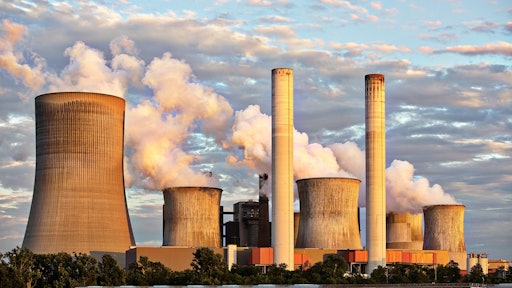
In 2000, outsourcing was just beginning to become the norm in the supply chain, which was detailed in this article from Supply and Demand Chain Executive’s first year. Revisiting this subject 20 years later, it is evident that outsourcing has become a prevalent factor in the U.S. supply chain, so much so that many people question if it is better to bring operations closer to businesses themselves again. Today, most of the supply chain functions are outsourced.
“Trends in outsourcing the supply chain include 80-90% of non-core functions is currently being outsourced,” says Brendan Heegan, CEO of Boxzooka.com. “From e-commerce to PPC to fulfillment and operations to marketing to even HR. You can outsource any function right now.”
In SDCE’s first year, outsourcing just took off, as most companies kept things within their own organizations for more control. Heegan believes that this growth of outsourcing has supported the economy in the past two decades and has allowed the supply chain to become more sophisticated.
“Twenty years ago, companies tried to do all of the non-core competencies functions in house,” he says. “We wouldn't be as advanced today and our economy wouldn't be as strong if companies continued to keep these functions in-house. The old method stagnates growth and stagnates advancement, and the ability to pivot and be competitive. In 2000, there weren't as many out-of-the-box solutions and flexible solutions for fulfillment, and as these platforms came about, it allowed companies to outsource. Outsourcing enables companies to focus on their core competencies, be more competitive and be more nimble.”
However, since the Coronavirus (COVID-19) outbreak, things are very different, and many rethink their strategies, as they look to overcome adversity caused by the pandemic.
“All company expenses are being reviewed, such as product quality, exceeding specifications, risk mitigation, holistic cost and innovation,” says Roy Anderson, chief procurement and digital transformation officer at Tradeshift. “We can break ‘all expenses’ into two major categories: indirect and direct manufacturing expenses.
“Labor expense across all indirect activity is reviewed to determine its value to employees, customers and shareholders. Internal labor expense is involved in many categories including payroll, facilities, call centers, logistics and IT services such as internal data storage, which was at one time a significant internal expense and has since moved to outsourced services such as AWS, Microsoft Azure or Google Cloud services. The trend is that all non-core activity (non-core is unique to each company as to what makes them exceptional in the marketplace) is challenged against external suppliers. The review is not only total cost, buy scale and innovation, but the ability to open up new markets,” adds Anderson.
Direct manufacturing
For direct manufacturing, much of the production process relies on outsourcing to third-party factories in China, moving to a single-source supply chain, explains Anderson. But, since COVID-19’s impact on the supply, many pitfalls in operating this way have been exposed and have companies looking elsewhere to diversify their outsourced production. Countries such as Thailand, India, Malaysia, Vietnam, Indonesia and the Phillippines now get attention as potential sources for third-party outsourcing.
This will become a growing trend, as much of the supply chain today is outsourced, with some companies not handling any of the manufacturing process and instead focusing on the marketing and design.
“Another example of direct expenses are component manufacturers buying from companies that do sub-assemblies, a form of outsourcing, while the buyer handles final assembly and testing,” continues Anderson. “Some companies have even gone as far as eliminating all internal manufacturing, leaving the buyer to own product design, marketing and supply chain, and then outsourcing the rest.
“The next trend is that companies are moving toward building a network of suppliers and customers that share data across tiers of the supply chain. IoT is being deployed across the supply chain to collect inspection, QA, certification and logistics data and deliver that digital data to and AI tools, which in turn, drives better decision making, quality and efficiency. It also creates a ‘digital twin’ of their physical supply chain’s flow and delivers a dashboard with all the key product information. This massive change to the flow of contracts, orders, invoices and payments not only eliminates manual intervention and saves time and money, but it streamlines the flow of working capital," says Anderson.
“The final trend in outsourcing supply chains is to improve risk management,” he adds. “Not only do you need to know your supply chain’s financial, geopolitical and reputational criteria, but you must ensure you’re building an ‘anti-fragile’ supply chain. Antifragility is a property of systems that increase in capability to thrive as a result of stressors, shocks, volatility, noise, mistakes, faults, attacks or failures. The outsourcing supply chain will also be asked to drive sustainability, which will require building and buying based on the ability to reuse, repair, re-manufacture and recycle.”
Outsourcing will continue to be a major part of the supply chain today, but the weak spots exposed during COVID-19 will be adjusted for greater stability. As the supply chain shifts pushed by these outside factors, it is likely that we will never return to the way it was 20 years ago when companies kept most operations in house.