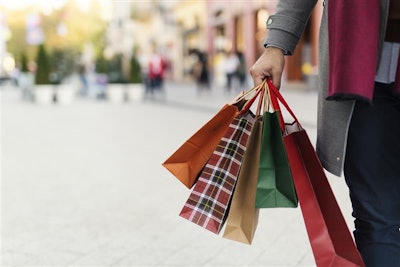
Reverse logistics has become a vital part of the growing e-commerce sector, and the efficient management of returned goods has become a necessity for e-retailers. According to the market estimations, nearly 30% of purchased products on e-commerce platforms are returned. Adopting technology is necessary for market players to manage a huge volume of returns. E-retailers and warehouse owners have partnered with tech companies and startups to reduce waste generated during returns.
However, the Coronavirus disease (COVID-19) pandemic has brought new challenges in managing reverse logistics and market players need to take all the safety precautions and devise strategies to reduce the waste. With adoption of technology and safety measures, the market for reverse logistics would boom in coming years. According to a report published by Allied Market Research, the global reverse logistics market is expected to reach $603.90 billion by 2025. Following are some of the activities taking place in the industry.
Adopting technology to optimize return processes is a recent trend adopted by retailers and organizations. Tech market players have realized the opportunities in the sector and brought their technological solutions.
Partnership with tech startups in order to reduce waste produced in the reverse logistics process is one of the smartest steps taken by organizations.
COVID-19 impact on reverse logistics
With remote working on the table, the burden on IT equipment would increase considerably. Deployment of state-of-the-art infrastructure has become a priority for organizations for continuity of businesses. Not every organization has advanced equipment and many have been scrapping old ones to make a room for updated ones. Equipment manufacturers or reverse logistics companies need to handle the influx of returned or replaced products during the pandemic.
There has been disruption in the reverse logistics chain due to the lockdown across many countries. Many consumers have held back their items, waiting for reopening of chains. This disruption would cause havoc once the supply chain begins as restrictions on lockdown ease off. To efficiently manage the flood of returns, retailers need to deploy the practices and technologies they deploy during the holiday season. Retailers and warehouse owners can deploy data-driven technology that can scan and asses the returned items. Based on the data points, owners can determine what needs to be done with the product. If it shows that items can be refurbished and sold again, it will reduce the waste and enhance profitability. The technology can be useful for those products sold online. Experts have also expressed concerns over the warehouse spaces for storing the returned products. Online retailers have pushed the timeline for anniversary sales from July to August to assess return inventory and take further steps accordingly.
There are concerns over disinfecting and cleaning of those items to prevent infection as it is found that the coronavirus can live on surfaces for hours and days. In warehouses, safety must be made the first priority for workers. Safety guidelines and recommendations by governments should be followed and procedures should be established accordingly. There has been reallocation of workers from stores to warehouses due to handle the workload efficiently. As many workers have been reluctant to return to work, retailers must demonstrate the safety precautions and educate workers on safety practices.