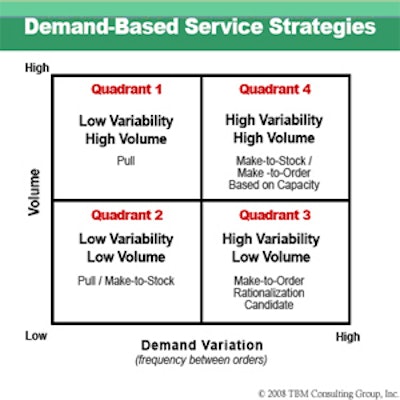
Over the past several months we have seen much written about the difficult economic times and the focus on becoming "green." While Lean continues to focus on the relentless pursuit of waste, several new tools have been added to the Lean toolkit to help improve energy footprints and free up working capital. A third key recent focus area of Lean implementation is applying these concepts across the value chain.
Energy Kaizen Events Really Pay Off
Certainly, widespread societal demand exists for energy conservation to preserve the environment, but manufacturing leaders know that energy reduction also is crucial to their companies' long-term survival. By ignoring the call to conserve energy, manufacturers risk losing the gains reaped from years of LeanSigma and other continuous-improvement efforts. Energy is essential for goods production, but compared with other widely consumed raw materials, energy has become one of the costliest and most volatile. Therefore, stabilizing energy-consuming processes and removing as much waste as possible become the mandate to remain a globally competitive manufacturer.
By applying Lean activities to energy use, an average facility can reduce its energy consumption by up to 20 percent, of which 30 percent can be achieved by making procedural and behavioral changes. Manufacturers such as agribusiness, food and beverage, paper and packaging, and other continuous process industries can potentially double these reductions because their processes operate around the clock and tend to be more energy intensive. For example, one continuous-process manufacturer working to cut energy consumption achieved a minimum 10 percent reduction with each process change.
Manufacturers that reduce energy usage do more than lower their utility bills. A focus on reducing energy consumption:
- Creates a reputation of social responsibility locally and globally, which makes a company's products more attractive to customers;
- Makes a more attractive partner to new and existing customers that have environmental-sustainability mandates for suppliers; and,
- Ensures compliance with current or future government regulations or industry guidelines regarding energy consumption and/or carbon emissions.
Develop Service Strategies Based on Demand Segmentation
Demand segmentation is a tool that has recently become a key component of Lean implementations. Most approaches to production planning treat all products the same. By analyzing and segmenting products, a company can optimize planning, control and manufacturing. Plotting the volume and variability for each product segment can lead to more predictable and responsive production processes, while reducing inventory at the same time. Demand segmentation will determine, for example, if a product should be made using a "pull" system, if it should only be produced on a made-to-order basis, or even if it should be discontinued altogether.
A demand segmentation initiative will look at production volumes, historic inventory levels, shipment records and point-of-sale data if they are available. Simply overlaying these data on a graph can make it obvious for everyone to see how promotions, seasonality and other market factors influence demand and production processes. Once these influences are understood and changes are implemented, companies should expect up to 30 percent improvements in inventory and 10 percent or greater improvements in operating margin from addressing under-performing products.
Create Competitive Advantage by Implementing LeanSigma across the Value Chain
Traditionally, manufacturers have started their Lean implementations on the factory floor. Some may then use Lean on their business processes. Few work on the links in their value chains that touch customers, distributors and suppliers because such work can be complicated, risky and difficult to tackle. Developing a Lean value chain means addressing four key links: demand management, order fulfillment, business planning and scheduling, and supply management.
Demand management helps you see true customer demand. It allows you to forecast at the product family and stock-keeping unit (SKU) levels so you can better plan resources and capabilities. Customer point-of-sale drives execution and replenishment. Through demand segmentation, you understand the volume and frequency of demand patterns, and you shape demand by taking advantage of more agile order fulfillment. This means addressing customer-facing policies such as promotions, pricing structures and delivery frequencies that create demand volatility. Taking the volatility out of the demand pattern helps you lower capital and capacity required, improve service and reduce inventory.
Lean order fulfillment improves the efficiency of order entry and processing, warehouse design and operations, packaging, the distribution network and logistics management. By applying Lean to order fulfillment, companies require less inventory, reduce their distribution costs, improve put-away and picking capabilities, and develop distribution points based on their customers' locations.
Creating flow throughout the value chain requires connecting all links and synchronizing them to serve customer demands. A robust business planning and scheduling process aligns every part of the company with customer requirements. Production smoothing and daily sequencing leverage lead time and stock to deliver the right products at the right time based on actual consumption.
The heightened focus on supply chain management over the past decade has helped companies improve the quality and on-time delivery of supplied parts. Lean supply management builds on these successes by aligning supply relationships and flow to deliver value to your customers. Supply management involves key processes that promote flow from your suppliers, build strategic supplier relationships, improve receiving and warehousing, and reduce costs. It develops clear commodity and sourcing strategies to control purchasing costs. It streamlines your sourcing and contracting process to develop supplier partnerships.
With today's difficult economic conditions and the increasing focus on being more environmentally friendly, it is time to step up the game in Lean implementations. Apply Lean techniques to energy usage to identify and eliminate energy wastes to reduce consumption and become "more green." Conduct demand segmentation to quickly identify and address service strategies and product line performance to improve your working capital situation. Finally, expand Lean beyond your manufacturing operations and eliminate the wastes in material and information flows used to support value creation for your customer. Stepping up the intensity and focus in these new areas will reap significant benefit for your organization.