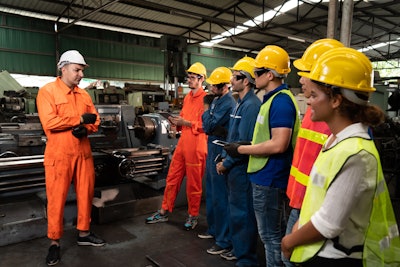
You might think the most pressing worker safety challenges in manufacturing involve big things like machinery or forklifts. But honestly, it's often the simple stuff that needs the most attention. Slips, trips and falls continue to be some of our biggest safety concerns.
And it's not just in the factory—it's everywhere. We’re moving faster, we’re distracted and we sometimes forget about the basics: slippery floors, texting while walking, or standing on an unsecured ladder. We really need to go back to the fundamentals to make a difference.
Start with a Safety Mindset
The key to mitigating those risks is to be proactive. Simple actions like doing regular safety observations, inspecting facilities, reporting near-misses and taking corrective actions can help prevent accidents before they happen. It's all about catching issues early and addressing them head-on.
Key practices to keep safety front and center include:
- Offering comprehensive safety training
- Employee incentive programs around safety training
- Tracking key safety performance indicators, like safety observations, by location
- Incorporating daily ergonomics stretching to help prevent repetitive strain injuries and other health issues
Adopting practices like these helps to create a culture where safety is always top of mind. And when you make safety a top priority, people really notice. Not only do they become more mindful of their own actions, but they start looking out for each other.
A strong safety culture shows employees that we care about their well-being. At the end of the day, we want people to leave the workplace in the same condition they arrived—safety always comes first. When safety’s a top priority, it boosts morale, reduces injuries and leads to better long-term productivity, improving overall operational efficiency and employee well-being.
Make it the Priority at all Levels
Clear, consistent communication is the key. Talk about it first at your daily huddle on the manufacturing floor. And it’s not a one-way conversation. You need to make sure your team members feel confident relaying their safety concerns to their leadership. One way to accomplish that is with local team safety committees, made up of a variety of team members, not just managers.
This creates a heightened awareness of safety at all levels, showing everyone that it's an integral part of the company’s culture. When safety is a constant topic, it becomes second nature to look out for one another—and everyone understands that keeping each other safe is just as important as getting the job done.
Technology Can Offer a Valuable Assist
For today’s manufacturing and supply chain environment, technology plays a huge part in enhancing worker safety and ensuring compliance with safety regulations.
It is equally important to operate an aggressive near-miss program, so the root causes of potential problems can be uncovered before they turn into accidents. Think about your own home…how many times have you tripped over that uneven board on the deck, or slipped on the tile in the bathroom? Yet too often we don’t take the corrective steps needed until after the accident. The same holds true in the workplace. Whether it is at a warehouse, in an office or on the factory floor, we all experience near-miss situations with regularity. Solving those issues early can help you attain the safe environment you seek.
Special Challenges Shouldn’t Mean Shortfalls
Depending on your business, you could have special or unique situations in your work environment that make safety a greater challenge. But that doesn’t change the expectation or the responsibility you need to make to your team to keep them safe.
In manufacturing and distribution right now, for example, staffing is a huge challenge to the environment. Across our industries, the turnover rate has us operating with team members who may come to us with inadequate training, underdeveloped skillsets, and a lack of knowledge of our guidelines and procedures. Oftentimes, we are bolstering our regular teams with temporary staff, who may not be in our facilities long enough to embrace the benefits of our training and development. It is estimated it takes 8 temporary employees a year to cover a single open position!
We need to be cognizant of the positions to which we assign these new or temporary workers, making sure to educate them on the basics of our safety protocols, and provide heavier supervision, while we steer them clear of any areas that are more complex, or might pose a greater risk.
Safety is the Best Investment You Can Make
Making safety the priority is smart business. As you think about the costs of a comprehensive safety plan, consider that it is likely 2-3 times LESS than what you’d spend without a robust safety environment – on injuries, down time and turnover.
In the big picture, we’re all looking for zero-injury world. That’s the goal. Because when you remove the hazards, you can focus on quality, delivery and innovation, building your business with productivity and confidence.