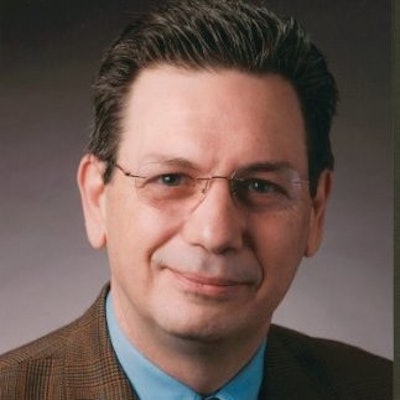
Out-of-stocks (OOS) are all too common with the retail grocery industry’s OOS rate consistently hovering around 8 percent, meaning that one in 13 items on a consumer’s shopping list is not available on the shelf. If the consumer does not (and cannot) buy your product because it is out of stock, you don’t sell. You also provide an opportunity for your competitors to gain your consumers business and loyalty.
While there are many on-shelf availability (OSA) solutions on the market to help manage OOS, the challenge is the industry’s outmoded OSA practices that focus on fixing today’s problems by reactively responding to OOS. However, when you focus on fixing today’s problems, you are already missing sales. Moreover, attempts at intervention often are unsuccessful, ineffective and expensive.
However, what if manufacturers knew the root cause of OOS? You could then monitor for these causes to easily replenish store shelves in a timely manner, as well as maintain optimal inventory levels. So, instead of fixing today’s problems, you prevent tomorrow’s losses. How is this so?
Managing OOS Situations
To effectively address OOS it is critical that the main problem is viewed from the perspective of the shopper. By shifting the focus of OSA from triage to prevention, the percentage of available products on shelves is managed by identifying the root causes of product unavailability. Using a sophisticated, cloud-based supply chain management (SCM) system allows manufactures to collaborate with retailers and suppliers to identify, track, understand and act upon the root cause of OOS to maximize profitability and further synchronize the supply chain.
In order to proactively manage OOS, it is essential to first identify and understand the root cause of the situation. Out-of-stocks can be caused by a number of issues, including phantom stocks, disruptions in the supply chain, underestimating demand for a product or in-store replenishment schedules. The primary goal of root cause analysis is to determine why and where the problems are occurring. In which store, or stores, did the OOS occur? Did an outage occur during a particular sales event? Was product available in the distribution center? Was the data feeding the system accurate?
Maintaining an Accurate PI System
After completing a root cause analysis, findings can be used to develop and implement specific action plans, ultimately preventing OOS from occurring altogether. One of the main sources to OSA is the retailer’s perpetual inventory (PI) system, which drives the quantity and interval in which the product should be ordered. Unfortunately, however, according to industry studies, 65 percent of PI data are inaccurate. These inaccuracies have less to do with technology and more to do with people and process.
A practical solution to recognize where errors occurred in the PI data is to use an exception-based, intelligent system. Given that “phantom inventories” often are the cause of OOS, it is critical to have the capability to both identify the root cause and determine the corrective action.
Implementing a Cloud-based SCM System
Since determining the root cause of an OOS is dependent on data, the richer and more comprehensive the data set is, the better you are able to understand the situation. This also means that the preventative action plan is more likely to succeed in preventing future OOS.
A cloud-based SCM system gives manufacturers the data visibility needed to both measure and manage OSA. These systems have the ability to gather, consolidate and standardize point of sale (POS) data at the store level in order to calculate key performance indicators (KPIs), such as sales, OOS and OSA. In addition, advanced OOS management capabilities allow manufacturers to ensure product availability on store shelves by identifying and addressing the root causes of unavailability.
Using a cloud-based SCM system can turn complex data into simple, actionable information by consolidating information from multiple POS locations into a single dashboard. In addition, by using algorithms, these systems can generate immediate calls to action for replenishment and operations teams. This results in higher product availability, reduced OOS and overstocks.
In order to examine the root cause of lost sales, it is essential to have the capability to view inventory levels as well as compare expected and actual sales. In the event of a product outage, it is flagged in the system. Once flagged, data are gathered to determine the root cause of the outage, allowing users to create workflows within the SCM system for future events. This predetermined best course of action is the key to preventing future OOS.
By implementing a proactive solution to OOS, manufacturers and retailers can prevent loss sales through a scalable and cost-effective process. Additionally, retailers and manufacturers gain increased customer satisfaction fully meeting consumer demand, leading to an increase in profitability and bottom line.
Paris Gogos is vice president marketing and sales engineering of NeoGrid North America. In his current position, Gogos leverages his experience working with some of the world’s most successful consumer packaged goods companies and retailers to help NeoGrid customers align supply with demand and improve on-shelf availability. Gogos previously worked with leaders in demand visibility and retail execution practices including Nielsen, RSi and Efficient Market services. A published thought leader, Gogos holds a degree in marketing and finance from Rosebank College in South Africa.