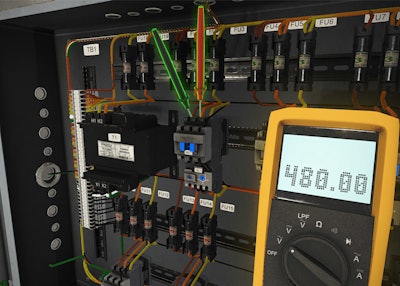
With automation and artificial intelligence changing the business and pace of the supply chain industry, many of the skills needed to operate the facilities of the future are shifting. Attracting and retaining the best staff can be challenging given the current manufacturing skills gap caused by retiring Baby Boomers and an insufficient pool of available workers to replace them. This is why many in the supply chain industry are engaging their employees through new tools, such as simulation and gamification techniques.
Tech Tools for Training
With unplanned downtime costing industrial businesses over $50 billion annually, knowledgeable and well-trained maintenance professionals are critical to supply chain operations running smoothly. Having a maintenance department that can solve problems, mechanical as well as electrical, can avoid extra expenses, such as lost productivity and changing parts unnecessarily. However, Deloitte’s manufacturing skills gap study predicts that over two million jobs are likely to stay open in the next decade due to the lack of skilled workers.
More than half of the companies surveyed by the McKinsey Global Institute said they would have to help build the workforce of the future, either by training or hiring new workers that have the right set of skills. For those supply chain companies looking to train either new or existing workers, a good program that is cost-effective and ensures employees develop the skills their jobs demand will be an imperative.
Simulation is one training technology that is gaining popularity through virtual reality (VR), augmented reality (AR) or computer devices. For example, the Raymond Virtual Reality Simulator is used to train new and existing lift truck operators working in warehousing and distribution facilities. LogistiVIEW uses AR to help warehouse and distribution center workers do their job. Through computer vision software, workers wearing industrial smart glasses, such as Google Glass, can see a series of lights and hear voice instructions directing them on how to fill orders.
Users interacting with simulation tools can practice on realistically-replicated equipment and explore different scenarios and even make mistakes. None of the plant’s assets need to be down for training purposes, and the activities are done in a safe way without risk of injuries or equipment damage. By using instructional 3D simulation tools, a more immersive experience can be provided for those learning how to operate advanced automated equipment and solve electrical maintenance problems on the plant floor. When users interact with a 3D representation of a plant environment, they can make observations, such as if there is water on the floor, and understand how actual conditions can affect operations. This tool provides a powerful and effective way to develop critical thinking of maintenance personnel.
Game On!
Simulation tools that employ cutting-edge graphics and video game techniques can also use gamification methods to effectively train. Gamification is the concept of using game design elements to motivate participation and engagement with some existing entity, such as a website, app and brand.
Currently, some of Amazon’s fulfillment centers are testing a gamification program where games are displayed on small screens at employees’ workstations. When robots move shelves to a workstation, lights or screens direct the worker to the items to fill the particular order. Scanning devices track the completion of tasks and can spark competition among employees, teams or even floors to achieve the best performance. Those workers who have the higher scores get bragging rights and “swag bucks” that can be used to purchase Amazon-branded clothing and other items.
Amazon is trying out this program in order to make its fulfillment center jobs less mundane and monotonous — a criticism the company has been under fire for recently. Plus, if the program works successfully to engage employees, higher rates of productivity could be one of the positive outcomes.
In training applications, gamification elements can take the form of leaderboards, merit badges and buttons to encourage peer competition and motivate both new workers and existing staff to learn more skills. However, these “serious games” must be designed properly so that trainees are not interacting with just a game, but with actual concepts.
Using gamification methods can be useful for onboarding a younger generation in particular. Millennials and Gen Z has grown up with video games and are comfortable interacting with them. Additionally, games can be helpful with retraining older workers who might need extra training to keep up with the advanced automation in plants. Finding ways to inspire and motivate older workers who have a wealth of knowledge, but might be resistant to doing things can be challenging. However, training programs that make learning stimulating and engaging can help with the upskilling process.
For operations that are becoming more automated, new equipment is just one part of the digital transformation. People will still be needed to work in these facilities, but they might not have the skills necessary to do so. Investing in employees and having an effective training program will be crucial to prepare supply chain companies for future challenges.