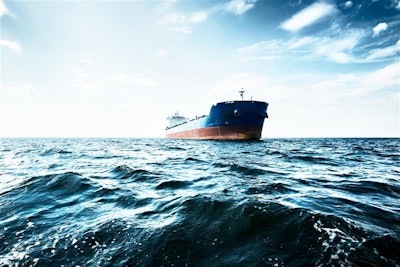
A new year has begun, but supply chain experts are still beset with the problems of 2021, mired in untangling a still-messy shipping crunch. There are many areas to point blame – a new COVID-19 variant locking down suppliers in Asia, increased consumer demand, aging shipping fleets – but understanding the reasons behind the supply chain challenge is only part of the larger solution.
With the two major ports in Los Angeles and Long Beach, California still bottlenecked, logistics managers have gotten creative in circumventing these shipping stopgaps by seeking alternative ports and exploring different methods of delivery.
However, changing shipping processes can create more wrinkles in the supply chain if marine managers are not well-prepared. Here are best practices for logistics experts to respond to the evolving supply chain risks and protect against loss.
Examine costs and benefits closely
Logistics managers have spent the past year looking for alternatives to moving cargo through backed-up major ports, but not all solutions are created equal. Each decision comes with costs and benefits, and managers and leaders must make difficult choices when considering each creative solution.
For example, some big box retailers whose businesses hinge on large volumes of goods flowing in have opted to invest in building their own dedicated fleet of cargo vehicles and vessels to circumvent the backups in third-party shipping. Other companies have explored sending their supplies via air cargo, skipping ports altogether. Both of these solutions, while effective, come at a steep cost that most companies – especially smaller businesses – can’t afford.
Also consider the costs of rerouting cargo containers through other ports in spots like Houston or Miami. Marine managers should be well-versed in how changes in route will affect the cargo being shipped and the timetable for delivery.
Report losses immediately
Aside from dealing with late shipments and angry customers, companies take on some risk when choosing alternative routes or shipment methods to circumvent supply chain snags at ports. Traditional marine perils, like bad weather or rough seas, may add risk for containers on a longer or different route. Contractual deadlines may be harder to meet when shipping through an alternate port. Perishable goods containers are especially at risk, whether containers are stuck at a main port or rerouted to an alternate port.
If a loss does occur, it is imperative that logistics managers report the loss immediately so that insurance teams can begin the claims process. The sooner a marine surveyor can investigate what went wrong with the shipment, the scope of the damage, whether any goods can be salvaged and who is responsible, the better.
Keep necessary shipping documentation
No matter the cargo route or alternative shipping solution, marine and logistics managers should carefully organize and keep all shipping documentation to ensure all the details of the shipment are accessible if a loss occurs. Documentation helps clearly delineate the responsibilities of both the buyers and sellers, and these can vary significantly depending on the transaction.
If a cargo claim needs to be filed, documents including the bill of lading, a commercial invoice and packaging lists are essential to help with the investigation surrounding the loss. Marine surveyors are experts at going through this documentation, but supply chain knots can get untangled faster when information is quickly available and organized.
Trust technology to clear up questions
In the early days of global trade, when cargo became lost or damaged it was sometimes impossible to understand what went wrong – or if the cargo ended up somewhere incorrect or at the bottom of the sea. Thanks to technological advances like data loggers, sensors, and sophisticated weather and ocean instruments, marine surveyors have a much easier time understanding what happens to cargo while in transit.
Determining if a cargo container has been subject to extreme temperatures or suffered damage from a severe impact is a crucial part of a loss investigation. This process is especially important if containers have been rerouted to avoid supply chain backups, as a loss is more likely to occur on a new route.
This has always been the most difficult piece of the puzzle to solve, but companies that depend on global shipping for their business should ensure cargo transport partners employ up-to-date tracking technology which can help clear up a claim if a loss does occur.
Maritime professionals play a pivotal role in smoothing out the supply chain – the current crisis has just heightened the awareness around how important these experts are. Help these vital players in the supply chain by making well-researched decisions when seeking alternate shipping solutions and ensuring your organization has the proper steps and documentation when taking new shipping routes.