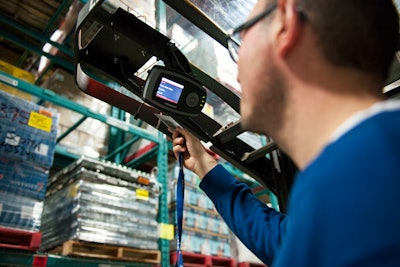
As a supply chain executive, questions about increasing return on investment (ROI) are always at the forefront of your mind. What are quick yet long-term ways to cut operating and manufacturing costs? How can you optimize your lift truck fleet and reach maximum productivity? Are you running as efficiently as your competitors?
Knowledge is power. Fortunately, with today’s technological advancements, it’s becoming much easier to gain real-time information about your fleet and operators’ performances. One key innovation leading the way in the manufacturing and supply chain industry is telematics systems.
All companies collect data on profit and loss, ROI and other key metrics that ensure their businesses remain stable and profitable. It’s the same with telematics for our industry. For example, telematics systems can provide in-depth lift truck data to help reduce impacts, manage growth and monitor fleet and operator behavior.
Whether you have been running with telematics systems on your trucks for years or you are weighing cost versus ROI, here are some benefits of implementing a system that you should consider.
Baseline Identification
You cannot improve what you don’t know. If your warehouse team has not been consistently tracking fleet utilization, operator performance, impacts and scheduled maintenances, it is more difficult to measure opportunities for improvement in such key areas. Implementing telematics systems on your equipment can be a cost-effective way to set a baseline. A baseline report will help identify outliers—hidden costs and missing hours—that are impacting your company’s bottom line.
This visibility into pain points and growth areas can be the information you need to optimize operations and drive productivity across your warehouse. Once you have a baseline set, it’s time to identify your facility and operating inefficiencies and determine opportunities for fleet optimization and cost savings.
Right-time Maintenance Savings
For years, it was a common industry best practice for facilities to adhere to preventive maintenance, which entailed scheduling truck upkeep every 90 days, regardless of truck usage. The expectation was that performing regularly scheduled maintenance would help reduce or avoid unexpected breakdowns and costs incurred when a truck is not in operation.
What many manufacturers are moving toward is predictive maintenance, which does not follow a predetermined calendar schedule for fleet servicing. This technique relies on directly monitoring the equipment performance during normal operation to anticipate possible failures based on operating parameters exceeding established tolerance thresholds. The expectation is that, because powered industrial equipment is operated very differently between customer sites, associated service intervals will also vary greatly. Therefore, some preventive maintenance intervals may be too long based on the way the equipment is used within a facility. On the contrary, some preventive maintenance intervals may result in over-servicing trucks, leading to unnecessary expenses. Telematics systems provide real-time monitoring of operating parameters so warehouses can use predictive maintenance best practices to keep their equipment running smoothly and efficiently all the time.
A recent study by The Raymond Corporation of a company with an 88-truck fleet provides a good cost-savings example of how predictive maintenance can put money back into your warehouse budget. Using preventive techniques, Raymond monitored scheduled maintenances within a 90-day interval to calculate deadman hours per truck. Raymond’s iWAREHOUSE telematics system helped this company determine that only 15 of 88 trucks had more than 500 deadman hours, and 20 trucks had fewer than 250 deadman hours. The metrics from the telematics system calculated that 25 percent of the company’s estimated 352 yearly scheduled maintenances could be avoided—equating to approximately $10,000 in cost savings annually.
Cost savings will vary depending on the size and usage of your fleet, but the monetary and equipment benefits offered by predictive maintenance can offer long-term advantages for your business.
Fleet Right-Sizing—and Right-Typing
In addition to right-time maintenance cost savings, the data aggregation telematics systems offer can expose patterns of equipment inefficiencies and assist with how to right-type your fleet. Operating with a larger fleet isn’t always the answer. A right-sized and right-typed fleet drives productivity and efficiency. Telematics systems can help assess which trucks are working the hardest and which trucks can be removed from the fleet based on utilization data.
Here is a real-world application of how implementing telematics systems at a company’s facility resulted in positive ROI. After nine months of using telematics systems, a company with 76 trucks reduced its fleet to 67, removing one counterbalance forklift, one orderpicker, three pallet jacks and three swing-reach trucks. The telematics system captured data for slow and peak operations times, and based on these analytics, the company right-sized its fleet resulting in strong ROI. Reducing its equipment by 12 percent led to approximately $72,000 in cost savings, which includes the telematics system monthly fee, truck maintenance and staffing expenses.
Another aspect of fleet right-sizing that telematics systems can help with is determining when it is better to rent or buy equipment. Telematics systems monitor peak operations seasons and can determine when you may have heightened equipment needs. For example, telematics systems data helped the above company realize it had nine rental trucks it did not need for most of the year. Right-sizing your fleet to fit day-to-day needs and renting equipment when necessary will save on maintenance, operator and truck costs.
Impact Reduction
Fewer impacts can lead to reduced costs. This straightforward supply chain concept is not news to you. However, you may find that when you evaluate operational costs, it can be challenging to correlate a direct cost to impact. At a high level, a metrics report may show that product is being moved quickly in and out of the warehouse. What may not be visible on the reports is that, while operators are moving quickly, you’re losing $5,000 in damaged equipment or racking repairs, for example.
Impact costs not only account for damaged equipment or parts of the facility, but also man-hours spent inspecting the scene, resetting the vehicle, filing documentation and retraining or hiring new operators. With the cost of truck repairs, as well as replacing any goods that were affected, restocking and addressing any driver injuries, expenses can add up quickly.
Telematics systems provide visibility into how often these impacts are happening, key areas in the warehouse where accidents are occurring and impact frequency per operator and per truck. Additionally, the data shows high-impact zones that may be due to blind spots, rough areas on the floor or staging with bad corners that are leading to severe truck damage.
Compliance Cost Savings
Can you calculate how much time your operators spend on Occupational Safety and Health Administration (OSHA) checklists each year? We can. Automating OSHA checklists with telematics systems can save operators roughly six minutes per checklist, which would otherwise be spent by the operator filling out truck and warehouse information, reporting equipment metrics, delivering the report to the clerk and returning to the floor—which significantly adds up over time.
For a company that performed 153,535 paper checklists on 2,362 trucks—spanning more than 20 facilities—over the course of a month, the cost of operators’ time equaled roughly $307,000 a month. Assuming an hourly wage of $20 per operator, this equates to more than $3.7 million per year spent completing OSHA checklist
Time is money. Automating this process by electronically filing checklist results through a wireless telematics system helps put time back into your operators’ schedules, which can be reallocated to more value-added tasks.
Behavioral and Performance Metrics
Telematics systems also provide cost savings by improving operators’ accountability and behavior. Often, when operators know performance-based data is being collected, warehouses experience a reduction in equipment impacts and an increase in operator productivity. Most telematics systems can provide custom reports to measure and track specific key performance indicators to tailor the system to your business and operator benchmarks.
From appropriately scheduling truck maintenance, right-sizing and right-typing your fleet to streamline efficiencies, reducing impact and automating OSHA compliance checklists, telematics systems are worth the investment. And if you already have telematics systems, ensure you’re using the technology and its rich data sets to their full potential for maximum ROI. With today’s increasingly shortened production deadlines, tracking and analyzing your warehouse data will help your company remain stable, profitable and ahead of competition.