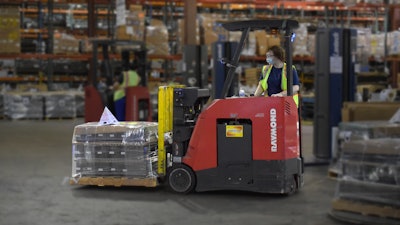
Transportation and industry are thriving sectors of the economy, and are increasingly critical as more manufacturing is brought to the United States and the demand for goods moving through the supply chain grows. From the middle- and heavy-duty trucks on the road to the material handling equipment in warehouses and distribution centers, each has a critical role in keeping our economy moving.
Companies in the transportation and industry sectors are investing in strategies that enable them to responsibly grow their capacity while also minimizing their carbon footprint. Sustainable fleet management can help companies meet our country’s net-zero carbon emissions goals. By taking a close look at the vehicles moving materials inside the facility and =the ones transporting finished products, you can find more energy-efficient practices that can add up to significant improvements in fuel economy, operating costs and emission rates.
The best way to begin is with small steps.
Encourage training and communication
One of the easiest steps to take is driver training. Up to 30% of a vehicle’s fuel efficiency is impacted by driver behavior. Safe driving habits, such as following speed limits and avoiding sharp braking and rapid acceleration, reducing fuel consumption and greenhouse gas emissions and reducing the number of preventable accidents.
Another driver behavior to address is excess idling time. A heavy-duty long-haul truck generally idles around 6 hours per day, wasting more than $20 billion in fuel costs and increasing emissions. To eliminate unnecessary idling, auxiliary power sources can be used to provide power to onboard equipment more efficiently. Auxiliary power sources typically include batteries charged from the electrical grid overnight or recharged while the vehicle’s engine is running.
Unnecessary trips also lead to increased fuel consumption, higher gas emissions and more wear and tear on vehicles. By following optimized routes, on the road and in the warehouse, these losses can be avoided.
Solicit feedback from drivers and operators as they may be able to help pinpoint where the inefficiencies lie. Their day-to-day perspective can provide valuable insight into how to improve productivity.
Optimize routes and schedules
The larger a fleet gets, the more likely inefficiencies will creep in simply because there’s so much traffic.
Examine the paths forklifts take inside the distribution center. Are forklifts criss-crossing the floor rather than following a grid? Do you have too many, or too few, in operation at any given time? Consider using a software solution to ensure your path to pick goods is optimized for your operation.
Map the routes trucks take between the facility and destination points. Are they taking the freeway or surface streets? Are there stops along the way they can make to cut down on the number of trips?
Plan routes efficiently inside and out. Schedule work and establish routes to ensure maximum productivity. Such planning will also allow fleet vehicles to be serviced in a timely manner.
Maintain your fleet
Some of the common contributors of fuel waste and unnecessary carbon emissions are based on vehicle maintenance not being completed regularly. For example, for every 1 psi that tires are under-inflated, gas mileage is reduced by 0.2%. When fleet vehicles are properly maintained and running optimally, their fuel economy increases up to 10%.
Establish a preventive maintenance schedule and service pattern. Ensure that timetable meets the manufacturer’s recommendations and protects the vehicle’s warranty.
Invest in the right parts
Having the right batteries in place is essential for a sustainable fleet.
While you might save money in the short term with low-cost, low-quality motive power batteries, you may find that less time is spent working because they need to be charged more often. High-quality batteries tend to hold capacity for a longer period of time, meaning they are in use longer and are replaced less frequently.
You also want to select the right battery for the application conditions. For example, lithium batteries have greater energy density than lead batteries; however, they don’t perform as well in cold storage applications without the addition of heating packages. Choosing the right battery for the conditions helps ensure the battery lasts longer, reducing downtime and increasing productivity and efficiency.
Whether the goal is to reduce engine running idle times or to support house loads during driver rest periods, selecting the right battery is important to ensure that the operational expectations are met. Heavy-duty commercial vehicles are typically equipped with either standard flooded lead batteries or with the better performing but more costly absorbed glass mat (AGM) batteries. Enhanced flooded batteries (EFB) and their high-cycling cousins are now available in the North American market, offering a high-performing solution with a value-orientated cost. Fleets looking to reduce cost per mile and total cost of ownership while maintaining the electrical system’s performance can find value with EFB and high-cycling products.
Another component in maintaining a sustainable fleet is what you do when parts reach end-of-life. Recycling as much as possible is integral to sustainability. According to the EPA, the recycling rate for lead batteries in the United States is 99%, making them the most recycled product in the country. Almost 100% of the lead in a lead battery is recyclable, and lead can be continuously reused without losing any future performance capacity. The plastics and other casing materials are also recycled and reused. Used battery acid is processed into sodium sulfate, which is used in laundry detergent, glass and textile manufacturing.
Right-size your fleet
The optimal fleet consists of the fewest and most cost-efficient vehicles necessary to meet the company’s objectives. Begin with an audit of what is currently in your operation. A power study can help you understand what is going on with your material handling fleet. It will establish a baseline for energy needs and provide insight into energy consumption and battery health. Performance modeling software can help fleet managers select the right combination of batteries and chargers to fit their needs.
For a transportation fleet, begin by setting benchmarks. Common metrics are utilization, fuel economy and repair costs. Analyze how often and to what extent each vehicle is in use. You can identify excessive spare vehicles by assessing monthly mileage, engine hours and active days. Evaluate vehicle weight, engine size and load capacity to determine if the same job could have been done with a smaller, more fuel-efficient vehicle. Identify inefficient vehicles and begin mapping a replacement schedule. Planning life cycles will allow for more efficient procurement. By deciding when to retire vehicles and acquire new ones, the company can balance current costs and future needs.
Conclusion
Continuous improvement is the key to sustainability. Always look for additional measures that can be taken to move the needle forward. Establish fleet policies and communicate them throughout the organization. Integrate technology to collect relevant data to make right-sizing decisions easier. Once baselines have been established, benchmarks can be added based on goals and objectives.
As advancements in technology continue, more options will become available to achieve a more sustainable, efficient and productive fleet.