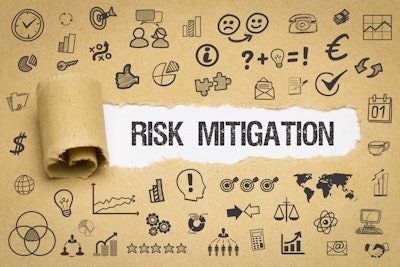
In an increasingly complex supply chain and material handling environment, keeping unforeseen variables low — and efficiencies high — is crucial to running a smooth, lean operation. From intuitive warehouse design to the implementation of highly effective, highly efficient software and technology systems, creating a standardized workflow around the twin principles of risk assessment and mitigation can enhance returns while fostering a work environment that champions employees and warehouse managers alike.
To understand how technology and software systems can enhance operations, industry leaders should first look to diagnose the organizational inefficiencies affecting their operations. Then, they should examine how applying the right techniques to minimize those lapses can allow their organization to reinforce best practices in a comprehensive, effective way.
Understanding Supply Chain Inefficiencies and Their Impact
The greatest contributors to increased supply chain interrupters often go unnoticed. After all, most potential operational threats are a combination of multiple factors in a dynamic operating environment that work in concert to slow operations and reduce efficiency, making them difficult to diagnose and even harder to solve.
Take, for example, warehouse congestion, which is a common challenge that can dramatically reduce productivity if left unaddressed. At the surface level, congestion may seem simple to contend with. But congestion stems from multiple potential weaknesses, including equipment malfunctions, human error, outdated software and legacy technologies. From cyberthreats to training issues to seasonal workforces that make standardizing business operations more difficult, the process of understanding and mitigating bottlenecks is more complex than tackling individual variables in a vacuum.
For these reasons, identifying deficiencies in a modern warehouse setting demands a proactive approach that involves identifying and preventing underlying challenges before they become a larger, more complex problem.
Using Technology and Software to Proactively Identify Inefficiencies
While the nature of supply chain management has undoubtedly grown more complex over time, technology-driven solutions designed to enhance efficiency make it easier to manage the complexities.
For instance, consider the problem of human error as a result of suboptimal training. One of the most significant advancements in warehouse operations involves the implementation of virtual reality (VR) simulator technology that can help new trainees develop the skills needed to succeed on the warehouse floor without impacting day-to-day operations. VR simulators serve as flexible, scalable teaching tools that rely on advanced technology to help workforces become more efficient and expand operator skills, creating optimized conditions for all employees.
Tools such as integrated equipment detection and notification systems and operator tether systems can similarly help warehouse operators enhance their work environment. Systems like these use intelligent speed limitations, real-time object detection, operator notifications and more to enhance employee environmental awareness even in high-traffic areas. In this way, equipment detection and notification systems continuously highlight and reinforce crucial standards and operator best practices — intuitively educating employees and expanding talent operation wide.
Finally, capturing data through telematics systems can help warehouse managers better understand and tackle operational inefficiencies. From increased visibility to better equipment maintenance to the greater efficiency of people, warehouse processes and operations, data collection and the analysis of this combined data are powerful means by which businesses can reduce immediate flaws and prevent future scenarios at the same time.
The Future of Technology and Risk Mitigation
These new, powerful emerging technology solutions all point to an important growing trend — a shift toward holistic data collection and implementation that champions optimization while simultaneously streamlining processes.
After all, data is only powerful if properly analyzed and implemented, which is why warehouse managers should look to create an ecosystem of connectivity and productivity that reinforces the integration of equipment, labor, technology and data collection systems. Additionally, warehouse managers should understand how the analysis of combined data reported from different elements in their warehouse ecosystem provides the story of how efficient their warehouse is operating. Just as conditions for deficiencies are interconnected, so are identification and mitigation systems — solving operational challenges in a highly impactful way.
The Business Benefits of Mitigating Risk Through Enhanced Technologies
The key to success for businesses navigating the future of supply chain management lies in viewing new technologies as integral components in developing a comprehensive strategy that promotes operational excellence. From VR simulation technologies to equipment detection and notification systems to integrated tether systems, telematics and more, adopting new, better solutions to long-standing operational challenges can help organizations get ahead now instead of playing catch-up down the line.
Indeed, leaders who refuse to view risk management as more than a means for avoiding costly setbacks are ignoring a crucial business benefit — the benefit of leveraging software and technology solutions to create resilient, efficient and lean warehouse operations ready to meet future industry challenges. By remaining updated on new technology trends and solutions, businesses can look forward to a strengthened framework that addresses warehouse issues for comprehensive, effective and transformative results.