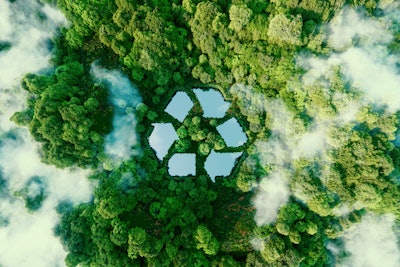
A good 90% of global plastics are made from fossil resources. At the same time, less than 10% of plastic waste gets recycled. In an ideal world, these figures would switch places: There is an urgent need to reduce emissions across the plastics value chain and turn these value chains from linear to circular to combat plastic waste pollution.
While plastics are a crucial enabler for all kinds of applications due to their versatility and unique properties, they are also responsible for a significant share of the scope 3 emissions in many supply chains. To achieve their company’s climate targets, sourcing managers have to introduce non-fossil alternatives - and they often have to do so quickly.
At the same time, there is high interest in finding solutions that come without changes to the performance of the materials. The motto: change the environmental impact, not the product. Two routes are particularly promising in that regard: renewable and recycled materials.
Keeping Materials in the Loop
Recycling isn’t a new concept. And yet, today’s recycling rates are anything but satisfactory. While plastics are, in theory, quite well suited for recycling, it isn’t always that easy in practice. Conventional recycling technologies are based on mechanical processes. Plastic waste is sorted, shredded, cleaned and then melted and reformed into new products. While this works well for very clean plastic waste, it doesn’t work so well when the plastic waste is rather impure, e.g. through contaminants such as colors, additives or similar materials. At the same time, mechanical recycling faces challenges when the desired products need to be very clean as well - e.g. in sensitive applications such as food packaging - as it usually involves a slight diminish in the quality of the plastic. This also limits the number of times plastics can be mechanically recycled.
However, “advanced” or “chemical” recycling can complement the conventional approaches. It can deal with more impure or mixed plastic waste streams as it basically turns the plastic back into its building blocks, which can then be used to produce new plastics of virgin quality. This comes with two benefits: more plastic waste becomes recyclable - and more sensitive products can be made from recycled materials. The complementary character becomes even more apparent considering that advanced recycling may serve as a reset button for plastics that have been mechanically recycled several times already and suffered losses in quality.
Expanding recycling to achieve circularity by keeping materials in the loop thereby has a lot of potential to tackle both issues associated with plastics: put plastic waste to good use and reduce the need for virgin fossil materials.
Recycling alone won’t be able to solve the plastics challenge though: The demand for plastic is growing. So not only is there a gap to close in the recycling race, the target also keeps moving away. On top of that, recycling always comes with certain losses of material. Thus, even a 100% recycling rate wouldn’t be enough. For the foreseeable future, a demand for new material will remain, but that material shouldn’t be of fossil origin. Luckily, it doesn’t have to be.
Renewable Materials to the Rescue
Plastics are made from hydrocarbons, which today are mostly won from refining fossil crude oil. But this isn’t the only source for hydrocarbons: bio-based oils and fats are in large parts hydrocarbons as well. Various types of bio-based raw materials can therefore be turned into very pure hydrocarbons as well, including waste oils such as used cooking oil or residues from vegetable oil processing, but also animal fats not suitable for human consumption. Through cleaning and treatment with hydrogen, these oils and fats can become bio-based versions of their fossil counterparts that can then be turned into just the same plastics, e.g. polypropylene or polyethylene, to name the most common ones.
As the change in materials happens very far up in the supply chains, there also is no need to change any of the downstream processes and infrastructure. All known materials further downstream as well as the end-products remain unchanged.
What changes though is the carbon footprint of the plastics - and this is due to the fact that instead of fossil carbon, they are based on biogenic carbon. Fossil carbon, if eventually released to the atmosphere, e.g. through the incineration of plastic waste, adds additional carbon to the atmosphere in the form of CO2. Biogenic carbon, on the other hand, originates from the atmosphere already where it was absorbed during the growth phase of the biomass. It thereby doesn’t add additional CO2 to the atmosphere. Hence the lower carbon footprint.
A Life-cycle Assessment for renewable hydrocarbons from Neste shows a reduction in GHG emissions of more than 85% when they replaced fossil hydrocarbons in the plastics industry.
The Short-Term and the Long-Term
While possible solutions to the plastics challenge are technically available, an important question is when they can be implemented and at what scale.
For renewable plastics, the answer is rather simple: bio-based materials for plastics are available at scale already - and so are many applications that make use of them. Neste alone has a production capacity of 3.3 million tons for renewable products, set to gradually increase to 6.8 million tons by the end of 2026. Other large scale producers are active in the market as well. Across the globe, all kinds of plastic applications can be found in the shelves that are based on renewable materials, ranging from diapers to plastic cups, from food packaging to baby pacifiers, from medical equipment to laboratory consumables.
In the long-run, it will be crucial to expand the raw material basis though. Waste and residue oils and fats are a limited resource. It will be important to add other resources to the raw material pool. Algae or forestry & agriculture waste and residues are promising candidates and so are so-called novel vegetable oils. The same is true for Power-to-X, which uses hydrogen and CO2 as a carbon source to produce hydrocarbons.
Regarding advanced recycling, the large-scale commercialization of the technology will require some time still. Various companies are working on large-scale operations. In the case of Neste, a total of 6,000 tons of waste plastic have already been turned into high-quality raw materials for new plastics. The company is currently constructing a facility in Finland that would come with an annual capacity of 150,000 tons by 2025. It’s first steps, but more years will pass before its significant contribution to solving the plastics challenge.
When it comes to companies looking for the best way to combat the plastics challenge in their supply chain, they should consider recycled and renewable materials part of the same equation: instead of choosing one or the other, they should consider combining both to achieve a holistic approach. Using as much recycled content as possible and filling up any additional demand with renewable materials would be the royal road to more sustainable plastics.