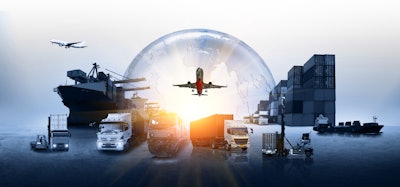
It’s an understatement to say that our current healthcare logistics environment is complex. The healthcare supply chain ecosystem is interconnected and critical to ensuring patients receive care when they need it most. Supply chain leaders at these companies have a seat at the table for determining how the best possible care can be delivered. As a result, these leaders need to bring innovative strategies that enhance legacy approaches that ensures a resilient and efficient supply chain. However, that doesn’t come without its own set of challenges. Many organizations are being asked to do more with fewer resources and face increasing financial pressures and talent shortages that can hamper the team’s ability to evolve.
The logistics industry is at an innovation inflection point: we’re seeing widespread adoption of new technologies and advanced digital tools to plan and monitor supply chain effectiveness, but having an informed performance target in mind must be part of the equation. In fact, a recent McKinsey survey shows that, as of 2023, 79% of supply chain executives have implemented dashboards for end-to-end visibility (vs. 37% in 2022) and their attention has switched to improving the supply chain planning process. Additionally, 71% of respondents stated that they’re actively planning to revise their supply chain processes and governance over the next three years.
While it’s notable to see the industry rally behind digital transformation and adoption, technology is only as useful as the expertise of those navigating it. For many, successful digital adoption will be contingent on supply chain teams going back to the basics to set benchmarks that are realistic but steadily raise the bar for the institution.
A supply chain’s ability to improve its flexibility and sustainability relies on the team benchmarking effectively. Even amid disruption, benchmarking is the key to resiliency, and it starts with understanding your data and uncovering what “good” looks like as well as how you use that information to perform better.
Before we dive in, let’s remember to not conflate the benchmarking process with setting targets or Key Performance Indicators (KPIs). While they should go hand-in-hand, benchmarks focus not only on helping teams understand their own, internal capabilities, but continually cross-examining their supply chain’s effectiveness, and as a result, unlocking the full potential of their supply chain.
Understanding Your Data to Set What “Good” Looks Like
The importance of capturing data to inform our supply chain strategies, which leads to understanding good benchmarks, is not a new concept. The problem isn’t a lack of data; it’s that often an organization’s data is fragmented and difficult to extract from multiple systems. In fact, a study by Gartner shows that only 23% of supply chains are set up to identify, capture and share information seamlessly. While individual data is important, single data points won’t provide a complete outlook of the situation.
To effectively set baselines and benchmarks, healthcare providers should audit their current data setup and tailor their reporting to leverage comparable analytics against the goals of the team, department, or overall business. Uncovering and auditing data can feel daunting at times, and this is often where a trusted, experienced logistics management provider comes in. Such a partner can work on your behalf to optimize your supply chain and serve as an expert with deep industry experience to provide a holistic view of your organization’s operational efficiency. Usually, they can dive deep into your business’ inputs and outputs, but also can balance what’s happening at the industry and national level to help determine what good looks like for your specific business goals.
If you’re not afforded the ability to bring in an outside perspective, a good place to start is asking, “what is the problem we’re trying to solve as it relates to our supply chain?” For many, that’s understanding what potential opportunities there are to unlock and improve efficiency.
There is no one-size-fits-all strategy when it comes to selecting the right data sets for your benchmarks and data management. It’s important to keep in mind the right level of data your business needs to set benchmarks – what works for one department in a matrixed environment like a health system might look drastically different than another department. For example, a time sensitive or temperature-controlled shipment like a specimen is going to require a higher proportion of express or overnight delivery, but a department that handles more standard or shelf stable supplies like PPE is afforded a longer, less expensive delivery. These two departments are often looking at different variables when it comes to benchmarks such as shipping spend or outbound delivery modes.
That’s all to say you really can’t go off cumulative data alone. However, to get started, some areas to begin peeling back the layers to start setting benchmarks and are often universally analyzed include:
- Location and shipping habits: Examine shipping habits and volume of individual locations and compare those metrics to other locations that are part of your network.
- Volume trends: Evaluate shipment volume coming into or leaving your facility over time and by service level. Are there certain times of day/year that are higher in volume? How can you proactively and effectively plan workflows to support that seasonality?
- Shipping costs: Analyze shipping costs to uncover if employees, or suppliers, are selecting the correct mode and allow for potential education on optimization to reduce costs.
Being able to turn data into actionable insights is the most crucial step of this process, and benchmarking is contingent on it.
Using This information to Get Better
By now, you probably understand that benchmarking can be a complex process, and it’s not one where you can “set it and forget it.” Achieving supply chain excellence relies on a nimble and proactive benchmarking process. As we outlined above, benchmarking is a tool that can help organizations set realistic goals while raising the bar on responsible financial decision making. The best use case of benchmarking is to establish best practices and guardrails across your organization to execute on and increase improved performance – which is always a moving target.
Supply chain managers that effectively use benchmarking know it’s a constant balancing act where teams are making tradeoffs to optimize their supply chain, prioritize needed improvements and uncover hidden value. Teams need to be consistently collecting data, checking it against department goals, discovering areas of strength and opportunity, as well as pressure testing scenarios along the way. Organizations must remain nimble and agile as it relates to benchmarks as it’s vital to mitigate disruption and pivot when necessary.
Benchmarking can feel like a complicated process, but going back to the basics is a sure way to return to determining what good looks like and turn insights into action. By understanding your data and revisiting this process, you’ll be able to unlock incredible value for your supply chain, withstand the unexpected and come out ahead.