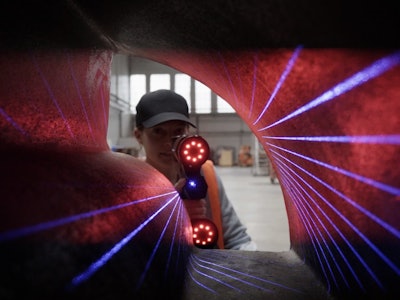
Hexagon’s Manufacturing Intelligence division introduces new handheld 3D scanning technology that complements its broad range of manufacturing inspection devices with unprecedented capabilities for flexible measurement.
The company’s first handheld 3D scanning devices, they enable engineers and manufacturing personnel to easily scan what they need in a wide range of environments inside and outside factory walls. Two new handheld devices, the ATLASCAN Max and MARVELSCAN are ideal for measuring parts in a wide range of inspection environments where metrology has not traditionally been used, including applications in automotive, rail, industrial equipment and general manufacturing, as well as heritage and restoration projects outside of manufacturing.
"Today, manufacturing and engineering teams recognise the value of up-to-date 3D scans throughout the product lifecycle. This means almost anyone might need to perform a metrology-grade scan of a part regardless of their location,” says Pirmin Bitzi, general manager for Portable Measuring Devices at Hexagon. “Our first handheld 3D scanners enable customers to digitalise parts without worrying about fixturing or environmental conditions and MARVELSCAN’s cutting-edge, integrated photogrammetry system aligns to reference targets without the need for stickering. Wireless and ergonomic, these scanners provide a seamless, instant scanning experience from the shop floor to the shipyard.”
Key Takeaways:
- ATLASCAN Max and MARVELSCAN users can adapt workflows on the fly using ergonomic, thumb-operated controls that streamline 3D scanning processes in confined spaces and rugged or outdoor environments. Eliminating the need to access a control PC during measurement, this multi-mode scanning enables different feature types and surface needs to be measured efficiently. For example, users can scan open surfaces with Standard mode, then quickly switch to Fine mode with the on-device controls for higher resolution on intricate features. Crucially, the data collected under these different modes are automatically combined into a single, workable point cloud.
- The new devices also eliminate the need to fixture parts prior to measurement, which contributes to significant time savings and allows greater measurement flexibility. The scanners and parts can be moved freely during measurement, reducing the time it takes to capture complete part data without negatively affecting inspection results. For further productivity gains, the common and time-consuming task of measuring multiple holes and slots is made easier with a hole-flash capture mode that enables instant data capture of multiple holes and slots in the same shot.