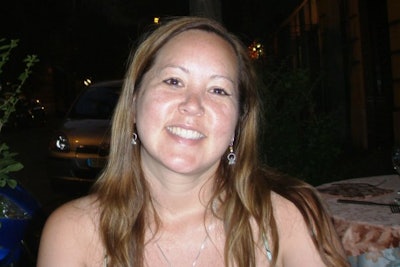
We are truly living in a fascinating time where things once only dreamed about in science fiction are becoming reality: driverless cars, appliances that text you when they need servicing, home security technology that allows you to track your children’s movements from your smartphone, and home healthcare wearable technology that can alert you if your elderly loved one falls.
These are just a few of the hundreds of ways consumers are taking advantage of this new technology landscape brought to you by the Internet of Things (IoT), which enables the automated transmission of information over a network without need for human intervention. Just as the consumer world is changing at light speed with the adoption of IoT technology, the manufacturing world also is in the midst of an IoT revolution. IoT is enabling manufacturers to gain competitive advantage and lay a foundation for the factory of the future with smart connected operations, smart connected assets and the smart connected enterprise. These initiatives to modernize manufacturing plants and facilities will have a huge impact on workers and organizations.
Leading global manufacturers across various industry verticals are putting together strategies that leverage IoT technology to modernize their processes and organizations. Analyst firm LNS Research sees four main areas for manufacturers to consider when developing their IoT strategy: connectivity, cloud, big data analytics and application development. Let’s take a look at each of those areas individually and how they all work together to create a factory of the future.
Connectivity: To act on the data, you need to collect the data
On the factory floor, it already is impressive how sensors, instruments, cameras, RFID readers and other data collection devices are being deployed en masse to record and track a wide range of operational processes from tracking temperatures to inspecting parts with greater speed and accuracy to equipment productivity. The installed base for Internet connected devices already exceeded 14 billion by early 2015, and is forecast to balloon to nearly 50 billion by 2020 according to one estimate from Cisco.
Adoption of connected devices on the manufacturing floor is expected to continue to accelerate for a number of reasons, including lower costs for smart devices, reduced connectivity costs as providers are starting to charge less for data connections, more efficient wireless communications, better reliability and security, and expanded cellular networks, leading to higher bandwidth. In addition, now there is easy to use software available that can take all that collected data, and provide insightful and actionable analytics on a regular basis.
How is this connectivity being applied to a factory of the future? Imagine installing sensors and controllers to your major pieces of manufacturing equipment and throughout your manufacturing facility. These sensors can inform you of a piece of equipment’s need for maintenance before something malfunctions, preventing expensive production delays and shutdowns. Questionable parts can be viewed remotely with cameras or optical sensors, and then followed digitally through its production run and throughout the supply chain. All the while, sensors continue to collect data on the performance of those parts and the equipment used during production runs. Building out the infrastructure to create this smart connected enterprise will be critical for manufacturers if they hope to keep up with their competition. By 2025, the number of connected devices used in manufacturing facilities or for manufacturing processes is expected to represent 75 percent of all connected devices, says information and analytics firm IHS.
To gain any true business value out of all this data being generated with connected devices on the manufacturing floor, you need a scalable infrastructure that lets you store, organize, integrate and secure that data. There is no better time to get into the game than now. The advent of cloud computing has greatly reduced computer processing and storage costs, so economic barriers to entry are becoming almost non-existent.
Organizations that haven’t fully thought through how to leverage the large and complex amount of data being collected will not be positioned to fully take advantage of what the Internet of Things can do, as all components of an IoT solution must work together and be secure at every point throughout the system. Streamlining and connecting this new wave of device data to back-end cloud applications and services is critical to driving production and infrastructure costs down and profits up. Companies that wisely adopt a cloud strategy are getting greater bandwidth and scalability, and are able to save time and streamline operations.
And of course, being confident that your data is highly protected and secure throughout its journey from device to data center to the cloud is extremely important to the factory of the future. As manufacturers begin to rely more and more on cloud technology, they also will have to consider how to protect themselves against cyber threats to their intellectual property. Factories of the future must have reliable security measures to protect against hacking and to ensure that confidential data cannot be breached.
Big Data and Analytics: Analyzing the data and gaining actionable insights
To get the most out of the massive amounts of data that is generated (also known as Manufacturing Big Data), manufacturers must be able to analyze it and act on it quickly—often not such an easy task given the sheer amount of data. Many manufacturers are unable to manage and analyze such large volumes of data spread across multiple systems due to the lack of a robust and scalable infrastructure, technologies, and analytical tools. These issues are often magnified if companies experience slow access to the data that is critical to their businesses. The end result could be delays of several days to weeks to analyze the root cause of defects, and often prevents timely corrective actions.
Factories of the future will adopt end-to-end solutions that help consolidate, contextualize and analyze massive amounts of product, process and quality data generated by manufacturing facilities. These solutions will enable these enterprises to detect problems earlier in the process to help maximize yield, improve quality, and minimize defects and cycle times. The implementation of an effective Big Data strategy often can yield a 10-25 percent reduction in operating costs, 10-50 percent reduction in assembly costs and can generate an increase of up to 7 percent in revenue. The factory of the future will be able to deliver this Big Data analysis on a smartphone, a tablet or on a desktop on the shop floor, act on the data, then push information back to the field, the production line or out to a supplier. Easy access to such level of analysis that these analytic tools enable can help facilitate decision-making, improve products, solutions and customer service, and can help uncover other new opportunities for improvement.
Applications Development: Streamline the data into intuitive business flows with modern cloud applications
In light of this new manufacturing revolution, many manufacturers now are taking a harder look at their current enterprise applications, business processes and data, and realizing the inefficiencies in utilizing systems that are functionally isolated and fragmented. Bringing all these processes and data together in smart business flows is the next component to a strong IoT manufacturing strategy. The right cloud applications can help revitalize and optimize older business flows and processes on the factory floor.
Some manufacturers might be interested in an integrated cloud planning and manufacturing solution that enables manufacturers to plan and balance supply and demand in one screen while efficiently managing the shop floor. Or some manufacturers might benefit from complete order to cash solution that will allow them visibility to orders as they are fulfilled. The possibilities are endless, and the bottom line for factories of the future is less risk and lower costs for cloud applications deployed as part of an overall IoT strategy.
We already are feeling the effect of the Internet of Things in our daily life. IoT represents not just new technology, but a new way of viewing technology and its uses. For manufacturers to have a comprehensive IoT strategy they will need to consider all four main areas discussed above. Leading manufacturers already are way ahead of the game and have recognized and built their IoT strategy to include these four areas because they understand the impact of IoT, and are well on their way to building their factory of the future.