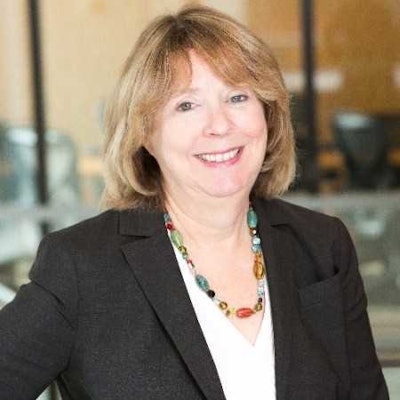
Labor Cost. Those two words can bring a range of emotions such as frustration, angst and determination from those that have to manage their organizations labor costs. The Bureau of Labor reported that productivity fell 4.4 percent and the unit labor costs increased by 4.8 percent in the third quarter of 2017. It's not surprising that more are looking for creative ways to manage the labor spend.
Over the years many have provided solutions to manage their labor more efficiently, but few have suggested looking at the hourly time data as a potential area of focus. This might be the place that can give insights into employee behavior which, when modified, has shown to provide between .5-2 percent savings in an organization’s hourly spend, according to Deloitte analysis. For even smaller businesses, that number can impact their bottom line.
This can be done by tracking their hourly workers' time through an automated solution. While there are many solutions available with various capabilities, the consistent theme is that all have a database with detailed information on their workers paid, unpaid, worked or not-worked time. By analyzing these data points, trends can emerge which may not have been apparent when looking at timecards.
Looking at the data from a different lens has provided some interesting insights when applied regardless of the vertical. In a large manufacturing client, the findings included:
- Several hundred thousand missed punches over the course of one year. While each Supervisor knew they had a few employees who consistently forgot to punch in or out for the start of their shift, there was no awareness of the magnitude of the issue. By having the employees focus on clocking in and out, there were both soft savings (due to Supervisors not having to spend time researching and fixing the time) and hard savings as the employee’s time may be overstated due to estimating when they actually started work.
- Supervisors changing over a hundred thousand time codes. This issue was due to the Supervisors modifying an employee’s time to add an overtime code or remove an overtime code. Interestingly, remediating this may not result in savings and could actually show an increase due to hours that should have been paid at overtime. However, eliminating the manual edits and depending solely on automated rules to calculate regular or overtime pay, can reduce the potential of employees challenging their pay either internally or externally and the perception of non-compliance.
- Lack of approvals by Supervisors or Employees. Producing a manual check is costly and any reduction in the number of manual checks will likely produce hard savings. A key factor in producing that perfect paycheck is to have the hours going to payroll be accurate. By having the employee attest to their hours being accurate and then the Supervisor consistently approving the time, it reduces the chance of incorrect hours being passed to payroll. The approval metrics are available and will show who is or is not approving on a regular basis.
- Reduction in Overtime. Data in the time system can also reveal when employees may have increased overtime based on consistently clocking in or out a few minutes early or late. While looking at individual employees did not reflect a material savings, however, looking at the entire hourly population will show the true picture. If there shows a trend of early or late clocking in that is not related to approved overtime, a change to behavior or the time system can result in a significant reduction in overtime.
These are just a few examples, but others such as how is call-in pay processed, scheduling efficiencies and the assignment of overtime are also areas that may have opportunities to reduce labor costs.
The key is to think about what data you have and how that data can provide transparency into your policies, technology or processes. Those insights then transcend into a conversation about what modifications can be initiated to reduce labor cost without affecting headcount and using the workforce more efficiently. You have the data, now use it to help combat those labor costs!