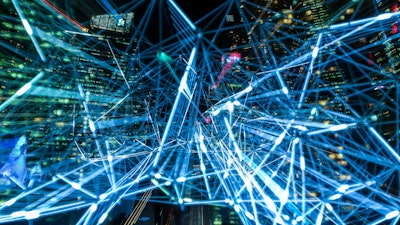
Supply chain companies are adopting machine learning at such a pace, it won’t be long before the process is commonplace. Across the industry, companies are using machine learning to integrate systems, forecast demand, provide real-time visibility on shipments and improve efficiencies in last-mile deliveries, among a host of other uses. According to a report by Gartner, the use of artificial intelligence (AI) and machine learning was one of the top 2020 trends in the supply chain industry, and one of the top technologies giving companies a leg up over the competition.
Machine learning is a complex technology. In the most basic sense, machine learning is the process of taking an immense amount of data and analyzing it to make smarter decisions. The goal is to save businesses money and generate greater profits, in part by better serving end customers. One example of machine learning in everyday life is image recognition. Facebook uses image recognition to identify and tag people in photos. In image recognition, algorithms are used to identify facial features and compare those features to facial images collected in a database. Similarly, in the supply chain, algorithms are used to measure everything from weather patterns and rail schedules to SKU profiles and stock-out alternatives. Those hundreds or thousands of data sets can be compared and cross referenced to predict various outcomes, from inventory levels to estimated delivery, with higher accuracy than ever possible.
A study published in February by Deloitte showed that “more intelligent networks enable organizations to reduce the time between collecting data and take meaningful actions.” Only 40% of survey respondents said they are actively using AI, but those who are moving toward increased digitalization will outperform their competitors. For example, the use of IoT-enabled trucks is expected to reduce transit time by 50%.
Accenture's SynOps platform offers forecast inventory demand to help companies order weeks in advance, using machine learning.Accenture
Machine learning in supply chain
Several software companies are helping supply chain businesses become more digital. The time to dip a toe in the water to tentatively test out the efficacy of the latest technology is over. Instead, it’s time for the industry to commit to the shift, technology experts say.
“Machine learning is shifting the perspective of the supply chain,” says Manish Sharma, group chief executive at Accenture Operations. “Traditionally, supply chain models tend to approach improvements too incrementally and leaders in the supply chain industry need to think bigger.”
He points to Johnson & Johnson as one example of a supply chain success story.
“They re-tooled their supply chain to adapt to fluctuating consumer and production demand patters, with an end-to-end digital ecosystem fueled by deep data science, analytics, and automation,” Sharma says.
Gartner recently placed Johnson & Johnson at No. 3 on its Supply Chain Top 25 List for 2020 for its ability to continuously improve supply chain practices to meet demands during the COVID-19 pandemic. The company scaled up its manufacturing to meet demand for ventilators, converted manufacturing lines to produce hand sanitizer and has taken on its own vaccine efforts.
“Due to the pandemic, they’re now thinking bigger,” Sharma says. “Businesses are now looking to augment human plus machine workforces by integrating machine learning and other automation technology into supply chains. Helping drive productivity and improve employee experiences, companies are already seeing dividends and plan to scale their artificial intelligence platforms in the coming years. From the consumer perspective, businesses can now utilize their supply chains for greater visibility into sourcing and shipments to enhance the experience for them.”
During the pandemic, Accenture repurposed its SynOps platform to maintain real-time visibility into supplier inventory and automatically identify alternatives for its customers. Used as a procurement tool, the platform scrapes the web and uses machine learning and natural language processing algorithms to find suppliers that might be able to step in with missing materials or components.
Ware2Go uses tech, data and machine learning to integrate OMS, WMS and TMS systems.Ware2Go
Digital-first approach
Ware2Go uses tech, data and machine learning to integrate order management system (OMS), warehouse management system (WMS) and transportation management system (TMS) technologies.
“Ware2Go’s technology-first approach to supply chain is powered by machine learning, which is a novel idea in our space, but it shouldn’t be,” says Steve Denton, Ware2Go’s CEO.
Data is the most powerful asset in the supply chain, he says, and integrating OMS, WMS and TMS with multiple data sets helps customers with three common issues:
- Decide which warehouses to stock with inventory according to geoproximity to their biggest customer bases, warehouse capacity and required warehouse or transportation capabilities.
- Determine how much inventory to carry and how to distribute it, what may be missing from (or extraneous to) their SKU profile and when they should reorder for optimal inventory carry costs and supplier bulk order discounts.
- Forecast demand based on historical sales and patterns of seasonality. This helps merchants align their marketing spend with available inventory to get the most out of seasonal peaks without experiencing stock-outs or backorders that lead to frustrating customer experiences.
Technologies like machine learning allow companies to ramp up marketing to their best end customers by geo-targeting and increasing service levels in those regions.
