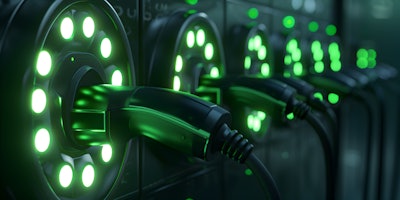
For more than a decade, the promise of environmentally friendly travel created a forecast of change in the automotive industry. Despite these lofty ideals, the transformative shift from traditional internal combustion engine (ICE) vehicles to electric vehicles (EVs) hasn’t panned out as quickly as planned, particularly in North America.
A report by JATO shows that the U.S. and Canada combined for only 13% of EV sales last year, far behind China (51%) and Europe (23%). Automakers must balance investments in ICE and EV production while managing costs, resources, and supplier relationships as the EV adoption picture becomes more transparent.
The Environmental Protection Agency (EPA) recently finalized pollution standards that project to reduce fleetwide average carbon emissions by roughly 50% by 2032, but that’s nearly a decade away. Consumer adoption has lagged behind aggressive goals, particularly in regions lacking adequate charging infrastructure and augmented by significant cost barriers to ownership. This misalignment has led nearly every automaker to revisit their EV strategy, as evidenced by revised sales forecasts and layoffs across the industry.
We are in the midst of the greatest change to the automotive industry since ICE replaced horses and Henry Ford established mass production of vehicles. It should come as no surprise that there is a high level of uncertainty.
The contrasting realities of the concerted regulatory push and slower consumer adoption underscore the need for advanced supply chain planning tools and strategies. The ability to accurately forecast demand, test alternate strategies and respond quickly to disruptions will be crucial for success in this transformative period.
Barriers to EV Adoption
Slow sales figures for EVs and a lack of adequate charging infrastructure have created a two-pronged issue. The National Electric Vehicle Infrastructure (NEVI) program sought to solve the so-called “charging deserts,” but those funds haven’t been widely dispersed yet. ‘Range anxiety’ meanwhile, presents a critical concern for potential EV buyers, as the scarcity of charging stations makes long-distance travel challenging.
Moreover, the high cost of EVs, primarily due to their expensive batteries, has been another significant barrier to widespread adoption. Although battery prices continue to decrease, the upfront cost of EVs is still higher than comparable ICE vehicles. The limited availability of affordable EV models across various vehicle segments has compounded this issue.
Supply Chain Planning Challenges
As consumers grapple with whether or not they want to be early EV adopters, manufacturers are stuck in neutral with supply chain planning challenges. One of the most significant hurdles is accurately forecasting demand and avoiding overcommitting resources to EVs that aren’t selling as well as they were forecast to.
Automakers must maintain the production and supply of ICE vehicles, which still account for most sales, while simultaneously ramping up EV production to meet regulatory mandates and prepare for future demand. Consider the traditional combustion engine, which has roughly 2,000 parts. The tiered automotive supplier community is expansive, and those suppliers also run their own supply chains. EV engines, on the other hand, have only 20 parts in the engine, but the suppliers are just as critical.
To make matters even more complex, the technology which powers EVs is changing rapidly, new batteries and more powerful computers mean that product lifecycles for the current generation of EVs will be much shorter than ICE vehicles.
This balancing act requires tremendous flexibility and agility in supply chain planning and execution. The EV supply chain is still evolving, with new players entering the market and existing suppliers adapting to the unique requirements of EV components. Automakers must work closely with their suppliers to ensure they have the capacity, capabilities and flexibility to support both ICE vehicles and EV production.
Transparency and trust are critical in this context, as automakers and suppliers must share information and collaborate to mitigate risks and respond quickly to disruptions. The recent semiconductor shortage, for example, highlighted the importance of end-to-end visibility and collaboration in the supply chain. Automakers with stronger supplier relationships and more transparent supply chains were better positioned to navigate the crisis and minimize production disruptions.
Leveraging Technology to Ease the Burden
Automotive companies are looking increasingly similar to high tech companies with shorter lifecycles, high demand uncertainty and greater competition from new market entrants. High tech companies like Cisco were pioneers deploying advanced planning technology so it makes sense for automakers to follow the industry’s best practices.
As the automotive industry grapples with the EV transition, advanced analytics and scenario planning tools are becoming increasingly critical for success. These technologies can help automakers better forecast demand, optimize production, and respond quickly to disruptions in an uncertain and rapidly evolving market.
By leveraging artificial intelligence (AI) and machine learning (ML) algorithms, automakers can analyze vast amounts of data from various sources, such as consumer preferences, market trends, and economic indicators, to predict future demand more accurately. This can help them make informed decisions about production volumes, inventory levels and resource allocation, reducing the risk of overproduction or stockouts.
AI and ML can also be key in optimizing product design and features. By analyzing customer data and feedback, automakers gain insights into which features and options are most popular among different segments of the market. This information can guide the development of new EV models more closely aligned with consumer preferences, increasing the likelihood of successful market adoption.
Scenario planning is another critical tool for navigating the uncertainties of the EV transition. Automakers can develop contingency plans and stress-test their supply chains against potential disruptions by modeling various demand and supply scenarios. This can help them identify vulnerabilities and develop strategies to mitigate risks, such as diversifying suppliers, increasing inventory buffers or investing in flexible production capabilities.
Advanced analytics can also drive operational efficiencies and cost savings. For example, predictive maintenance algorithms can analyze sensor data from production equipment to identify potential failures before they happen, minimizing downtime and maintenance costs. Similarly, real-time monitoring of supply chain performance can help automakers identify bottlenecks and inefficiencies, enabling them to take corrective action quickly.
To fully leverage these technologies, automakers must invest in building the necessary data infrastructure and analytical capabilities. This may involve partnering with technology providers, hiring data scientists and analysts and fostering a culture of data-driven decision-making throughout the organization.
By embracing advanced analytics and scenario planning tools, automakers can not only navigate the challenges of the EV transition but also position themselves as leaders in this competitive and dynamic industry. As the market continues to evolve, those companies that can effectively harness the power of data and analytics will be best positioned to thrive as EV adoption takes hold.