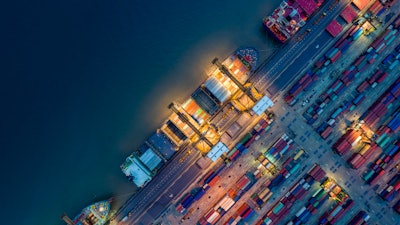
To say things have been difficult for businesses these past few years would be a dramatic understatement. The COVID-19 pandemic created challenges up and down the supply chain, and businesses are still grappling with the fallout from shortages and other disruptions today. The pandemic served as a wake-up call for many businesses that had not adequately planned for this level of supply chain volatility—and addressing that problem has become a high priority for organizations across nearly every industry.
The pandemic made it clear that businesses cannot take supply chain stability for granted. Disruptions are inevitable, which means planning for them is essential. It is increasingly important for businesses to focus on building a resilient supply chain—one capable of withstanding the many pressures and demands of today’s economic landscape. That means understanding the nature and scope of those challenges and overcoming them through a strong, varied, and sustainable network of partnerships.
The Impact of Recent Supply Chain Challenges
The supply chain problems faced by businesses over the past several years are varied and diverse. One of the most visible problems was a component shortage—specifically, the semiconductor shortage. For a significant period of time, it was difficult for many technology companies to get their hands on components critical for manufacturing, which led to long product lead times and significant production delays. The severity of the shortages led many businesses to build entirely new strategies around component availability and risk management.
The back-and-forth pull of globalization and protectionism has also been particularly volatile in recent years, with new laws and regulations dictating which components can and cannot be used within certain jurisdictions. Events like the war in Ukraine have had a disruptive effect on global markets as well. Natural disasters, too, have had an impact on everything from manufacturing to transportation. All of these factors combined to increase the financial pressure on businesses, too, driving up costs and adding new logistical challenges. Sometimes these problems could be overcome by paying a premium price, but for small and mid-size businesses (SMBs) in particular, this was not always an option.
When faced with challenges like these, businesses aren’t just looking to compensate or break even. Modern businesses can’t simply tread water—they are expected to grow, and grow quickly. That means they need to not only overcome these challenges but come out stronger on the other side. It means they need to be agile, always prepared to adapt when the unexpected happens. And for most companies, it means they can’t do it alone.
Building a Strong, Partnership-Based Supply Chain
Some businesses believe that shoring up their supply chain is best accomplished through vertical integration, but the reality is that trying to do everything yourself often puts you at a disadvantage. Vertical integration can be a strength, but it also has its drawbacks—namely a lack of flexibility. Other businesses choose to embrace a partnership model. Rather than directly owning and operating production assets, these companies choose to forge strong relationships with vendors and contract manufacturers.
Working with outside partners allows businesses to increase and decrease production capacity as needed across multiple jurisdictions, making it significantly easier to both scale the business and expand into new markets without needing to invest in entirely new facilities. Building a diverse list of partners also helps insulate the business from economic hardship: the loss of one supplier doesn’t necessarily spell disaster if you have multiple other partners to turn to. This makes it easier to overcome a disruption impacting a specific locality or component.
This is a key point. Becoming too reliant on any one partner or supplier is a risk—after all, what if something happens to them? Having second-source suppliers is critical, but so too is designing products in a way that prioritizes both flexibility and availability. If a certain component is hard to obtain, can the product be designed in a different way without sacrificing its core functionality? It’s necessary to consider the risk inherent to every component a product uses, and to segment the supply chain based on that risk. If certain components carry a high design risk or would be difficult to replace, it’s important to be proactive about creating a strategy to mitigate that risk.
Looking Ahead Together
Perhaps the partnership model’s biggest advantage is that it forces companies to prioritize planning. When working with partners, being predictable is critical. That means sharing information (a street that, hopefully, goes both ways) and engaging in forecasting together. Different partners may have access to different information, and working with them may provide you with a more complete picture of the future. Certain supply chain partnerships may provide trend analysis, benchmarking, and other critical data specific to their industry or locality. A supplier with their finger on the pulse of a certain industry may even be able to anticipate disruptions that would otherwise blindside you.
Of course, you don’t need insider information to anticipate some of the disruptions likely to be heading our way. Geopolitical instability isn’t going to change, and regulatory factors are always a concern—particularly for companies operating in multiple regions. But here, too, local partners can be very helpful when it comes to understanding what new regulations may be coming and how to comply with them. Collaborating with legal and compliance teams throughout the supply chain can help minimize the potential for regulatory disruption.
Other factors, such as sustainability, will continue to play a role as well. More and more businesses are looking to limit their impact on the environment through initiatives like the United Nations Global Compact, a voluntary pact among CEOs from around the world promoting practices like sourcing recycled materials and decreasing their carbon footprint. A growing number of companies are setting science-based targets as they work toward greater sustainability, and it’s important to understand how different partners plan to address these looming challenges. It may even spark ideas for your own business.
Stronger Together
Building a resilient supply chain comes down to three things: be proactive, be predictable, and always be looking to grow.
Being proactive means always looking to the future. It means not just responding to crises, but anticipating them, planning for them, and overcoming them. A proactive company is never resting on its laurels, but always leaning forward.
Predictability means keeping surprises to a minimum for any company you work with. That means keeping open lines of communication up and down the supply chain, and planning together to overcome challenges. Combine predictability with proactiveness, and the result is stability.
And finally, maintaining a growth mindset is key. When planning for the future, it’s not enough to break even. Building strong partnerships throughout the value chain will allow your business to keep the focus on its core mission, keeping critical resources where they belong and setting you up for future success.
There’s a reason “we’re all in this together” became a mantra during the pandemic—it’s true! The supply chain is never easy to navigate, and there will always be challenges. But embracing a partnership-based model and working together to identify, plan for, and overcome challenges is the most important way to build a strong and resilient supply chain.