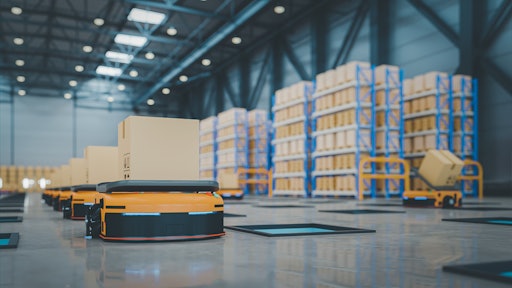
As the e-commerce and supply chain landscape rapidly evolves, autonomous mobile robots (AMRs) have emerged as a powerful tool to revolutionize warehouse operations. In short, AMRs are designed to make the jobs of warehouse workers easier and more efficient.
Among other benefits, AMRs can efficiently transport goods, optimize inventory management and perform repetitive tasks, freeing up human workers to focus on more strategic responsibilities that drive value. Ideally, AMRs navigate through the warehouse seamlessly, avoiding obstacles and optimizing routes. This streamlined approach reduces operational bottlenecks, ultimately revving up productivity and reducing lead times.
Fantastic, right? And yet, not everyone is thrilled about AMRs. Hesitance among human workers is common, especially when first collaborating with AMRs. The robots may be perceived as a displacement threat and/or a disruption to the way workers are accustomed to doing their jobs.
Despite this hesitance, the trend toward embracing AMRs in warehouse settings isn’t going anywhere. Recent surveys indicate that the majority of businesses are planning to increase automation up to 30% in the next year. Another quarter will aim for an increase of 11-20%.
Fostering Collaboration Between AMRs and Human Workers
The successful integration of AMRs hinges on establishing harmony between humans and machines.
When ramping up AMR adoption, it’s critical for leaders to be transparent and communicative. Workers need to know that AMRs aren’t intended to take away jobs, but rather to complement and enhance worker capabilities. In other words, make workers’ jobs easier.
A Balancing Act: Alleviating the Burden on Human Workers While Providing AMR Oversight
AMRs can tackle repetitive and physically demanding tasks that would otherwise consume valuable time and effort of human workers. This can lead to fewer injuries and other safety hazards, as well as lower rates of fatigue, burnout and turnover. Additionally, workers can be empowered through wearable devices that allow them to delegate tasks directly to AMRs – helping to alleviate the burden of repetitive tasks and make their job more satisfying. And it’s worth noting that AMRs can (theoretically) work around the clock — no lunch breaks needed.
Given the labor shortage combined with unrelenting demand, leaders are scrambling to increase job satisfaction, retention and motivation among workers, enhancing overall productivity and efficiency within the warehouse. AMRs may be the answer.
With AMRs handling routine tasks, businesses can likely expect to experience significant cost savings in the long run. These savings can be reinvested in further technological advancements, AMR training programs and employee development programs.
That said, AMRs aren’t perfect, yet. The technology continues to evolve and can experience glitches from time to time. Human workers can support AMRs and ensure full productivity is achieved by providing oversight. While this can be viewed as a burden to some, it is a way of investing time in the beginning for greater results in the future. We are a long way off from ubiquitous “dark warehouses,” which would be fully automated and require no active human labor or supervision.
Strategies for Successful AMR Integration
When it comes to AMR adoption, successful integration is everything. Otherwise, you have human workers feeling both overburdened and threatened, while your capital expenditures are being underutilized or even misused. Here are three strategies to help foster successful AMR integration:
1. Comprehensive training programs. Implementing thorough training programs for employees is essential to ensure a seamless integration of AMRs into daily warehouse operations. Workers must understand the capabilities, limitations and safety protocols associated with these robotic systems.
- Redefining roles. Redefine the roles of warehouse workers to incorporate AMRs effectively. Encourage employees to take on more supervisory and problem-solving roles, such as monitoring AMR performance, troubleshooting issues and optimizing workflow.
- Collaboration and communication. Encourage open communication between human employees and AMRs. Promote a collaborative environment where workers can provide feedback on AMR performance, allowing for continuous improvement.
Attracting the New Generation of Supply Chain Professionals
The integration of AMRs in the warehouse can help overcome the challenge of attracting and retaining talent in the supply chain industry. As younger generations enter the workforce, they are increasingly seeking technologically advanced workplaces. Demonstrating a commitment to embracing automation and utilizing cutting-edge technologies can make a significant impact on attracting the new generation of supply chain professionals.
AMRs may also allow for a more inclusive warehouse workforce, facilitating the employment of workers who otherwise may be prohibited from starting or continuing their work due to physical or other limitations.
The bottom line: The rise of autonomous mobile robots in warehouses is inevitable. Business leaders must recognize the potential of AMRs to positively transform warehouse operations. They must also understand that the technology is constantly evolving and acknowledge hesitancy on the part of human workers.
By fostering harmony between humans and machines, businesses can leverage AMRs to streamline efficiency, increase productivity, reduce costs, save time, improve worker satisfaction and expand the human talent pool. Embracing AMRs is not about replacing human workers, but rather empowering them to excel in their roles and drive the industry towards a more productive and prosperous future.