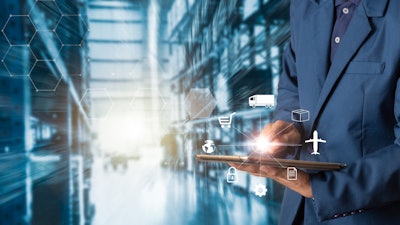
The Coronavirus disease (COVID-19) pandemic has upended the manufacturing industry, forcing job shops to reconsider their current infrastructure and ways of work. Specifically, the pandemic has highlighted the need to do away with legacy analog systems. Today’s customers expect digitized systems, and if a shop can’t deliver, they risk losing business, which very few can afford in the current climate.
Being digital is no longer optional for today’s job shops. Even beyond the current pandemic—in which most business is conducted virtually—customers have come to expect an experience featuring one-click purchases and same-day shipping. Internally, industry 4.0 has also put an emphasis on digital and connected information. Rather than allowing data to live in different silos, it should be gathered through connected systems to form a knowledge base from which job shops can make better decisions.
There is significant downward pressure—internal and external—on even the smallest job shops to adopt Industry 4.0 technologies, a demand which has been heightened by COVID-19. As more job shops move toward digital transformation, here are a few key factors to consider.
Automating one process can impact the entire organization
The mutual goal of Industry 4.0 and digital transformation is to achieve a higher level of efficiency and to implement better practices that reduce bottlenecks, increase production speed and trim costs. Automating even one internal process, such as quoting, can make major progress toward that goal. For instance, by automating quoting, job shops can greatly reduce the need for data entry, freeing up their most experienced employees for more strategic work. It also improves the consistency of quotes, so rather than being tens of dollars off, quotes can always be within nickels or dimes of the true cost. Most important, streamlined quoting supports just-in-time manufacturing and expedites the customer experience. In many cases, job shops can deliver quotes to customers within a matter of hours. The faster a job shop can provide quotes, the faster it can process jobs, allowing them to take on more business overall.
Choosing the right solution can make or break digital transformation
Knowing which digital solution is right for any given business is difficult, and investing in the wrong one can be costly. When exploring options, job shops should ask themselves these two questions:
· What are my needs for digital transformation? Does this solution help me get there? There are numerous industry-specific products being marketed to manufacturers, but they may provide an umbrella of capabilities that job shops don’t actually need. Make sure to invest in solutions that streamline current processes, not make them more complicated.
· Which solution will benefit the entire organization? A job shop should not invest in multiple solutions in order to address a multitude of problems. For instance, a quoting solution should not just improve one process—it should also factor in related processes, such as built-in communications capabilities that eliminate the time wasted searching for engineers on the warehouse floor. It’s also important for job shops to first understand the root of the problem they are experiencing. If scheduling issues are being caused by inaccurate quoting or slow order processing, for example, that is the area where they need to invest.
Prioritizing security is mandatory for Industry 4.0
Many job shops assume they wouldn’t be a target for cyber criminals, but in reality, hackers are more likely to steal sensitive data if they believe the shops are less protected than the internal networks of large manufacturers. Job shops must also keep cybersecurity top of mind to protect their customers’ sensitive information. Yet, most shops are behind with their cybersecurity infrastructure—still using on-premises systems, outdated versions of Microsoft Windows and Excel and large file servers. In many cases, everyone on the network can access any file via a shared drive. Oftentimes, cybercriminals will hack into and use the shops’ network to deploy phishing emails, through which they can exploit a weakness on the server and execute attacks throughout unprotected systems. If a job shop employee falls prey to this type of breach, and malware spreads through the shop’s email contacts to reach its customers, their information could be compromised within the hour. Not only could job shops betray sensitive information, but they will also lose customer trust, reputation and, ultimately, business. It is critical to deploy solutions that protect information and support cybersecurity, so customers can trust them as a true partner.
There is abundant conversation about what job shops must do to prepare for the future—but with unplanned, unprecedented challenges such as COVID-19, that timeline has been accelerated. Digital transformation can seem like a hurdle for shops, but with the right Industry 4.0 technologies and digital solutions, they will be equipped to respond to the opportunities and challenges to come.