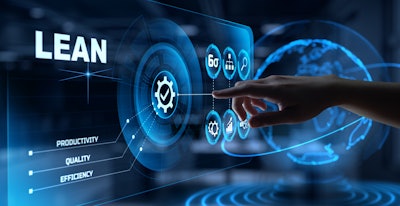
When lean manufacturing was first codified as a system over 30 years ago, it was a revolution in manufacturing efficiency. Instead of pushing staff to work longer and harder, lean focused on refining processes through the lens of value-added vs. non-value-added activities. By reducing the latter, companies could enhance efficiency and minimize overproduction.
Unfortunately, lean has too often been equated with inventory reduction. In fact, it was even blamed for the Great Paper Products Shortage of 2020, even though no manufacturing scheme on the planet could have predicted nor compensated for the public’s irrational excess demand. While inventory reduction is sometimes a result of the Lean process, that’s not the purpose—it’s a byproduct.
Consistency is the goal
The goal of lean is to create consistency in process flow and product quality through standard work. That means identifying, understanding and responding to anomalies and variables: optimizing things you can to mitigate the impact of things you can’t. The rest—speed, productivity gains, reduced waste, cost savings and higher revenue—happen naturally.
That means you can’t treat lean like a point in time—a project with a beginning and end. Many company leaders say, “We did lean last quarter,” as though it operates on a discrete timeline. That’s not how lean works. It’s not a thing you do, but a way of doing business: a consistent, ongoing program of continuous improvement. Lean is never done, and in fact, if you’re not finding new ways to improve, you’re not looking hard enough.
Why lean into lean now
Despite its 30-year history, lean is more important than ever in today’s global marketplace. With the threat of tariffs, supply chain disruptions and labor shortages, companies must be able to optimize processes, cut waste and maximize revenue in the areas they CAN control.
Therein lies the real value of Lean: its universal ability to optimize the current state, to hedge your bets against the unexpected, and provide a foundation for sustainable efficiency, no matter what happens.
The lean mandate for modern manufacturing
Despite lean principles being well established, companies still make major missteps in their implementation that derail success. As we face an increasingly uncertain future, avoid those mistakes by embracing these key tenets of a modern lean strategy.
· Adopt standard work. The Japanese didn’t invent standard work as part of the Toyota Way—this premise has been around since the 1900s as part of Frederick Taylor’s time study strategy, and it was fundamental in Henry Ford’s work. Yet a shocking number of manufacturers still don’t have documented standard work, and without it, they have no benchmark for quality, productivity or troubleshooting. Standard work is the foundation of Lean consistency, and there’s simply no excuse for not documenting processes in an era when cameras can reliably capture every single task on the production line.
· Ask the right questions. Too many companies attack Lean implementation by looking at machine efficiency, utilization, operator productivity, etc.; essentially, they focus on the details instead of the bigger picture. Those metrics are important, but lean success requires a broader view to understand all factors inhibiting flow. For example, instead of asking how you can make a machine run more efficiently, ask why the setup is taking so long. Is standard work being followed? How can you prevent machine downtime or rework? Improving efficiency requires a holistic approach that questions everything in the process.
· Segment, then optimize. Particularly in high-flow areas, you want to ensure high-value tasks are being performed at all times. For example, a welder is most valuable when generating weld beads, not when tending to equipment or gathering materials. Segmenting tasks allows you to break down processes and find an alternative—could you assign a helper or automate part of the process to keep that welder welding?
· Streamline steps. A surprising number of plant processes are cumbersome and inefficient, but they’re deeply embedded—they’ve always been done this way and no one has considered changing it. In several assembly line settings, I’ve observed operators repeatedly adding components to a machine. They would dump material into the machine, then walk to another area to get more, return, and add that, and then go to yet another location for the next batch. This kind of workflow wastes valuable time. Materials should be staged or stored near the machine to reduce unnecessary movement. While each extra step might only add a few seconds, those seconds quickly add up to hours, which can have a significant impact on overall productivity.
· Not all business is good business. Too many companies are willing to perform all manner of customizations and one-off runs for customers, thinking they have no choice if they want to keep the business. But if it’s costing you more and you’re losing money, do you even want that business? Not every order is worthwhile, and if it costs more, at the very least you need to charge more. Name your price and put that decision about whether it’s worth it back on your customer. Don’t be afraid to turn down work that disrupts flow and hinders your productivity and value generation.
· Balance digitization with human expertise. Many companies assume digitizing will supercharge their productivity, and it’s true that sensors, meters, and vision systems can spot anomalies better than any human. This can help you collect data faster to troubleshoot a problem, but it can’t solve it. That requires human domain expertise and root cause analysis. Beyond just getting back up and running, root cause investigation and prevention are essential in lean, otherwise the same disruptions will arise over and over. And with so much data being collected, you need expertise to separate signal from noise and decide what’s worth making adjustments to your flow based on risk/benefit considerations.
· Culture is essential. Leadership and accountability are hands down the biggest obstacles to lean implementation. Rarely is frontline resistance a hurdle—most operators will do whatever you ask, and often you’re solving problems they’ve known about forever. But reluctance to hold people accountable, enforce standards, and proactively problem solve are cultural issues that no amount of technology or strategy can solve. Effort is everyone’s personal responsibility and leaders must set expectations for themselves and their teams.
While the early days of lean may have focused on isolated productivity and efficiency improvements, modern lean strategy requires a broader, macro view. Companies must examine processes comprehensively, be more strategic around customer needs and open minded about what’s required or possible.
Instead of addressing issues piecemeal to achieve an aggregated result, modern lean strategy requires working backward from the desired outcome to create optimal conditions necessary to achieve it.