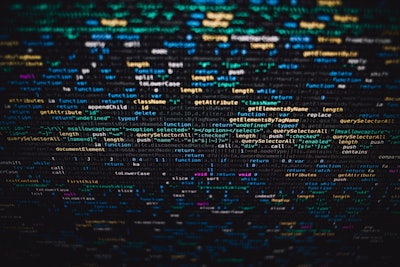
Companies around the world are confronted by a worsening shortage of talented supply chain professionals.
Demand for supply chain talent is soaring, yet the supply is dwindling as seasoned Baby Boomer employees retire. A study by DHL, the global logistics provider, estimates that demand exceeds supply by an alarming 6:1 ratio.
According to the report, one reason could be that supply chain careers are lacking in excitement, making it harder to find, attract and retain talent.
That’s not surprising as tech-savvy digital natives enter the workforce. Gen Z’ers and millennials relish roles in which they can flex their creativity while using advanced technology. They’re accustomed to interacting with digital agents like Siri or Alexa, and have the ability to summon data on demand through Google, Amazon and other popular apps.
Yet much of supply chain management relies on legacy technology solutions and heavy use of spreadsheets. To make decisions on fulfilling demand or optimizing inventory, planners and managers might spend 80 percent of their time rounding up data from multiple sources, and just 20 percent on actual analysis.
It can mean hours of tedious, stressful and unrewarding work. Given the limitations of legacy tools, those decisions may be little more than educated guesses. When something goes wrong, a finger-pointing blame game can ensue. Employee satisfaction suffers, turnover rises and the company faces another costly and time-consuming hiring cycle.
Meanwhile, planners and managers are under growing pressure to improve supply chain performance amid challenges including high customer expectations, faster delivery times and increasing volumes of data. That puts a premium on workforce productivity.
More Time for Strategy and Creativity
A key to building a happy and productive team of supply chain planners and managers is to equip them with modern technology that eliminates repetitive drudgery. That’s one of the benefits that companies realize through cognitive automation.
Powered by AI and machine learning, cognitive automation lets machines take over the difficult work of collecting data from a set of far-flung supply chain applications. Data is cleansed and enriched in a cognitive data layer, and algorithms are applied to assess scenarios and recommend optimal actions.
It’s accomplished at a scale and speed far beyond human capabilities. Data aggregation and analysis that can take human planners weeks and months is done in near-real time. Instead of mind-numbing data chores, teams are liberated to make informed decisions based on AI’s analysis of complete and up-to-date information.
They’re able to better develop “soft skills” that machines lack, in areas such as strategic leadership, critical thinking and problem-solving — three characteristics that the DHL study found to be most valued for the supply chain manager of the future. They’re able to play a more strategic role and better collaborate with partners to drive new cost-efficiencies across the full supply chain.
Cognitive automation has a significant impact on supply chain planners and managers in several key areas:
More creativity and innovation. Planners and managers finally have time to “think outside the box” and devise creative innovations that improve service levels, reduce working capital, optimize demand forecasts and minimize risk.
Unbiased decision-making. Human cognitive biases influenced by age, past experience and “group thinking” undermine the quality of supply chain decisions. Cognitive automation lets decision-makers focus on hard data, and exercise human judgment as necessary.
Productivity on Day 1. Cognitive automation dramatically reduces the learning curve for new hires. It’s no longer necessary to spend months or years mastering arcane workarounds and data manipulation techniques, as machines do the heavy lifting.
Institutional knowledge preserved. AI captures, preserves and exposes not just numbers, but the decision logic elements of who, what, when, where, why and how. That means that established decision-making processes no longer disappear when a valued employee leaves the organization.
Alleviating the Chronic Talent Shortage
Improving the employee experience isn’t a top consideration when a company first explores cognitive automation for the supply chain. They’re typically focused on cost reductions and higher service levels in at least one problematic operational area.
Once cognitive automation is operational, they quickly see the byproduct of greater workforce satisfaction and retention. Employees are more fulfilled, energized and enjoy a better work-life balance. They spend far less time on stressful “firefighting” and more time on work that can make a multimillion dollar impact on their companies.
It’s important to recognize that AI doesn’t replace human intelligence in the supply chain — it augments human intelligence by taking over more menial aspects of cognition (e.g., adding up numbers). That empowers people to focus their time and energy on creativity, innovation and strategic decision-making.
Cognitive automation is here and is a reality. Companies and supply chain teams need to embrace it and prepare and train their workforce and talent for it.