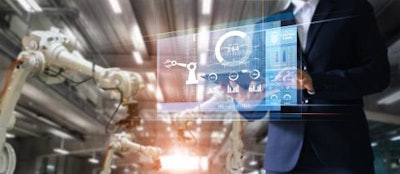
Managing a fluid supply chain comes with many challenges as countless factors are in play during any given process. With customers expecting fast deliveries, supply chain managers need to turn to solutions that will mitigate delays. These delays are often caused by poor processes, machine failures and other missteps in the production process.
Today, combatting these hurdles and fully understanding supply chain challenges within your organization require innovative technology. Digital twins are a solution of the future. This article will explain precisely where digital twins help along the supply chain and highlight prime examples and use cases.
What is Digital Twin Technology?
What if you could understand why a misstep in your production process may occur before it even happens? What if you could generate a visual representation of all your assets and simulate how operations across the supply chain will go? What if you could recognize the most efficient business practices to keep my manufacturing operation running smoothly?
The good news is you can. Digital twin technology is the future of supply chain simulation. It is the next revolutionary piece of technology to help companies make the most out of their analytics tools and data.
In the simplest terms, digital twins are visual representations of physical objects and processes. These objects and methods include everything from simulations of manufacturing plants and factories to large pieces of equipment or parts of different machinery. Equipping teams with this technology gives workers the ability to anticipate and react proactively.
The overall goal is to allow engineers to pinpoint missteps in the production process to optimize design, manufacturing, and labor processes. Visualization of every aspect and asset of production also can give maintenance teams a clear idea of when a particular machine needs to be inspected and, if a failure occurs, exactly how to fix it without halting or delaying operations.
Supplied with data and analytics, digital twins give workers a real-time view of their supply chain assets– allowing them to prepare approaches and see patterns from a tablet or computer prior to getting "physically" involved.
Examples of Digital Twins
For example, a manufacturer testing a product in the virtual world first during the design phase offers more flexibility and is more cost-efficient for testing how two parts work together.
Another prime example relates to machine failures and machine downtime. Failing equipment is a primary culprit to supply chain delays, and ensuring machines stay up and running is a significant benefit to all members of the supply chain– the producers and the consumers.
When a maintenance team can interact with a machine's simulation, many benefits occur. Not only is the maintenance team gaining a comprehensive overview of all the different parts and components, but they can receive proactive insights that lead to fewer reworks and more efficient resolutions to machinery failing. Because the digital twin is filled with real-time data relating to the optimal temperature, pressure, humidity and other levels of the machinery, they can easily interpret setbacks before visiting the physical asset and performing specialized maintenance. Another benefit is seeing the entire plant or factory from the inside out, knowing how certain parts are supposed to fit together, so every task is done quickly and accurately the first time.
How Do Digital Twins Empower Predictive Maintenance?
Any digital solution implemented by a company has a goal. That goal typically involves making more efficient processes to keep workers and customers happy while benefiting your bottom line. Analytical approaches and innovative tools are at the forefront of achieving this overarching goal of better strategies and more success. While we cannot predict the future, we can use tools to help us predict slowdowns in the supply chain.
Predictive maintenance uses data-driven techniques to help determine the conditions of machines and equipment, and digital twins are the key factor in doing so.
To get the most out of digital twins and predictive maintenance, a firm grasp on company-wide data is a prerequisite that cannot be overlooked. The term "data silo" refers to a repository of data that is untouchable by the majority of an organization. Company manuals may exist in one department, sensory data from machines may exist in another, and records of machine levels may be kept in a separate data source. Connecting all of this data for relevant company-wide use is how one gets the most out of their digital twin usage.
Digital twins are so reliable because of the real-time data compiled within them. Without an intelligent solution that utilizes connectors and breaks down data silos, digital twins lose impact, and their purpose within the supply chain fades.
All in all, digital twins can be what your operation needs to continue to run effectively, but data connectivity plays a significant role in empowering them to do their job.