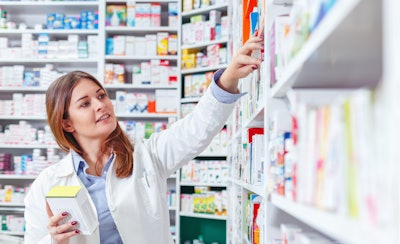
When it comes to supply chain stability, patients’ fears extend far beyond medication availability and affordability.
Many who participated in Zebra’s latest Pharmaceutical Vision Study say they are concerned about “the reduced quality and efficacy of medications and treatments due to improper refrigeration or temperature control.” They are nearly as worried that more illness and/or death will occur due to contaminated or tainted medications. They don’t believe pharmaceutical supply chain entities will be able to identify and remove suspect, illegitimate, fake or counterfeit drugs from distribution channels if supply chain improvements aren’t made. One-quarter of patients also cited a slow recall of defective drugs, the inability to track medication back to its source, and the inability of entities to adhere to and monitor compliance to regulations as potential risks.
They had other concerns, too. But, like the ones just mentioned, nearly all were centered on their health, safety and well-being. Will they be able to access and afford medications that they can trust will help – or at least, not harm – them?
I bring this to your attention because most of these concerns aren’t equally shared by supply chain decision-makers. There is agreement about the need to better maintain the cold chain and the consequences of temperature deviations during storage and transportation. But the second biggest “risk” cited by decision-makers was brand reputation.
I understand. As manufacturers, distributors and warehouse operators, you shoulder a lot of responsibility in the delivery of life-improving and lifesaving pharmaceuticals. If someone loses trust in your capabilities because the quality or integrity of your operations and products are somehow compromised – or simply perceived to be so –millions of patients around the world will be affected. The people you employ and partner with, those who rely on your paychecks, will also be impacted. So, reputation matters.
Yet, the method by which you should build and protect that reputation is changing – at least that’s what I gather from patients’ feedback in this study. Focus more on maintaining control and information flow than managing optics.
Current supply chain responsibilities
Before the pandemic, compliance was probably the timeliest problem and biggest priority for many. And though it’s still difficult according to one-third of surveyed decision-makers, “preventing, detecting, and responding to risks and threats posed by substandard, falsified, and counterfeit medicine” is the top challenge today. Over the next five years, organizations will also have to work hard to keep pace with the adoption of technological innovation and improve operational resilience. Maybe that’s why “transparency” was a common theme in decision-makers’ hopes and priorities.
Almost all enterprises say visibility across the supply chain provides a competitive advantage. And they acknowledge that if more patients had digital access to information about medications and supply chain histories, they could easily learn about the source and journey of their treatments, helping build trust in the integrity of the supply chain and their medications. Patients tend to agree.
As such, many decision-makers believe the top priority right now must be to invest in more or better technologies to track medications from their origin at the manufacturing plant to patients. They also want the industry to place a stronger focus on keeping the supply chain secure from suspect, illegitimate, falsified, or counterfeit drugs, and they want to see changes that ensure the availability of medications and treatments for patients.
From my perspective, these things all go hand in hand. If you can track and trace medications from the first mile through the last – and you can see when, where and how someone handles a pill, package, or pallet – then it becomes easier to maintain accountability, quality, control, availability and trust end to end. However, barcode scanning alone won’t provide this level of operational visibility or information transparency. There are too many environmental, safety and security factors that influence the performance of pharmaceutical supply chains, and many of them can’t be monitored or managed via barcodes.
Technology increases transparency and trust
To really get a sense of what’s happening, or not happening, during production, distribution, storage, and administration, you must be able to “sense” product temperatures and movements. You must also be able to clearly see variations in raw materials, products and packages that typically go unnoticed by the naked eye. That’s not something a barcode scan is going to reveal. An invalid barcode might alert you to a label or packaging swap at some point in transit. But when you have hundreds of vials or bottles on a pallet, are you really going to scan each item to confirm that none have been removed, replaced and/or tampered with?
There’s a reason why location technology has already been deployed by nearly half of surveyed pharmaceutical decision-makers and over a third say they’re using radio frequency identification (RFID) today. It’s the same reason why 97% of decision-makers say they plan to use location technology within the next five years. Many believe location technologies are the best way to trace pharmaceuticals, and track and trace capabilities are key to moderating drug safety risks and maintaining supply chain stability.
However, like most things in life, teamwork makes the dream work.
RFID is great for counting and tracking inventory, but location technologies alone can’t stop all threats to the supply chain, allay all patient concerns or inform all operational decisions. Machine vision systems are needed along production lines to help authenticate the presence and accuracy of direct product marks on tiny pills, confirm proper vial fill levels, and verify correct label information and placement. And temperature sensors must be strategically used in facilities, containers and trailers along with batch-item monitors and barcode-based data capture solutions to help report on the state of products – and the supply chain.
Data collected from digital sources can be stored in the cloud and mined using artificial intelligence and machine learning technology. When unusual patterns or red flag anomalies are identified, stakeholders can be prescriptively alerted and guided through the proper intervention. Offline technology and data, like that collected during visual check of a temperature sensitive label, can be used as a “trust but verify” tool by pharmacists, physicians, and even patients. They can confirm the cold chain was maintained prior to administering medications.
Click here to hear more about technology and data in the supply chain:
The way forward: trust in technology
Almost half of patients and pharmaceutical decision makers agree that technology can optimize the supply chain. Four-in-10 also believe technology can help companies and institutions maintain drug quality, efficacy, and stability. And while I’m glad to see many decision-makers believe that technology-led transparency drives supply chain resiliency, all decision-makers need to buy in.
With the Drug Supply Chain Security Act taking effect next year, patients lacking trust in pharmaceutical supply chains, and overall supply chain issues rising, now is not the time to stick with the status quo. Move beyond the barcode. Explore different approaches to track and trace. Research how temperature-sensitive labels compare to temperature sensors and batch monitors. Ask experts how you can quickly fill information and capabilities gaps.
Build a “team” of technologies that can collectively increase your operational visibility and give all stakeholders transparency into the pharmaceutical supply chain. That will be the only way to build universal trust and protect your brand reputation.
Download the full Pharmaceutical Vision Study report here.