“The supply chain industry can actually create demand through geo-targeting their best customers with increased service levels and overall lower shipping and fulfillment costs,” Denton says. “Not only that, but last-mile delivery efficiencies actually lower our merchants’ overall cost to serve and increase their margins. Combined top-line and bottom-line revenue growth adds up to significant business impacts for SMBs (small and mid-size businesses) and high-growth merchants.”
Machine learning allows companies to automate decisions and processes, allowing for greater speed and efficiency. In some cases, that has allowed smaller businesses an advantage over larger enterprise companies that are unable to react as quickly to market and supply chain changes, he says.
“Now that Ware2Go is equipping these SMBs with a supply chain that moves as fast as their digital sales channels and access to enterprise level data in the way of demand forecasting and network and inventory planning, they’re really well positioned to move in on retail market share in a way they never were before,” Denton says.
Another next-level machine learning advance is providing companies with SKU-level views of profitability.
“This is huge for SMBs who may have been basing their price structure off of educated guesses or broad stroke industry comparisons,” Denton says. “With a full understanding of their overall cost to serve and its impact on their bottom line, they’re able to scale quickly and with confidence by serving up the right products at the right price points to just the right customers.”
MHS Global uses machine learning in its robotics systems. The company recently developed an order-fulfillment cell that can build more than 40,000 orders a day with two robots.MHS Global
Robotics and machine learning
Machine learning is used to ultimately enable more efficient shipping with fewer manual touch points, says Brandon Coats, MHS’ global product manager for robotics and vision.
“We use machine learning in our new robot singulation cells, as well as in vision-based parcel counting applications,” Coats says. “Additionally, our Helix WES/WCS (warehouse execution software/warehouse control software) and Insights IoT platform can leverage AI in the warehouse to predict and group orders in fulfillment solutions, as well as leverage data acquired in the field over the lifecycle of the product to predict failure ahead of an actual downtime event.”
MHS uses unsupervised learning within its IoT to understand outliers in data and combines that information with its traditional Six Sigma baselining approaches to predict failures ahead of a downtime event.
“The value proposition here is that most logistics sites and many warehouses run short sort and operational windows to achieve exactly the number of material handling motions needed per day,” Coats says. “This means that if a portion or all of the system goes down during the shift, then significant loss in production can be incurred and, in some cases, result in millions of dollars in lost revenue. Predicting failure ahead of the event allows for planned downtime and minimized cost in maintenance events.”
MHS uses unsupervised learning technology to change future pick strategies, while supervised learning is used more broadly.
“The ability to run a low-cost, hardened industrial camera while retrieving package locations and counts in each frame helps to essentially re-control parcel singulators, which improves singulation profiles and reducing reliance on labor,” Coats says. “We use low latency neural networks in our robot parcel singulation family, too. These neural nets allow for the same functionality as just mentioned, however, they also output, with a bit more computation, a robot target for a pick, along with proper tool selection for more frequent first-time pick success. This strategy makes robot singulation a segment with a value proposition that is viable today and will increase over the next three to five years as national rollouts of disruptive technology occurs while throughput capability experiences a likewise upward trend.”
The company recently developed an order-fulfillment cell that can build more than 40,000 orders a day with two robots.
“This robotic cell can grasp 36 items is a single pick and batch build four orders at a time,” Coats says. “The value proposition here is consistent rate capabilities that far exceed human capability, by leveraging LEAN principles to minimize buffer and deploying buffer on the hand and on the fly to optimize overall flow.”
Kinaxis' platform uses machine learning to augment business decisions on the planning side of the supply chain.Kinaxis
Augmenting, not replacing, the human
At times, when there is mention of robotics in the workplace, people channel their inner Paul Bunyan. They worry their jobs will be replaced by robots, similar to the way Paul Bunyan’s ax-wielding, tree-cutting days came to an end after he was outworked by a steam-powered saw.
But, Polly Mitchell-Guthrie, who co-founded the third chapter of Women in Machine Learning and Data Science, says the goal with machine learning isn’t to replace humans, but to augment humans. Mitchell-Guthrie is vice president of industry outreach and thought leadership at Kinaxis Inc., a supply chain planning company, which develops automated machine learning, known as AutoML, designed for supply chain planners who are not experts in AI and machine learning.
“AutoML is a technological development in the machine learning programming space that we embrace significantly because it allows us to build software that does not require a data scientist and it's aimed at that planner,” she says. “We're trying to empower the planner and the planner with the math, and we use the technology platform that enables you to do that.”
Supply chain planners are essential to the process because they understand the context of data sets, Mitchell-Guthrie says. This is especially important when the supply chain is disrupted, as it has been during the pandemic.
“Interpretability really matters,” she says. “When your mathematical models are disrupted, because history is not predictor of the future, you have to do something different.”
