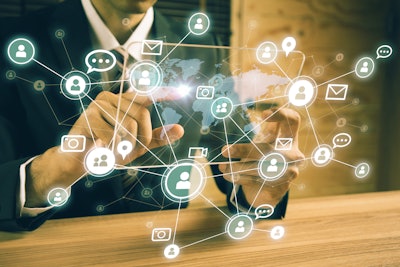
The electronic components supply chain has faced pressure in recent years amid the chip shortage and the rising cost of capital associated with holding extra “buffer” inventory to mitigate the supply constraints. While the semiconductor market is seemingly moving to a stabilized period following a pricing high in 2022, supply chains in high-reliability industries—such as defense and aerospace, medical and energy—have been especially impacted by market disruption.
Though the shortage of the last three years was an unprecedented event, disruption will be a continuous threat for high-reliability industries. To navigate future sourcing constraints, it is critical that original equipment manufacturers (OEMs) leverage long-term, data-driven planning strategies.
Why High-Reliability Industries?
Why did high-reliability industries feel the impact of the shortage more than others? Because they rely on hard-to-source legacy components more than their consumer industry counterparts. Due to the rapid advancement in semiconductor manufacturing, in most of these cases their component types are either at lower levels of production or not in production at all.
High-reliability industries also have stringent requirements for their components. The components must be tested and verified, and when sourcing, OEMs must adhere to strong traceability and quality control standards. This both takes time and limits the number of alternative components available for their systems.
These industries also seek to extend the lifecycle of their products, which is counter-intuitive to consumer-driven industries. Consumer manufacturers develop end products with the assumption that they will be replaced in two or three years. This drives chip suppliers to abandon low-demand, older technology products at a faster pace. Meanwhile, high-reliability manufacturers are driven by their product road map, intense engineering efforts, and long-term support for their systems that does not fit in the two-to-three-year cycle of the consumer sector. They need the older technology that chip manufacturers are likely to abandon, making their components more difficult to source.
As long component lead times and prices have begun waning for some, other buyers that are still being impacted by hard-to-find components are beginning to question: Is now the time to stock up for the next period of instability? While chip manufacturers are working to scale production in the newest technology types, OEMs in high-reliability industries must prioritize strategies for long-term planning to mitigate risks and navigate unplanned semiconductor supply chain disruptions.
Building a Long-Term Strategic Plan
Using historical lead-time data and advanced machine learning forecasting methods, data-driven solutions offer reliability during unplanned semiconductor supply chain disruptions. For OEMs to assert a better position for themselves in the market, there are 4 key data-driven tactics to building a robust long-term plan:
- Demand Forecasting—Leveraging qualitative and quantitative demand forecasting to understand historical trends and coupled with current market opinions/insights.
- Strategic Inventory Purchasing Planning—By combining a comprehensive view of historical purchasing data and forecasted components, organizations can better respond to current and future market needs. This mitigates the risks of future disruptions, plan for obsolescence and manage component lifecycle stages.
- Real-Time Inventory Insights—Inventory is constantly shifting with demand, so it is essential to utilize the most up-to-date information and updates. Without this tactic, organizations can run the risk of customers placing orders for items that have since gone out of stock.
- Setting Accurate Reorder Points—With insight into previous unit demand, organizations can choose the most likely points at which they will need to reorder. It also allows them to analyze lead times for production and warehouse receiving to stay aware of historical and current timelines for receiving.
Key Takeaway: Avoid the Impact of Future Disruption
The semiconductor industry is entering a period of waning demand following the highs of 2022. After years of reactionary decision-making, OEMs should consider this an inflection point and opportunity to develop proactive sourcing strategies to mitigate future disruption. These sourcing strategies should leverage historical lead-time data, real-time insights from trusted industry sources and automated processes to ensure quick, well-informed decisions. There will always be periods of booms and bust in the semiconductor industry, so OEMs must take the opportunity now to develop plans that insulate themselves from the ebbs and flows of the market.