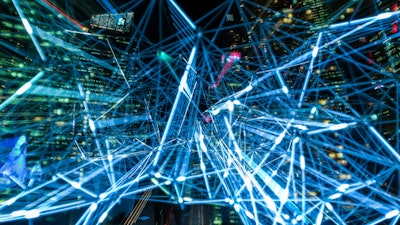
Digital transformation is driving an industrial renaissance that centers increasingly on customers and their experience with products and services. In addition to product design and possibilities of customization, the supply chain plays a supporting role. By optimizing it, custom goods can be manufactured and shipped as fast as possible. The time is more than ripe for companies to pursue the digitalization of their supply chain. Only then can they make the right decisions to improve performance, increase profitability and secure competitive advantages.
Many enterprises are still too cautious in their approach to digitalization. According to findings from the Hermes Barometer on the subject, only 8% of companies have a digitalized supply chain. And, 42% of those questioned realize that it is necessary to create digitalized processes in the supply chain. However, only 27% of logistics decision-makers participating in the study could come up with a concrete implementation strategy.
The Capgemini Research Institute study, The Digital Supply Chain’s Missing Link: Focus, produced a similar result. It showed quite a gap between what is expected and what is reality when it comes to digitalizing of the supply chain. Nearly 50% of companies questioned count digitalization of the supply chain as one of their Top 3 priorities, but 86% of them are still struggling to actually implement projects beyond the testing phase.
Digitizing the supply chain calls for a plan
Before moving forward with digitalization plans, evaluating the processes used to-date can help companies assess how competitive and profitable they can be in the future too.
First, companies must decide which key performance indicators (KPIs) are the focus. Are you aiming to reduce costs sustainably? Or to optimize processes? Does special attention have to be given to service performance for the customer? Or should the workload of production machines be optimized and the time to retrofit a plant be minimized?
Next, a company must not immediately digitalize its entire supply chain – it is often enough to optimize the supply chain at the right points first in order to markedly improve the process overall.
Another important aspect to consider is transparency of data, which can be achieved by evaluating whether important information is accessible to everyone involved in the supply chain and how data transparency can be created for those without access. .
Once a company considers these elements, it will be ready to begin digitalizing its supply chain.
Footing for long-term decisions
Such a platform is ideal for advancing and implementing the digitalization of the supply chain because in addition to a central data pool, it offers applications for computer-aided support in decision-making processes. That helps a company assess its supply chain from different angles and optimize it accordingly. The emphasis to-date has been mostly on deciding between optimization of costs and service to the customer. For example, if service is a priority, minimizing costs will tend to be second priority; whereas if you want a sustained reduction of costs, service will usually have to make sacrifices.
A good example of that is the automobile industry. In many cases, price is most important. As a rule, there are only a few model versions that are delivered depending on demand, and these cars are relatively inexpensive. Given the small choice of models, automotive production can be maximized and delivery optimized. Looking at the configuration possibilities of high-priced cars, there is a maximum selection.
Supply chain: Make-to-stock or make-to-order
Today, there are two classic concepts in the supply chain—make-to-stock (MtS) and make-to-order (MtO). Depending on how a company manufactures its products, the so-called order penetration point varies in the supply chain.
In the case of MtS, the order penetration point is often at the end of the supply chain because products are manufactured based on the general demand. They are then delivered to sales points where specification of a single product is thus not feasible.
MtO usually refers to easily planned products for which the customer does not expect fast ad hoc delivery. Production does not start until the actual customer order is placed, like in the building of a bridge. The order penetration point is right at the start of the supply chain and there is no production without an order. Specific customer wishes for car configurations can also rate as MtO depending on the scope and level of detail – but here, the order penetration point is in the middle of the supply chain. Some components are produced MtS, but the final assembly of the individual configurations is MtO.
MtO places a heavier demand on processes in a supply chain and this is where digitalization of the supply chain plays a substantial role. In planning the supply chain, many enterprises today must decide on a trade-off between costs and service. In the MtS domain, the costs are usually reduced maximally during the production process. Alternatively with MtO, individualization and service to the customer are priority over cost.
Customization: Challenging the supply chain
The biggest challenge for companies today, and even more so in the future, is that customers and their experiences as consumers will be an increasing focus. Based on a survey, conducted by Cite Research for Dassault Systèmes, 80% of respondents said they wanted to purchase personalized products, as is already possible for some products today. Additionally, 84% wanted fast delivery services, regardless of their location. This means sizeable demands for companies and their supply chains, illustrating why time is of the essence for companies to promptly address the digitalization of their supply chain operations.
Success through supply chain reform
Many companies today are at a turning point with their supply chain. To achieve long-term success, companies should consider a unified business platform that centralizes all data sources in one spot. Processes can then be planned and performed cross-enterprise, enabling holistic decisions to be made.
Future demands and needs can no longer be satisfied without an integral and digital adaptation of the supply chain. By exploring, questioning and optimizing processes that already exist, companies will see success.