Machine learning solves some of the disruptions but at a certain point, the models need to be reviewed by an experienced planner who knows how to shift the algorithms.
“That's why we want to say, ‘let's keep the human in the equation,’” she says. “They have so much domain expertise, let's figure out how to leverage that because one of the things that machine learning doesn't do very well is it can't understand context. Math is great and using volumes of data to find patterns, but it can’t understand context.”
The Kinaxis software improves forecast accuracy and helps prepare and cleanse the data.
“There’s a lot of feature engineering,” Mitchell-Guthrie says. “The data preparation, the data cleansing, the feature engineering; those are very time-consuming parts of the process. We have automated that. In our demand sensing work, it’s about looking at the historical forecast to see what other external signals to bring in to help us determine how to add value.”
John Galt Solutions' machine learning software predicted with accuracy the 2020 holiday shopping spending increase.John Galt Solutions
Predicting the rush
In 2020, retailers were left wondering how much of a holiday demand to expect during the pandemic. Unemployment was high, but people were not spending their discretionary incomes on restaurants or travel. Would have money for the holiday season, and would they spend that cash on gifts?
Using machine learning, John Galt Solutions was able to accurately predict, in October 2020, the upcoming boost in holiday sales.
“We predicted that it would be larger than normal and start earlier than normal because even though the unemployment rate at that point had peaked at 10%, there was all this cash sitting in people’s pockets,” says Matt Hoffman, VP of customer success at John Galt. “We were (forecast) modeling with the number of seats in restaurants, on the number of airline miles flown year over year and we were modeling consumer confidence and the unemployment rate and a couple of other features in our machine learning.”
Holiday spending was up 8.3% in 2020, according to the National Retail Federation. That’s well above the industry forecast of a 3.6% increase and 5.9% higher than 2019.
“It’s interesting because you cannot run through that sort of information unless you’re using machine learning,” Hoffman says. “People can very much now see the value of machine learning and these types of advanced analytics.”
Machine learning helped one client, an ice distributor and manufacturer, analyze its routes in terms of supply and demand. Using numerous data sets, the company was able to remove specific stops along the route depending on weather, allowing the company to visit other stops earlier. The changes resulted in a 50% reduction in stock-out, 75% reduction in unnecessary deliveries and 20% productivity increase in deliveries, Hoffman says.
“Leveraging IoT, point-of-sale and weather data, we built automated machine learning algorithms that optimized the transportation route delivery system and moved to intra-day responsiveness,” he says.
Blume Global's digital platform captures and cleans data from Blume Network sources into a single virtual and highly available place, powering logistics and supply chains globally. Data is accessible to authorized users via Web user interface, REST API’s and standard and custom electronic data interchange formats.Blume Global
Cleaning data with machine learning
Clearly, the right data set in the right situation at the right time can make a big difference when using machine learning in the supply chain industry. Obtaining correct data from different points along the chain, from factories in southeast Asia to seaports and rails can be a herculean task, says Glenn Jones, general vice president of product strategy at Blume Global.
“The supply chain is notorious for sending you bad data,” he says.
The factory in Asia may not have the technology to estimate manufacturing shipments or the arrival of raw materials to produce goods.
“Sometimes you have to assess what's happening, or you can look at the trucks that are backing up and track the trucks, but you can't track the factory,” Jones says. “Then, when it gets to the seaport, there are delays, the ocean liners, give you one story, the terminal gives you another story.”
Blume Global built an algorithm that looks at each of these sources of data and based on a historical analysis, cleans the data coming in. As the self-learning system receives new data, it makes automated decisions. It uses weather data to understand and deal with rail and trucking route delays. Data cleaning is the process of inputting information into the platform that the algorithms can use to make decisions.
“It gives us the best picture we think we can get,” he says. “And it learns, so the next time there is a weather pattern, it is better able to calculate the delay.”
Machine learning is used within the platform to establish predictive ETA, or a prediction for estimated time of arrival.
“If you ordered something from Wayfair and it’s not in stock, as a customer you want to know when it’s going to arrive,” Jones says. “There are a lot of factors that impact when it’s going to arrive. We’ve got an algorithm we wrote that’s heavily machine learning, that will constantly update that ETA.”
The platform also uses machine learning to make recommendations for how to fix problems and recognize opportunities in the supply chain. Depending on several factors, the system may recommend switching from rail to truck to ship the product to its destination.
“When the cargo on the boat lands in the port of Los Angeles, the standard mode might be rail and rail will take about four or five days to get to Chicago,” Jones says. “If you want the cargo in Indiana, then you’ve got to put it on a truck and run it down to Indianapolis. It might be better, if you’re behind schedule, to, when it lands in L.A., to put it on a truck and truck it directly to Indiana.”
The company is keeping an eye on emerging technologies, such as autonomous trucking, he says, which will likely significantly alter the supply chain in the future.