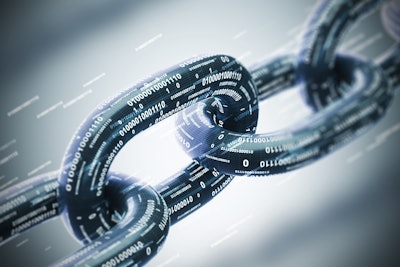
The Coronavirus disease (COVID-19) has exposed the fragility of global supply chains like never before. Dramatic shifts in demand patterns have affected the ability of companies to react swiftly, as was seen with the now famous global toilet paper shortage episode. Revenue flows are severely impacted leading to job uncertainties, and limiting consumer’s power and willingness to spend. According to the International Monetary Fund (IMF), this pandemic is likely to trigger “the worst recession since the Great Depression.” Store closures are widespread. Even larger firms have struggled to survive. Such business failures, on demand or supply side, can pose serious financial risks and endanger supply chain integrity.
Firms have no choice but to navigate this unprecedented turbulence and haze to best of their ability. Like a good surfer facing choppy waters, companies have to be flexier, and must quickly adjust their pace and course on the fly to dampen the impact. They must remain financially efficient to not only conserve cash, but also to emerge stronger post COVID-19. While these businesses confront both variabilities and uncertainties in their supply chains, here are some strategies that organizations should evaluate to reduce their impact on business continuity.
Variability
Risk pooling. This risk management technique widely used in insurance industry is one such avenue that can dampen the impact of variability on supply chain costs without compromising on customer service levels.
Location pooling. Shifting a portion of inventory from end nodes to fewer central locations can pool the risk by reducing variability and lowering costs. Firms can also benefit from economies of scale due to such centralization. On the other hand internal transportation and handling costs may rise. Balancing these trade-offs can present a solution that can lower overall cost.
Virtual inventory pooling. Similarly, companies can leverage Information Technology to virtually pool their inventory across multiple locations to lower the impact of variability. For instance, many firms use customer’s address to map the nearest fulfilment location. Instead, real time inventory visibility across locations can allow dynamic selection of best location to serve the demand. This pooling approach can reduce the risk of stock out, reduce cost and free up capital.
Capacity pooling. Health risks due to the pandemic can affect production plans due to sudden non-availability of key human resources. Having a flexible talent pool by cross-training the workforce in key skills can improve utilization of human capital and prevent expensive disruptions in manufacturing.
Adding a little flexibility to the manufacturing process is another pooling technique to improve responsiveness to the erratic demand and reduce cost. Auto-manufacturers like GM generally use flexible assembly line designs to build multiple models per line. Likewise, a product can be built at multiple plants or assembly lines, or sourced from multiple suppliers. This flexible manufacturing approach, when configured in right way, can improve capacity utilization, enhance agility and lower long term costs, especially when demand has high variability.
Parts commonality. Proper product design can help increase parts commonality, while retaining product’s core value proposition. Without commonality, the demand variability for a part will be same as that of the finished product. But, if the part is used in multiple products, its demand will depends on aggregated demand for all parent products. Consequently, its demand variability is reduced due to “risk pooling” effect. Further, such commonality can help consolidate supplier base, drive economies of scale and benefit from better predictability of aggregated demand.
Visibility
Above strategies focused primarily on internal strengths and efficiencies. It is equally important to improve visibility beyond organizational boundaries to detect disruptions that have potential to cascade through supply chains, and cause operational, financial and reputational damage.
Supply chain risk intelligence. According to the 2019 Supply Chain Resilience Report prepared by Business Continuity Institute, 74% of significant supply chain disruptions originated either at Tier 1 or Tier 2 suppliers. The associated risk is amplified further with COVID-19 due to its global spread and painfully bumpy recovery. Firms realize the value of developing good visibility deep into their supply base to continuously assess their risk exposure. Flex uses big data analytics, artificial intelligence and visualization to receive real-time alerts so that contingency plans can be promptly activated to limit the impact.
Product demand intelligence. Traditional time series forecasting models rely heavily on long term history to predict the future. This approach may less dependable during this crisis when companies are witnessing unseen demand patterns. Instead, planners must rely more on recent history to predict short term forecast. Forecast quality can be further augmented with adequate cross-functional collaboration and better information sharing with major customer accounts. Incorporating market intelligence through demand sensing, big data analytics and artificial intelligence into forecasting process can also aid in proactive detection of demand abnormalities.
Collaboration. Current volatility necessitates frequent communication and better collaboration with key trading partners for identifying and mitigating risks in timely fashion. Internally, cross-functional war rooms can ensure a speedy and cohesive response.
Digital integration. Production delays and transportation issues have affected supplier’s on-time performance. Accurate and timely information exchange through digital integration between trading partners can easily lessen the downstream impact of such issues. Tight integration can vastly increase automation, enhance data quality and increase communication speed.
While it is still unclear how the post-COVID-19 world would look like, current supply chain practices will certainly be scrutinized, leading to some long-lasting changes. Above strategies are few practical measures that can not only help firms to be resilient to safely sail through the choppy waters and chaotic undercurrents, but also help them emerge stronger to compete in the new world.