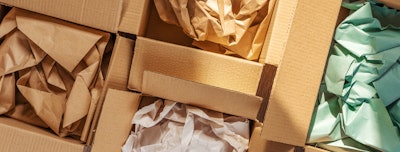
The growth of e-commerce has led to growing concerns about the impact of shipping and packaging on the environment from businesses and their customers. However, businesses often focus on sustainable product packaging while overlooking their shipping practices. Yet, changes to shipment packaging and processes can impact a company's sustainability goals while improving customer satisfaction. Enterprises that give meaningful attention to sustainability through the last mile reduce waste, emissions and cost while improving the unboxing experience for their customer.
Improving the Unboxing Experience
The unboxing experience has become a crucial aspect of e-commerce customer satisfaction. Consumers take notice when they receive products in oversized, poorly fitted boxes with excess filler and waste. It diminishes the experience of opening their packages and immediately raises questions about the company’s environmental sustainability efforts. Organizations that neglect the impact of the unboxing experience on the perception of environmental control risk damaging customer relationships.
A customer’s positive experience with right-sized and minimal packaging can build brand trust around sustainability simply by opening up the box in which their items have been shipped. This one-to-one reinforcement drives the adoption of right-sized packaging solutions, encompassing 2D and 3D packaging approaches. In 2D packaging, standard boxes are cut down to size, while 3D packaging involves using dimensioning and cubing algorithms to provide all three dimensions (length, width and height) for custom-fit boxes. This dynamic approach allows companies to adapt efficiently to varying product sizes and customer needs as products roll off the package line, with minimized waste.
Maintaining Sustainability in a Growth Phase
On the retail side, the growth of online ordering and the limited variance of packaging sizes can lead to operations challenges that are more polluting. Too large boxes using too much filler quickly take up space on a freight truck, which in turn means more trucks creating more carbon emissions. Wrong-sized boxes also pose logistical challenges for shipping and warehousing, and excess cardboard and plastic fillers contribute further to sustainability issues. This inefficient use of resources can inflate costs, negatively impacting a company's bottom line.
Identifying areas where cardboard and other waste can be reduced is often an uncomplicated, actionable step companies can take that will have a fast, positive impact on sustainability goals with the added benefit of improving efficiency by streamlining operations, reducing transportation costs and optimizing the supply chain.
For example, shopgoodwill.com, the e-commerce auction platform of the non-profit organization Goodwill, dispatches hundreds of donated items daily, featuring listings from Goodwill branches nationwide. Goodwill offers an extensive range of products, spanning from clothing to electronics. Any given customer may order a diverse assortment of unrelated items, which presents an ongoing challenge to ensure efficiency in the packing process.
The organization aimed to enhance packaging robustness to reduce the risk of damage, enhance the customer experience and streamline warehouse operations. Since introducing right-sized, automated packaging at their Orange County warehouse in 2017, shopgoodwill.com has not only met these objectives but also surpassed them. With the ability to produce a broader range of box sizes on demand, the necessity for extensive inventory storage of large boxes has been eliminated. This has resulted in improved shipping efficiency, enabling a greater number of items to reach customers without sustaining damage each day.
The Next Step for Sustainability: Light-Weighting
Packaging can be further optimized by implementing lighter weight packaging materials, or “light-weighting” for additional reduction of material used and cost savings. Today, light-weighting is a leading-edge sustainability implementation, but the technology to accommodate lighter weights of corrugate in the automated packaging process is becoming more prevalent. Thinner packaging materials enhance the sustainability benefits of automated packaging like improved utilization of truck space. Lighter-weight materials often have a higher proportion of recycled materials, as well.
Light-weighting can also provide cost savings. While that may seem pretty obvious – less material per box means lower costs – it is imperative to consider package integrity in the design process. If a package can be too easily dented or crushed, that has negative implications for the production and packaging processes, customer experience, product damage during shipment and returns. Designing and testing new materials is imperative to maintain package functionality while improving sustainability and reducing cost.
In conclusion, right-sized packaging enhances the unboxing experience and addresses sustainability concerns by reducing waste and carbon emissions. It optimizes storage space utilization, lowers shipping expenses and contributes to increased profitability. As e-commerce continues to grow, right-sized packaging is becoming essential to meet consumer expectations, reduce costs and uphold sustainability commitments.