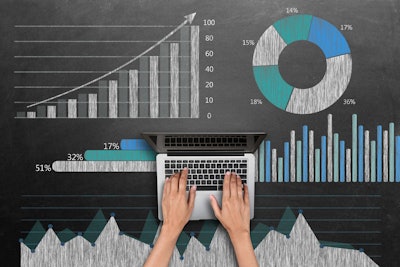
“Until the consumer buys, nobody sold.”
That is the mantra of the supply chain—no one makes a single dollar until the end customer purchases a product from the store shelf. If this is true, shouldn’t manufacturers base demand planning and replenishment on actual consumer consumption? After all, they cannot profit from inventory that sits in back rooms, incurring costs and slowing down the entire value chain.
Unfortunately, this is often the case, as many companies still operate under a push-based rather than a pull-based supply chain model. Why? The problem lies in the fact that, when organizations created their business rules many years ago, those rules were constrained by the lack of available technology and demand data. Now, as new technology and data streams are emerging, the constraints are removed. However, the old business rules, or orthodoxies, remain. To illustrate the situation, here is a simple example: In the past, hotel reservations were made with paper and pencil. Operating under this technology constraint, hotels required patrons to check in and out at a specific time. Although the technology constraint was since removed and reservations are now made through computer systems, the rules (check-in/out times) remain the same, despite whether they work to the patrons’ advantage.
In the world of supply chain management (SCM), manufacturers, distributors and retailers long operated as separate entities, each relying on their own enterprise resource planning (ERP) systems, their own set of metrics and their own key performance indicators (KPIs) to achieve their respective business goals. Essentially, each learned to define their space and make it their own local optimum.
Yet, a local optimum can have adverse effects outside its boundaries, as it creates silos throughout the supply chain. Operating with disparate information, manufacturers are unaware of what is happening with their products on the store shelves. Therefore, to prevent out-of-stocks and ensure product availability at the point of sale, manufacturers overcompensate by pushing out more product than is needed. This leads to higher inventories at the distribution and retail levels, creating bottlenecks and tying up cash. It then becomes up to the retailer to manage the inventory shift, which may ignore what the consumer actually wants. Indeed, the global optimum is not the sum of many local optima.
Today, the data and technology is available to help manufacturers, and their suppliers, retailers and distributors, break down data silos and change their way of thinking. With sophisticated SCM solutions, businesses can create pull-based systems in which replenishment is based on actual demand and consumption. Using the power of cloud-based technology, these SCM solutions allow all parties to access and use the same information, and the same metrics to plan. For example, a global beverage manufacturer can connect with its retail distributors and obtain visibility into store shelves. Based on which products are selling, the manufacturer can produce goods and replenish them accordingly, without worrying about out-of-stocks or surplus inventories. Moreover, the manufacturer can drill down through this information to identify trends across sales territories and even individual stores to proactively prevent future losses.
In addition, integrated and aligned metrics allow users to measure the performance and guarantee the effectiveness of each entity (the local optimum). At the same time, SCM solutions allow users to measure the performance of all companies within a supply chain as a whole, helping to confirm the success of the global optimum. So, going back to the previous example, the manufacturer and its retailers can use a cloud-based system to gauge their individual effectiveness, as well as to look at the big picture to ensure they are generating positive results for the entire supply chain.
Using an end-to-end SCM solution in the cloud, manufacturers, distributors and retailers can break orthodoxies, change their business rules and drive true supply chain collaboration. As everyone works with consistent data and KPIs, they can more easily operate under a demand-driven, pull-based model. This visibility provides sell-out information to all links in the supply chain.
With replenishment now based on actual consumption, the benefits will begin to roll in. Companies can reduce out-of-stocks at the store level, while decreasing excess inventory and overstocks. Manufacturers will replenish only the products that are actually selling, thereby minimizing cash flow deficits and lost sales. The end results are increased sales, improved customer service, a more synchronized supply chain and greater profitability for everyone involved.