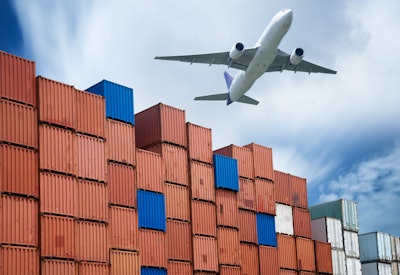
Research shows that 86% of buyers are willing to pay more for a great customer experience. That’s because in today's hyper-connected world, customers don't just buy products or services, they buy an “experience.” Products and services cannot compensate for an encounter that is not optimal. In order to maximize profitability, companies must invest time, money, and resources in delivering excellent customer experiences, often defined as one that exceeds expectations.
Supply chain vital signs
To accomplish those goals, companies need to focus on key areas referred to as supply chain “vital signs,” which are 1) people and culture 2) data and advanced analytics 3) process and 4) change management. Much like in the human body, vital signs in the context of supply chain business provide critical feedback on the health of supply chain operations and its direct impact on customer experience.
People and culture.
Supply chains are incredibly complex ecosystems, global and diversified in nature with different tiers of suppliers; original equipment manufacturers (OEMs); maintenance, repair and overhaul (MRO) providers; and customers. In general, the supply chain of OEMs has always been multifaceted, unpredictable and struggling to keep up with customers’ needs. In this ecosystem, culture is how things get done, and people are the primary resource that drives supply chain results. To be successful in this ecosystem, language of purpose needs to be identified, explored and implemented through partnerships with the broader community. Organize and mobilize employees around customers’ needs and empower them with the ability to deliver. In the time of the Coronavirus disease (COVID-19), companies have demonstrated supply chain creativity, innovation, collaboration and strength in keeping society fed, supplied and healthy. For example, there have been apparel companies that manufactured personal protective equipment (PPE) and airlines that converted dormant warehouses into food-processing centers. Those shifts would normally have taken months or quarters to plan and execute. However, purpose-driven supply chain talent managed to shorten these timeframes to a couple of weeks. In many ways, the supply chain represents the heart of the business as companies strive to improve the customers’ experience daily.
Data and advanced analytics (continuous intelligence)
Data fuel the intelligent supply chain. Advanced analytics include predictive analytics (those that identify data patterns and anticipate future scenarios) as well as prescriptive analytics (a set of capabilities that finds a course of action to meet a predefined objective). The increased availability of Internet of Things (IoT) data and extended external data sources such as weather or traffic conditions allow organizations to anticipate future scenarios and make better recommendations in supply chain planning, sourcing, and transportation. Advanced analytics will help organizations become more proactive and actionable in managing their supply chains, both in taking advantage of future opportunities and avoiding potential future disruptions. According to Gartner research, “the average financial impact of poor data quality on organizations is $9.7 million per year.” Fundamentally, analyzing performance-turning data into information, placing it in context and then turning that information into action starts with capturing quality data. Every transaction is breathing tons of data in and out, and without quality data, the supply chain business is a mystery. One of the keys to sustain attention from leaders and collaboration from peers is to make the customer experience matter in terms of the results that are important to them. Prove how satisfied customers drive up revenue, lower churn, reduce costs and grow the business by combining customer satisfaction data with transaction and operational data. Drive more value from these touch points by analyzing the gaps and bridging the gaps using technology. Companies can use these touch points to generate more demand and differentiate themselves in today’s crowded market.
Process
The basic units of supply chain are the processes that flow along its functions and partners. Siloed, difficult-to-use business systems complicate processes and hamper operations. According to IDC, companies lose 20-30% in revenue each year due to inefficiencies. A well-defined process guarantees reliability and converts vision into measurable value. The emergence of smart products enabled by IoT allows the transmission of data back to OEMs about their condition and usage and presents an opportunity for OEMs to communicate directly with end-customers while offering them add-on products and new services. OEMs are optimistic that they can achieve meaningful business benefits from supply chain transformation, including an improved ability to compete. In the current environment, the natural tendency of many companies is to reduce spending, including money tied to transformational programs while advanced supply chains are pressing forward.
Change management
Research shows that 75% of the executives agree that supply chain digital transformation is very important. The future state of digital supply chain transformation is all about focusing on business value and return on investment. Yet, there is also research that shows that 70% of digital transformations fail. That’s because this is not a technology shift, but rather a paradigm shift. In order to succeed and sustain these transformations, it is important for organizations to recruit change agents and engage employees by presenting a compelling vision for the future. Keep everyone informed as to “why” the organization is transforming, “what” will happen to employees and “what’s in it for them,” and show “how” they have an opportunity to drive the transformation forward. Adapt a mindset that accepts and embraces long-term perpetual change. When change management is governed with purpose-driven change-management principles, it helps people see the big picture in an era of increasingly rapid change.
One size doesn’t fit all
Companies that deliver the highest return on their investment begin with the customer in mind. In that sense, the customer experience is the new battlefield of corporate differential. Like with the human body, the health of supply chain operations is dependent on "vital signs" that must be carefully revived to provide better customer experience. While every organization is different, the end goal of delivering a customer experience that meets or exceeds expectations is universal.