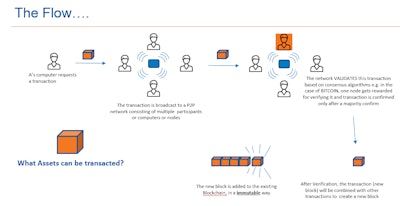
The digital maturity of oil and gas companies tend to vary along the value chain. Upstream oil led the revolution of digitized oil fields and integrated operations across multiple areas even in the most remote parts. In others, such as retail, there are followers looking to enhance their business model using available technologies in other sectors. As an industry strongly focused on health and safety for both employees and the environment, the area of asset management receives the most attention. Blockchain can play a significant role in improving the overall asset management of physical parts within the oil supply chain.
Upstream and refining are asset heavy operations where spare parts need to be of extremely high quality to withstand the harsh operating conditions. Operating temperatures within the equipment can reach 100s of degrees Celsius while the outside environment temperature can be several degrees below freezing. To sustain performance under these harsh and extreme conditions, quality of equipment is critical in achieving high levels of safety.
Blockchain – What and Why?
Blockchain, in simple terms, is an open, distributed ledger that can record transactions between two parties efficiently and in a verifiable and permanent way. The ledger itself can also be programmed to trigger transactions automatically. It does all this without the need for intermediaries and ‘trust’ keepers.
New transactions across any stakeholders in the network are bundled together into data blocks, and each data block is then sent to all the stakeholders for verification. The stakeholders themselves ‘mine’ the transactions and verify its traceability and authenticity. Once finished, the new block of transactions is added to the chain.
By dispensing the need for intermediaries, blockchain creates a new level of transparency within networks and connects stakeholders across boundaries. The core benefits of this technology are security, traceability, provenance, immutability, speed and reliability while breaking down the barriers of intermediation-bringing tremendous value-addition across sectors and industries.
For energy, the benefits will be cross functional – from a decentralized energy transaction and supply chain, efficient, reliable and secure documentation and contract management, guarantees of origin, certification of energy, counterfeits management to efficient trading and supply chain finance, to name a few.
The Spare Parts & Asset Management Use Case
Spare parts management in a traditional refinery and renewables setup is a very complex multi-step, multi-stakeholder process.
A process like this has multiple issues to contend with. A few of these are outlined below:
- Each stakeholder brings its own set of systems and documents to the table, all of which contribute to creating the supply chain journey of a product from before it was created to its actual usage in the installation.
Journey of the products (origin, movement, use of material) across a supply chain remains an unseen dimension for end consumers.
- Each stakeholder system maintains its own system of records and the ledger, which is a proof that the step occurred. However, unless the stakeholder certifies, confirms and transmits the required document physically (read manually), the next stakeholder cannot perform its role in this chain.
Guaranteeing the integrity of certificates is a costly process which, despite laborious audits, are still a challenge to assure the validity of the claims being made.
- Moreover, information flow between various stakeholders is paper intensive and prone to delays.
- There is therefore, no provenance and/or identification of the custodian of the produce in the various stages of the chain.
The issues associated with this traditional process don’t stop at delays and loss of productivity. Fraud and fakes are very expensive to prevent or correct and could lead to severely damaged reputations. While fake parts can be weaned out by an intricate set of checks and balances, eventually things do fall between the cracks leading to huge risks and costs for the parties involved. Fabricated part certificates, insurance documents are on the rise and this technology can really help in preventing these kind of fakes infiltrating the industry.
Blockchain as the solution
The first step in the solution is to build a distributed network with all the relevant stakeholders and having them as individual nodes on the blockchain. The inherent nature of the blockchain technology ensures
a) Complete un-deniability of the individual steps that make up the parts journey,
b) Complete verifiability & visibility to the stakeholders involved in the chain and
c) Security of the stakeholders themselves, e.g. once the manufacturer provides confirmation on the product completion, the transaction is posted on the Blockchain.
Certifiers physically verify the finished parts and the relevant certificates for each finished part in the chain are posted on the same blockchain. This information is then immediately visible to the stakeholders in the chain and becomes part of the lineage and history.
Documents, invoices or shipments created by downstream stakeholders go into the blockchain as well. The primary and secondary supplier can confirm their actions and transactions on the blockchain and this builds up the immutable provenance of the spare part.
At every step of the chain, the relevant stakeholder has an ‘inflight view’, a visibility of where the product is in the chain, and can plan the rest of the transactions with much greater efficiency and security.
Operating safely
It is accepted by industry bodies such as IChemE (Institute of Chemical Engineers) that the majority of incidents happen during transient periods. The quality of equipment to manage these transient conditions is critical especially when start-ups or shut-downs can take days. These transient periods are usually after or prior to maintenance. Industrial plants need to be aware of black list suppliers to avoid using counterfeit parts that can cause safety issues. Although counterfeit is one issue, potential quality issues from genuine suppliers can equally cause severe damage.
Blockchain by tracking all transactions will ensure that the equipment produced can be traced faster to avoid further damage. A blockchain could be used, for example, to track which suppliers produced the components, analyze production history, maintenance and other parameters to highlight any missing steps or failures. This can go as far as the production conditions of the component and even the quality of the ore used to manufacture it.
If used smartly, blockchain can be a real game-changer in the digital age that will surely redefine and reinvent your asset management across the board.