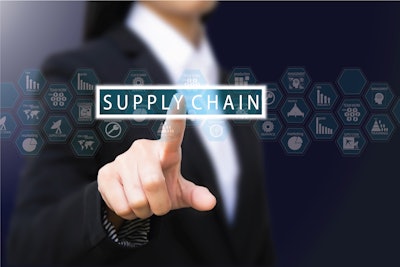
The Boeing 737 MAX is one of the world's most widely used and known commercial aircrafts, yet in recent years various models—such as the Next Generation (NG) and MAX series—have been under intense scrutiny for their design, manufacturing issues, and operational safety concerns. Boeing's latest crisis involving loose door bolts on aircrafts has sparked worldwide controversy, decreasing trust throughout the supply chain as further issues unfold. These inspection woes not only raise concerns about passenger safety but also lead Boeing and others in the aerospace industry struggling to contain and remediate these safety issues and their attendant business risks. Manufacturers throughout the aerospace supply chain must engage in the worrying inquiry whether specific pieces and systems that had not been previously identified or adequately addressed might also have defects.
With a defect crisis also comes massive reputational risks that can tarnish a large manufacturer's reputation and affect the OEMs and suppliers who are forced to pick up the pieces. This piece will address the unique market pressures facing the aerospace industry that contributed to the Boeing crisis and discuss what manufacturers can do to avoid similar defects and their fallout.
Supply Chains are Under Immense Pressure
As economies normalize and grow following the huge disruption of the pandemic, many industries are experiencing demand outpacing supply, leading manufacturers to look for ways to work quickly while maintaining or increasing quality. There is pressure on supply chain teams and OEMs to build more efficiently to meet demand, especially in aerospace, as the travel industry rebounds post-pandemic.
For tier 2 or 3 suppliers, pressures subsequently flow down from the OEM through the supply base. And with increased volume of orders comes increased pricing pressures on the manufacturers, so OEMs might look to make sacrifices to get all orders completed at a lower unit price.
In addition, the manufacturing industry is facing challenges with modernizing its business processes and attracting the talent necessary to serve its customers as the prior generation of manufacturing labor enters retirement.
At the macro level, all of this increases the risk of a manufacturing defect. Manufacturers’ end-users, such as airlines, are relying on faster and more efficient production at a cheaper cost—all while expecting increased quality and traceability capabilities from their supply chains.
The Ripple Effects of a Defect
In aerospace supply chain risk management especially, robust processes and quality control are of heightened importance. In the event of a suspected defect, manufacturers must pinpoint and contain issues within the supply chain as quickly as possible with undisputable evidence of where the problem arose and that it has been contained.
Proving undisputably how a defect happened and that it has been mitigated can be an onerous process, however. With Boeing’s 737 MAX bolt crisis, for example, mitigation would involve finding not only the exact issue with the door and bolt but the exact batch where the defective part came from. Mitigation would also involve tracking if the door and bolts were made by an OEM, subcontractor or another supplier. The supplier responsible must go through tremendous efforts to prove exactly where in the supply chain the issue came from.
Manufacturers across industries are sometimes using traditional business processes, such as physical records, yet still need to accurately track their supply chains through all levels.
Optimizing Processes with Technology
Luckily, technology can aid manufacturers in both avoiding defects and in mitigation efforts if errors do occur. AI visual inspection tools enable manufacturers to respond to demand pressures by increasing the efficiency of their inspection processes. AI tools can drastically reduce inspection time and virtually eliminate manufacturing errors. In addition, as manufacturers face labor shortages or the retirement of experienced workers, AI visual inspection can put the equivalent of hundreds of years of inspection experience to work, even as manufacturers contend with talent pool challenges.
In addition to ensuring quality from the production line, manufacturers looking to avoid becoming a part of the next Boeing-like crisis should ensure they are modernizing their tracking and recordkeeping processes. AI tools can also help with this process. Manufacturers should automate their inspection processes with tools that automatically serialize each item. This will help ensure that if a defect occurs either upstream, downstream or in a manufacturer’s own facility, it can be tracked down and isolated. Manufacturers leveraging technology can then efficiently show the kind of “undisputable” proof that an issue has been resolved that high-stakes manufacturing contexts demand.
While manufacturing comes with a human error element that will never go away, technology is the clear path toward navigating inevitable supply chain woes and complexities in the future. There are several robust tools that manufacturers can put in place to adapt to demand pressures without compromising quality or taking on more risk.
By adopting the right technology, manufacturers can mitigate the risk of defects and close gaps while not raising costs in this highly turbulent period in supply chains.