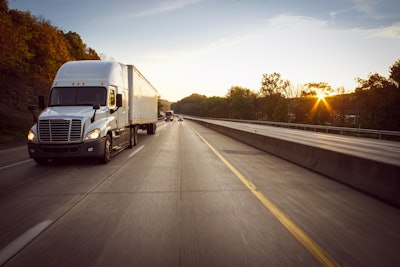
Transportation experts are predicting that as many as one-third of all commercial trucks and buses will have alternative drivetrains by 2030. Many of these are expected to be fully electric. With this push to vehicle electrification, vehicle designers will need to rethink how to power accessories.
Today’s vehicles with internal combustion engines rely on belt-driven accessories for power steering assistance, air conditioning and battery charging. With electric drivetrains, fans and alternators are eliminated, as are belt-driven accessories. Instead, air conditioning compressors and power steering pumps will need to be driven by small electric motors.
The challenge with electrically-driven (EV) accessories in battery-powered electric vehicles is their range-robbing potential. If the motors used to drive the accessories are incorrectly spec’d, they could draw significant amperage, pulling down battery levels more quickly than desired and reducing the vehicle’s effective range.
Ideally, the motors used to drive EV accessories should have five key qualities:
- High output with low power draw. High efficiency is important to keeping the electrical draw to a minimum. The best measure for this is the ratio of electrical input power to motor output torque. Percentage efficiency is calculated by taking the work out/work in. Work in = Voltage*Current. Work out = Torque*pi*RPM/30. You should be targeting motors with efficiencies of 40% or greater.
- Long life. Motors should be designed for several million cycles before failure. Commercial vehicles put on a lot of miles and will have high accessory usage. Fleet owners can’t afford frequent replacements.
- Designed for harsh environments. Vehicles experience weather extremes and need motors which can handle heat, moisture, dust, and cold conditions. Don’t pick a motor which is not designed for these conditions. Look for motors with high ingress protection (IP) codes, such as IP67 or IP68, which indicate high protection from solids and liquids.
- Programmability. By equipping motors with encoders, you can run them even more efficiently and adjust output/speed to changing conditions. Look for motors already packaged with encoders, so you can save time involved in integrating with control systems.
- Easy to replace. Sticking with simple, proven brushed motor designs is wise because of the many years of refinement in vehicle applications such as wiper motors. These motors are quickly and easily replaced at low cost.