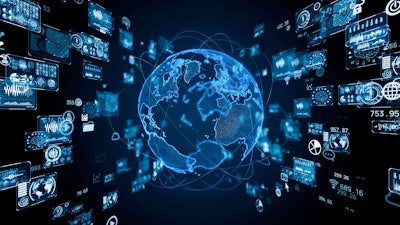
Visibility in the supply chain is critical to the success of any business. Traceability is expected to become the standard across most industries within a few years. Strategic products—such as those related to human and animal health, products subject to government taxes and high-value goods—are leading this shift. Regions with sustainability regulations will enforce the adoption of solutions that improve circularity, energy efficiency, recyclability and durability, such as the Ecodesign for Sustainable Products Regulation in Europe.
Product owners and management in large companies are increasingly facing economic losses and brand reputation challenges due to counterfeiting and diversion in the supply chain. The term "diversion" covers a variety of scenarios, including trans-shipment, promotional bulk purchases, smuggling (illegal product imports), unauthorized distribution, resale of expired goods, diversion of free samples and theft. In industry terminology, diversion is also referred to as the parallel market or gray market.
Traceability can be approached from two different perspectives. Solution providers typically fall into two categories: those focusing on traceability from raw materials to finished products and those concentrating on traceability from finished products to the end customer.
1. Raw Material Traceability
The supply chain is indeed complex, particularly because what constitutes a final product for one company can serve as a raw material for another. Take papermaking as an example. The process begins with the extraction of components such as wood. The wood is first shipped to a distribution center and then transported to a factory where the paper-making process takes place. The factory produces paper, which is considered the final product for that company. However, this paper becomes a primary component for other companies, such as label providers.
Following this logic, a label becomes a primary component for a wine producer, who will apply the label to a bottle of wine. Thus, the final product evolves through several stages: starting as a roll of paper, then becoming a label, and ultimately, a bottle of wine.
For label traceability, specific details about the roll of paper and the ink used are required. When ink packages are received, they must include essential information such as the order number and product-related data, including color, production date, expiration date, product name, description, raw materials used and potentially much more.
Label information is typically entered into the system used by the label converter. These systems are commonly referred to as Enterprise Resource Planning (ERP) systems and will store all relevant data.
2. Finished Product Traceability
The supply chain for Consumer-Packaged Goods (CPG), Fast-Moving Consumer Goods (FMCG) or life science finished products presents a different narrative. These products refer to final goods that a customer will directly use, such as bottles of wine, perfumes or antibiotics.
The key distinction lies in the potential for more efficient traceability if we are able to mark products individually. This approach enhances traceability by enabling tracking at the individual product level rather than just at the Lot level. Lot-level traceability can be more challenging to supervise and may hinder the execution of efficient recalls, for example.
An important concept to consider is aggregation, which involves associating individual serialized units with other units under a serialized parent package. Examples include cartons to bundles, bundles to cases, and cases to pallets. When finished product traceability incorporates aggregation, it provides the product owner with full visibility of their products throughout the supply chain.
This level of traceability is critical for combating parallel markets and counterfeiting. By leveraging aggregation and serialization, it becomes possible to identify the location of a product at any given time. This visibility allows product owners to determine where in the supply chain improper activities may be occurring and to take corrective action effectively.
3. Traceability from Raw Material to Customer
In previous sections, we observed several key differences between raw material traceability and finished product traceability. Currently, the market primarily offers solution providers that specialize in either one area or the other. While there are software solutions capable of managing the entire process, these systems often fall short in terms of scalability and comprehensive functionality.
Although multiple systems can communicate and exchange data effectively, having a single, integrated system that consolidates all business information is theoretically more efficient. However, integration can be both costly and challenging to maintain, as it often requires ongoing updates to remain functional and aligned with business needs. Additionally, some industries impose specific validation requirements, further complicating the process.
4. Enterprise Resource Planning vs. Track & Trace and Their Integration
This section revisits a previously discussed topic, but with a specific focus on the software systems involved post manufacturing. On one side, we have Enterprise Resource Planning (ERP) systems and on the other, track and trace systems, which often include Packaging Execution Systems (PES).
ERP Systems:
The adoption of ERP systems has increased, not only for controlling raw material details during production but, in some cases, to provide feedback on supply chain activities post-manufacturing.
Advantages:
- (+) Unified Platform: A single provider can likely fulfill all requirements, reducing integration issues as the data resides within the same platform.
- (+) Master Data Management: ERP systems consolidate all Master Data, including Lots, Orders and Raw Material details.
Disadvantages:
- (-) Limited Capabilities: ERP systems often lack robust solutions for print and vision systems, as they are not designed for these specific tasks. Integrating with specialized software can be challenging.
- (-) Limited Rework and Exception Handling: ERP systems typically offer minimal support for rework scenarios and handling exceptions.
- (-) On-Premises Limitations: Some ERP solutions operate on local site servers, reducing visibility and connectivity with other devices and systems throughout the supply chain.
Track & Trace Systems:
Track and trace systems have been widely adopted for manufacturing and supply chain operations, especially in industries like pharmaceuticals, where serialization and aggregation are mandated.
Advantages:
- (+) Proven Reliability: Track and trace systems have been successfully implemented for years across global regions with varying regulatory mandates and operational needs.
- (+) Native Support for Serialization and Aggregation: These systems are designed to handle complex printing and vision inspection requirements, natively supporting serialization and aggregation processes.
- (+) Cloud-Based Connectivity: Cloud-based solutions integrate easily with mobile devices and external systems, enhancing visibility and connectivity.
Disadvantages:
- (-) Integration Challenges: Track and trace systems often require integration with other systems to retrieve orders, raw material details and other essential data.
The choice of systems must be evaluated on a case-by-case basis, as recommendations from experts will depend on the User Requirements Specification (URS) and the budget allocated to the project.
Full traceability encompasses the entire product lifecycle—from raw materials to the final manufactured product, delivery to customers, and even recycling. Currently, available solutions are often split between ERP systems (which manage raw materials) and track and trace systems (focused on finished products). However, integration between these systems is expected to advance, leading to future-proof solutions capable of managing even both aspects—before and after manufacturing—more efficiently.
It is important to recognize that track and trace is not a single project but an ongoing program. Successful implementation will require collaboration across multiple departments within the organization. To minimize risks and complications, it is strongly recommended to involve Subject Matter Experts (SMEs) from the outset.