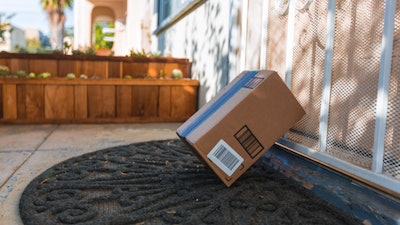
The Coronavirus disease (COVID-19) pandemic has put an unprecedented strain on the national and global supply chain, toilet paper and hand sanitizer shortages included. It’s easy to blame shortages on consumer panic and hoarding, but the root cause is one the industry experiences even during times of normal consumer behavior, just now exacerbated by the crisis.
Delays and restrictions
Typically, suppliers and retailers have built in agreements to ensure that shipments get from place to place at precise times. Yet even under normal circumstances, this isn’t always the case due to issues like human error, inclement weather and more. Now add the challenges of managing a supply chain during a global pandemic. For example, cities and countries across the globe are implementing time window restrictions on when commercial vehicles are allowed to cross borders or enter city centers, resulting in unanticipated delays and making estimated time of arrival (ETA) calculations near impossible.
While a 60-minute delay at a port of entry or loading zone may not seem like a major factor in overall delivery time, these seemingly inconsequential periods of time can pile up and create a ripple effect, resulting in delays of several hours or even days. The same way a single flight delay can lead to a headache for travelers across multiple cities, one delayed shipment can cause a ripple effect and completely throw off a supply chain.
Beyond the bottleneck of materials and goods, dynamic events and delays create frustrations across back-end offices and technology teams, leaving supply chain managers in the dark and rendering ETAs tremendously inaccurate.
Transparency along the chain
Today’s pandemic is unlike any other in recent history. Every aspect of the modern supply chain is being stress-tested, and the industry is being forced to accelerate its digital infrastructure investment. In the short term, suppliers and retailers are fighting to maintain operations. But, there will also be an opportunity to step back, assess the situation and audit the tools needed to create real-time, end-to-end visibility throughout the supply chain, during times of crisis and beyond.
Two aspects define end-to end-visibility. The first is process visibility, which lets suppliers and shippers know where shipments and goods sit within various stages of the transportation chain. This form of visibility (enabled via electronic data interchange, or EDI) provides management with updates as a shipment progresses through the chain, and most importantly, when process milestones vary against the plan. It’s when these variances occur that the second aspect of end-to-end visibility comes into play.
The second is physical visibility. Enabled by GPS and telematics data, physical visibility allows managers to see in real-time where shipments are located on a digital map. Typically, when a shipment doesn’t meet a specific process milestone within an expected timeframe, managers will quickly turn to physical visibility to figure out where the shipment is stuck and determine how to expedite the process. Once the shipment clears the process bottleneck, using the physical location, the shipment ETA can be re-calculated based on real-time traffic and weather conditions.
In addition to real-time physical visibility, managers can collect, aggregate and analyze historical GPS data to identify trends and patterns across the entire transportation. Having this historical “visibility” allows managers to identify and mitigate pockets of inefficiency as well as account for seasonable variables like weather or tourism-related traffic in the summer.
What can we learn from this?
As the supply chain slowly regains normalcy, we can conduct root-cause analysis on the data generated throughout this period and begin gleaning insights on how to create more efficient processes for future times of volatility. As it stands, we’re learning in real-time, though the data is already actionable and robust, given the volume of vehicles moving across the network every day.
Beyond tapping this refreshed set of historical data to influence scenario planning, retailers and suppliers must integrate real-time capabilities into their everyday processes. Through continuous ETA calculation, teams can make quick decisions on how to allocate resources to prepare for arrival. Whether it’s preparing equipment for docking or ensuring that there are enough workers to unload supplies, real-time visibility helps teams better prepare for the transfer of goods and shipments.
Coronavirus and beyond
This crisis has uncovered a number of vulnerabilities throughout the broader supply chain and logistics industry; namely, a general lack of agility to address heightened product demand in tandem with increased traffic barriers. Because relevant historical data doesn’t yet exist to guide response at the current state, we’re collecting an entirely new set of data to reference later on. Eventually, we will amass enough intel to help inform improved processes and resource management in the future.
To move forward, we must prioritize full resiliency and visibility along the supply chain. While the crisis is certainly not behind us, the industry can implement the lessons learned throughout the process to create a stronger and more efficient supply chain overall.