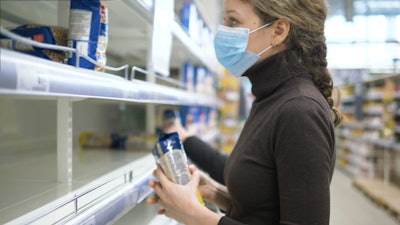
Supply chains have always faced situations that could disrupt information, financial and material flow. Even before the internet or advancements in technologies and globalization, organizations had to figure out how to manage disruptive events ranging from natural disasters, to labor disputes, to war. Of course, this became even more important after these innovations were introduced to the market and as supply chains became global and more complex. Ultimately, these innovations helped define a new frontier of supply chain risk management. Fast forward to 2020, and organizations find themselves facing yet another push to the boundary, and this time it is due to the Coronavirus disease (COVID-19) pandemic.
Organizations now need to understand how to navigate this new frontier in their quest for supply chain recovery and resilience. A critical part of this understanding must include what has been learned about disruption due to COVID-19, and this can be broken down into 3 lesson types -- general supply chain lessons, paradox lessons and knowledge lessons.
No. 1: General supply chain lessons
In many disruptive events, supply chains generally suffer from lack of supply. COVID-19 has taught us that both supply and demand can be negatively and significantly impacted at the same time. Take personal protective equipment (PPE), for example. While PPE manufacturers could not get raw material fast enough to satisfy demand, these same companies also struggled with understanding what real demand looked like. Given that demand for PPE was projected to increase somewhere between 1,700% and 10,000%, it was difficult for PPE suppliers to even assess the degree to which their demand was derived. In fact, some even received purchase orders from buyers where the specified order quantity was simply “as much as you can give me.”
Managing risk itself can simultaneously lessen one challenge while increasing another. This has always been true but has never been more obvious than now. During the early parts of COVID-19, customers began panic buying various products such as toilet tissue. To reduce supply risk, tissue manufacturers looked to increase capacity and volume to meet demand. However, increasing it too much would lead to higher demand risk and very high inventory levels. Yet, higher inventory levels can increase inventory risk while lowering disruption risk.
There are many other examples like those previously mentioned, and a large majority of them share a major characteristic – they are all paradoxes. Of importance during this time is identifying which supply chain paradoxes are key for companies to explore and invest in managing, and these include impact-probability, supply chain strategy and supply base management.
No. 2: Paradox lessons
Paradox lessons highlight challenges in managing tension and the importance of building different types of capabilities across a supply chain for better preparation, recovery and resilience on any given day.
Impact-probability paradox. One of the toughest decisions facing supply chain executives moving forward is balancing investments between low severity-highly probable events and the black swan events that are high severity-low probability events, like COVID-19. Currently, investments made in the former heavily outweigh those made in the latter. Why? Because most risk events like hurricanes and material delays share one important characteristic – a similarity with past events. With this similarity comes historical demand and supply data, previous response and recovery actions of the focal firm and its supply chain partners, tried and true risk management protocols, and reliable disruption playbooks. With the use of technology, companies could exploit this past data and knowledge and deal with disruptions quickly. With COVID-19, there is no past data, therefore heightening the danger of failing to balance the investments.
Supply chain strategy paradox. In order for organizations to prepare for future waves of COVID-19, it is essential for supply chain leaders to consider a dual-focused supply chain strategy approach where efficiency and responsiveness are optimally balanced. Given the pandemic, organizations such as UPS and the World Economic Forum are now recognizing the need for such an approach. Efficient strategies are for mass-produced essential products and can enable organizations to focus on minimizing stockout frequency while optimizing the physical cost associated with material flow and storage. These supply chains operate best when supply and demand are both stable. Once COVID-19 hit and both demand and supply became unstable, efficient supply chain strategies were ineffective. For such a situation, efficiency needs to be appropriately balanced with agility. An agile strategy can help the company optimize market balancing costs while also building in risk hedging practices. This type of strategy is meant to help balance supply and demand in times when they are both unstable. Balancing an efficient and agile strategy can help organizations meet demand during a disruption.
Supply base management paradox. A third paradox lesson deals with sourcing. At the heart of the supply base management paradox, we see disruption protection being traded for reduced transaction costs between buyers and suppliers. On the left hand is supply base reduction, which results in minimizing the number of suppliers, thereby consolidating large purchase volumes, reducing negotiation costs, material prices and delivery fees. On the right hand is sourcing flexibility, which results in more direct suppliers and geographic redundancies, but also increased cost associated with the need for more coordination and collaboration across the supply chain. Without striking a balance, supply chains are much more likely to be built too much for reduction and not enough for resilience. This problem becomes worse further upstream, to the point that the industry-level supply can depend on a single large supplier or a few suppliers concentrated in a single geographic region. For example, many masks are almost exclusively produced in China, which means the control in generating new capacity during COVID-19 is also with these suppliers and not with the internal key decision-makers of their downstream partners. Again, a balance between supplier reduction and flexibility in sourcing is critical to ensuring efficient disruption protection.
No. 3: Knowledge lessons
This pandemic has challenged and disrupted traditional supply chain practices in a way that very few, if any, could have predicted. To prepare for potential future waves of COVID-19 or the occurrence of another disruptive event, refining supply chain knowledge will be key. In fact, social distancing and other challenges brought about by COVID-19 should serve as encouragement for supply chain professionals to refine their knowledge through virtual supply chain education. COVID-19 has placed significant value on knowledge related to supply chain disruption and risk management. Since the pandemic, there have been several virtual education opportunities, including webinars, conferences and free online courses.