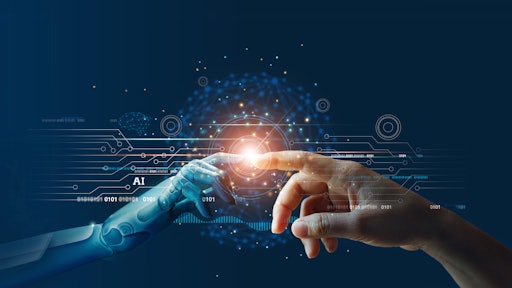
We’re in an era ripe with potential. Technologies that can help hone supply chains are less expensive and more accessible than ever before. Offered as on-demand Software-as-a-Service solutions that require virtually no investment in additional IT infrastructure, they are also more configurable – in many cases enabling users with little or no technical expertise to add forms and functionality without assistance.
As a result, mid-sized businesses that could not justify tech investments with a Fortune 100 price tag now have opportunities to transform their supply chains in ways inconceivable just a few years ago. Such innovations are increasingly ubiquitous across industries for a wide range of use cases, for example:
- Tying a medical device maker’s sales forecasts to purchasing and delivery schedules;
- Monitoring the performance of suppliers for an automotive manufacturer;
- Using robotic pickers in an omnichannel retailer’s distribution center.
There is a subsequent downside. Despite innovations in supply chain technologies, more organizations complete deployments only to find they failed to achieve desired business outcomes. Why this happens is rarely contingent on the technology but instead is a result of common implementation mistakes.
Proper Deployment Enhances Supply Chain Operations
Many supply chain technologies are designed to streamline and automate core operations by using data. This includes mission-critical processes like distribution and logistics management, planning and forecasting, sourcing and supplier management, project and program management, and the numerous workflows involved – all of which can be integrated with enterprise resource planning and other core systems.
Unfortunately, many organizations begin their supply chain technology transformation with an important misconception. Whether the initiative is tech-driven, or tech-enabled success begins with understanding the role of technology.
Importantly, technology allows people to do things they cannot do manually or otherwise would be laborious, but it is rarely a cure all. Nor does merely overlaying new supply chain technology on existing operations often deliver value. Technology alone is not a silver bullet, nor does it deliver on its promise when not aligned with the people and processes involved.
We see this when a state-of-the art robotic picking operation fails to materially impact productivity because inventory is not optimized, or when marketing and manufacturing fail to consistently share the information needed to plan for demand. To successfully deploy technology, several imperatives must be kept in mind.
Imperative #1: Set Specific Goals and Consider Processes Carefully
Any implementation should be governed by business goals and objectives. Are you looking to increase the percentage of on-time deliveries, foster better customer and vendor interactions, increase production levels or simply gain visibility over your supply chain? It is equally imperative to identify the processes involved and determine how to optimize them before or alongside the technology deployment. When used alongside ineffective or bad processes, technology can often make the wrong things happen faster.
Ask yourself what you want to accomplish, determine what the optimal processes look like, and find a solution capable of automating them. Ask too, if additional processes will benefit from the data the new solution delivers. A holistic view is crucial to realize the full value of technology deployment and to create a data-driven enterprise.
A strong data foundation is also crucial. You can’t manage what you don’t measure. Baseline metrics of processes the new system will impact should be gathered beforehand for comparison to outputs from the new solution. Existing data silos – including those that prevent cross-department collaboration – should be removed. Remember too, that collecting too much data can pollute data-driven systems and create needless work. The goal is to gather and use the right data.
Imperative #2: Consider Expectations and Existing Technology
Many failed implementations result from a fundamental misstep – setting unrealistic expectations. As noted above, technology alone does not fix problems. You must have the right processes in place. You want to accelerate the optimal processes the technology makes possible, not just speed up existing ways of doing things. This requires people to embrace the new system and often requires them to learn new ways of working.
Leaders should also assess the organization’s existing supply chain systems. While most new solutions work better, many organizations have valuable, unused supply chain technologies – among them material requirements planning, ERP modules, and e-procurement solutions – because of employee attrition or when adoption wanted because the processes that leveraged the technology were insufficient. Identifying these systems, how data is fed into them, and how they may be used effectively is an important step – one that sometimes shows new technology is not needed at all.
Imperative #3: Involve “Purple” People
No significant supply chain technology implementation should occur without first securing executive buy-in. The endorsement of those at the top is needed to ensure the organization gets behind the adoption of new technology, and that the resulting data is used for maximum impact.
Once it is decided to move forward, it is also important to bring in what we call “purple people.” If operations is red and IT is blue, those who understand both arenas are the “purple” experts who know how new technology will impact supply chain processes. These experts understand the data involved, how it is collected, how it can be analyzed and acted on, and what perimeters need to be considered. Notably, they also bring an understanding of whether an entirely new approach may work better – a key factor to ensure that new supply chain technology is transformative.
“Purple people” also understand and can speak to the challenges and questions not just of operations and IT leaders, but those who report to them. In this way they ensure not only that a proposed solution works in theory, but also in practice – something which requires real-world knowledge honed at the executive table and on the factory or warehouse floor.
For example, when looking at supply timelines, such individuals might not only look at the processes associated with vendor management and the ordering of supplies, but also how requested arrival times compare to actual, historical ones. Using this information, lead times in the system can be adjusted to make planning parameters more accurate for the manufacturing operation and business functions like finance and sales.
Such individuals, who have the ability to explore what is possible while also understanding how things are done currently, are in short supply and high demand, but their impact on supply chain technology implementations cannot be overstated. They are also important to secure the support of respected employees – for example a veteran foreman who can impact how employees respond to a new technology and the new ways of working it demands.
Supply chain leaders have a great opportunity to improve their operations with technology, but it should not be embraced naively. The latest, shiniest innovations are alluring, but only provide value if they address an existing business need. Now, when technology promises so much, the trifecta of any successful implementation – people, processes and technology – must always be considered.