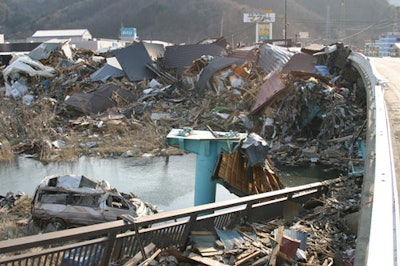
Tokyo—April 1, 2016—Five years after a huge earthquake temporarily crippled parts of Japan's auto supply chain, some companies have adjusted the industry's famed just-in-time production philosophy in a bid to limit any repeat of the costly global disruption.
The quake exposed the vulnerability of a system pioneered after World War II by Toyota Motor Corp. under which companies aim to boost efficiency by receiving small quantities of parts from suppliers only when needed.
But even with the risk of new disasters in one of the world's most seismically active countries, businesses have had to balance efforts to disaster-proof the supply chain due to concerns of the cost of, say, storing more inventory in case of an emergency that may or may not strike.
"Holding more inventory or adding another production line as a business contingency measure may improve a company's robustness in the face of disaster, but it won't necessarily improve its global competitiveness," said supply chain expert Takahiro Fujimoto.
To read the full story, please click here.