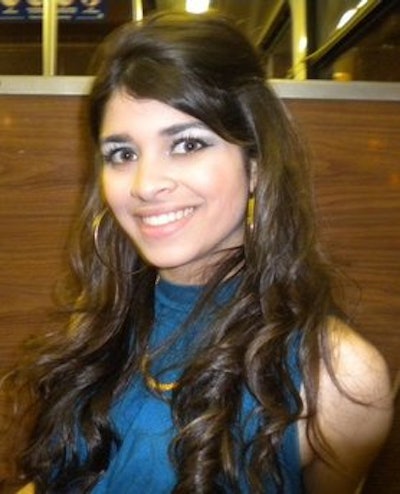
The Internet of Things (IoT) has helped many industries evolve over the years, from retail to manufacturing. IoT based products, also known as connected devices, have sensors that are embedded into a product to track location, condition and predict failure before it’s too late. A recent Gartner study predicted that about 20.8 billion new IoT devices will operate worldwide by 2020. Furthermore, a thirty-fold IoT device increase could significantly reshape supply chain operations.
How IoT Makes Supply Chain Service More Efficient
The supply chain industry has made great use of connected devices. For example, Loaded Delivered stated that food manufacturers use sensors to ensure better quality control, analyze labor costs and monitor worker productivity.
Supply chain involves transporting goods from manufacturing facility to customer, which is complex. Field service and supply chain is even more convoluted, which involves providing maintenance, repair and other support services to end users after sales. IoT is helpful in inventory management to customer service when it comes to service supply chain.
- Sensor embedded machinery reduces downtime. According to MBT Mag, production facilities are embedding sensors into machinery to track product use conditions. IoT sensors monitor factors like temperature, shock and other environmental conditions to predict when and why a product malfunctions, sending an alert back to the central network. From there, an employee can tell a customer exactly why a product is failing and which part. Customers then don’t have to rush for a simple repair or part replacement.
Reacting ahead of time saves the end user money on expensive replacement and repairs. The increased uptime means products don’t require maintenance services on a set schedule. Users save more money when paying for service only as and when it’s needed. Furthermore, photographic instruments and scanners can scan parts to ensure the right materials are at the right place and time, and even send maintenance alerts that require little human intervention.
- Better forecasting reduces spare parts inventory costs. Many companies rely on reduced spare parts inventory to reduce operating costs. Carrying too many or too little spare parts is bad for business, and IoT sensors can help reduce spare parts. Traditionally, companies use historical data based algorithms to calculate spare parts needed, which isn’t always accurate. These days, sensor networks teach companies exactly how components perform, which accurately predicts which components fail and how quickly.
MIT Center for Transportation and Logistics and OnProcess Technology recently developed an inventory planning method that utilizes both historical and IoT based data to predict spare part needs. This method only needs about 1,000 IoT signals to capture enough data. In the end, a company could reduce stock by up to 10 percent. Even just a 6 percent reduction of unnecessary parts can save a company up to millions of dollars, depending on parts costs. Additionally, companies will have just enough parts to deliver to the right customer at the right time, as needed
- Post sale customer demand is better fulfilled. By aligning field service operations with IoT-derived parts maps, companies better predict customer needs. In industries such as technology and electronics, servitization is becoming more common, which means companies are selling services rather than just products. Today’s customers are expecting longer warranties, 24/7 product support, refunds based on defects and other common post sales services.
IoT is particularly helpful in reducing No Trouble Found returns. NTF returns happen when customers falsely believe a product is defective and return for a refund. When OEMs spend time testing products only to find no malfunction, companies can lose billions of dollars. IoT enabled devices better determine if a product is defective before a customer returns it. If sensors rule out malfunction, making the product work requires a much simpler action such as hitting the reset button. Using the central network to also track crash and event logs helps detect other usage patterns and potential problems.
Sensor Driven Data Bypasses Traditional Methods
Before the IoT, companies made educated guesses when managing inventory and providing aftermarket parts and service. Today connected devices prove science is more accurate than instinct in the service supply chain. Now that more customers demand aftermarket services, businesses must understand customer behavior more accurately to stand apart from competition. A connected device is like a product with a brain and a voice that tells companies exactly how consumers use products and when products are in poor health to eliminate the guesswork.