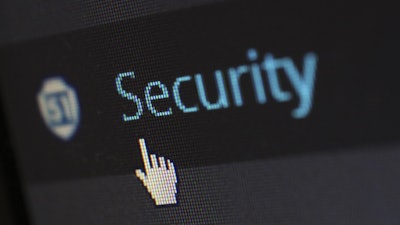
The coronavirus continues to hammer global markets, spreading to Europe, Asia and now the United States.
And, supply chains, large and small, are being dramatically disrupted—from toys and Teslas to stranded lobsters and missing wedding dresses. The damaging economic impact is a stunning reminder of the reality of doing business in a global marketplace.
Of course, if you’re a buyer or procurement manager, this issue gets added to the already existing supply chain disruptions you navigate every day: trade wars, on-again/off-again tariffs, increased government regulations, freight issues, poor or unacceptable part or product quality, and more.
There’s also the ongoing challenge of unforeseen downtime. A study by Information Technology Intelligence Consulting reported that a single hour of downtime can equate to $100,000 in losses in a manufacturing environment. And, that number is likely higher, potentially exceeding $300,000.
Given all of these issues—and, yes, especially given the urgency of the coronavirus situation today—this may be a good time to look at a supply chain risk contingency plan, or pivot to maybe even instituting a major overhaul and reboot.
Supply chain emergency/contingency planning
As Yossi Sheffi, director of MIT’s Center for Transportation and Logistics, wrote in a Wall Street Journal article on this topic, “hoping for the best while preparing for the worst may not seem like a rigorous business approach to the [coronavirus] crisis. But, given our lack of knowledge, it is the most prudent strategy for managing risk.”
Sheffi urges companies to act quickly to minimize short- and long-term impact on their operations. Among a long list of items, he recommends:
- Setting up a central emergency management center.
- Planning for operating to maximize cash flow rather than profits in the short term.
- Reviewing your company’s product portfolio and customer base in order to set priorities.
- Reviewing your suppliers to figure out who makes critical parts and are there alternate sources.
Beyond this short-term contingency mode, if you are considering a supply chain pivot or reboot, here are some brief points on how digital manufacturing suppliers that are closer to your home base can tame supply chain disruption with rapid manufacturing, regional sourcing, on-demand production and customization.
Reliable, fast lead times aid supply chains
Acting quickly can help minimize disruptions. Accordingly, turning to a digital manufacturer that can pair manufacturing scale with reliable, fast lead times enables companies to quickly adapt to market demands and unforeseen forces in your supply chain. Indeed, under a fully digitized process, accurate price quotes can be provided in hours, if not instantly, and the manufacturing can be completed often in a matter of days, sometimes even the same day. This speed can make a difference especially when you factor in the total cost of ownership all along the supply chain, from concept to distribution. For example, if your product is sitting on a container ship for three months, that’s all a part of your total cost.
Regional suppliers mitigate risk
Using regional suppliers can be an effective way for companies to not be as blocked by global disruptions. And, especially if those regional suppliers also use regional suppliers.
Many companies have been discovering the benefits of onshoring options, taking advantage of contract manufacturers that use digital technologies on our own shores and insulating their companies from the macro-economic unpredictability I’ve mentioned.
Indeed, we’re seeing an increasing number of our customers turning to localized and on-demand manufacturing alternatives to off-shoring. Manufacturing locally, or closer to the point of consumption, has been made more economically feasible with the proliferation of digital manufacturing.
On-demand production can tame demand volatility
On-demand manufacturing can help your company tame demand volatility, gain greater control of inventory cost and deliver the right products at the right time at the right total cost. Manufacturing on demand helps companies navigate market volatility, so that they’re not tied to massive production forecasts. When demand spikes, you can get parts quickly. On-demand sourcing can also lower overall inventory costs and warehousing expenses because you’re no longer focusing on mass producing products with high minimum order quantities (MOQs). Instead, you’re opting for on-demand production in low volumes, thereby creating a supply chain that is truly driven by customer demand, not by (and dependent on) a supplier’s lead time.
Mass customization supports supply chains
Finally, yet another way to tame supply chain disruption is to deploy a mass customization approach. Today’s market demands are more customized. This low-volume and high-mix ratio of products is not the supply chain of the past where mass production was the normal way of doing business. Indeed, customization is changing how manufacturing needs to react and on-demand manufacturing has the digital capacity and rapid capability to meet those mass customization needs.
In summary, what’s happening in China and now elsewhere as the virus spreads stands as yet another example of the global uncertainty that we as buyers and procurement managers face every day. And, beyond the business and market considerations, what’s happening is of concern to all of us as caring world citizens.