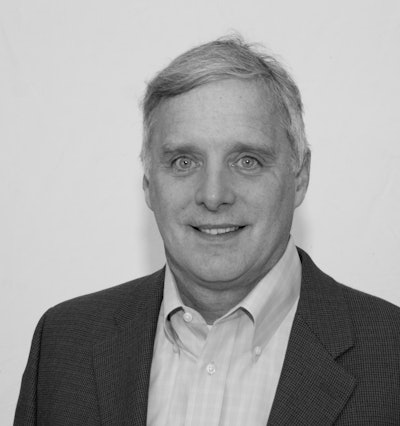
For years, progressive manufacturers enjoyed the benefits of lean manufacturing operations. With today’s omnichannel retail environment creating more incentive for operational efficiency, retailers can enjoy similar advantages by deploying lean techniques regardless of the source of goods sold. While lean manufacturing places emphasis on just-in-time supply and efficient manufacturing processes, for retailers, it’s all about the supply chain.
By applying the five lean principles of supply chain management (people involvement, continuous improvement, short lead times, built-in quality and standardization) to their supply chain and warehouse operations, retailers can reduce waste and drive efficiency. For many, it all comes down to balancing lean with supply chain risk management.
Here are a few tips to make sure you are ready to embark on the journey and likely to achieve the maximum value from your lean initiatives:
1. Look at your Supply Chain Holistically before Diving in
Before doing a deep dive into specific elements, take the time to look across your operation and evaluate performance at a higher level. Are you meeting customer expectations on delivery? What is the executive team’s overall perception regarding warehouse systems efficiency? Is it a company strength or something that is a known improvement area? Taking this holistic look can identify the priority areas that require attention. From a warehouse and distribution center view, this would be an excellent time to actually practice another old-school management technique: management by walking around or MBWA. Take the time to explore the distribution center, looking at obvious places to evaluate.
2. Take a Hard Look at Inventory
Reducing on-hand inventory is key to maintaining a lean supply chain. Work with suppliers to reduce lead times. Make sure your systems and reporting enable accurate and real-time order and trend forecasting. This enables you to reduce safety stock to minimum numbers without risking stock-outs or delays that impact customer fulfillment performance.
Consider supplier compliance agreements to enable more standardized put-away processes and reduce repackaging requirements to aid in the pack-and-ship process. And, of course, look to improve distribution center performance that can lead to reductions in safety stock.
3. Tighten Logistics
Review and evaluate arrangements with transportation partners for efficiencies and better long-term performance. Don’t let the need to meet expedited customer demand force you into a non-efficient shipping situation with premium suppliers. Look to negotiate better and more efficient transportation solutions by potentially consolidating suppliers or engaging in longer-term agreements. And look for opportunities to implement service-level agreements with shipping partners to provide a level of confidence.
4. Update your Warehouse Management Software
Maintaining a lean supply chain is dependent on having the information at hand to not only manage warehouse operations efficiently, but also evaluate processes and potential changes. Old-school, non-automated warehouse management system (WMS) software can’t keep pace with the demands of a lean operation. Make sure you’re taking advantage of the latest cloud WMS solutions as you pursue your lean initiatives.
5. Squeeze Waste from your Pick-and-Pack Processes
With order picking processes widely reported to consume up to more than half of overall warehouse operations expenses, it’s easy to see that inefficiencies here can derail any effort to streamline and improve performance. Evaluate your in-place order processing procedures with an eye to optimizing warehouse layout, order processing technology and the potential for eliminating waste from unnecessary human steps in the process. Optimizing here can shorten order lead times and improve order quality. And this doesn’t necessarily mean adopting new picking technology. Efficiencies can often be gained by evaluating each step with an eye toward eliminating wasted steps or needless wait times.
6. Don’t Forget Returns Management
Retailers often make the mistake of seeing their supply chain as a straight line—from supplier to end customer. The problem is that, for an increasing number of e-retailers, returns are making supply chains more circular. And without a robust returns process and set of practices in place, the idea of a waste-free, lean supply chain can never be realized. The lack of a detailed return processes and standardized procedures can lead to ongoing inefficiency in operations—ultimately negatively impacting bottom-line performance. Make this a priority when evaluating operations improvement initiatives.
7. The Devil Is in the Details
Adopting lean practices is a long-term commitment—one that requires constant review, refinement and, at times, significant adjustment—all of which demands the ability to monitor and measure process and performance against expected outcomes. Armed with the systems, tools and technology in place to do so, you can establish the process metrics and adapt performance measurements to guide your lean implementation.
It’s also important to be sure you measure the right metrics. For example, a focus on dollars or orders picked in a day applied to lean processes might not yield the right information given that metric is impacted by so many factors. It’s better to focus on specific supply chain process steps like number of orders picked, accuracy of out-the-door orders, etc.
8. Make Lean a Company-Wide Initiative
Adopting lean is more than applying new procedures or investing in new tools. It requires a culture built on the somewhat relentless commitment to lean principles and actions. And for that to take hold, a commitment from the entire organization is required. Senior company leaders must communicate the lean vision and expectations. Employees must be empowered to identify improvement opportunities, make recommendations without fear of reprisal and operate in an environment that builds morale.
Adopting lean principles throughout your supply chain can lead to measurable and significant improvements in operational performance. Warehouse operations alone can benefit from improvements in order-handling time, truck loading and unloading time, time spent locating inventory and processing returns, and improved order quality. Add to that improvements in transportation management and inventory efficiencies, and the results can be substantial. But lean has a cost. It requires discipline, potential investment in technology, and a continued commitment to its principles and approach.
There is one factor, however, that might tip the scales in favor of a lean approach. Beyond the documented savings from lean initiatives, one of particular value to omnichannel retailers is that a lean supply chain is much more likely to have the flexibility to adapt to changes in market conditions or customer needs.