren’t using it, consider incorporating overhead trolley conveyor systems. These systems are ideal for:
- Moving/delivering empty cartons or totes
- Removal of trash without the need for a human employee to leave their station to keep their area tidy and safe
- Moving product that may be too messy or large for traditional conveyor belts (anything with oil/grease, odd shapes, extra-heavy items)
- If cost-savings is your goal, consider replacing your conveyors with MDR (motorized driven roller) conveyor systems.
Keep Employee Training up to Date
Industry rules and OSHA regulations require employees to be trained on the equipment they use and equipment best practices, but oftentimes continuous training can fall by the wayside. Proper training is a proactive initiative that can empower warehouse workers to do their jobs safely and efficiently, equipped with the most up-to-date knowledge about their tools and tasks.
To go the extra mile, you could offer incentives for your employees who become part of a safety committee or learn first aid or CPR. You can use the courses as a team-building exercise as well, while helping improve company safety best practices.