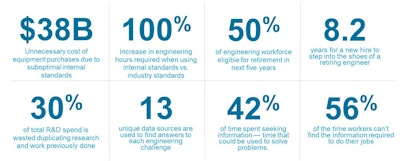
There was a time when “fit for purpose,” standards and over-engineering industry standards in the oil and gas industry were acceptable practices. Commodity prices were triple what they are today, operator revenues were rising, and there was no end in sight for rising crude oil prices. Fast-forward to 2016 and the environment couldn’t be any different for oil and gas companies. Not only have crude oil prices dropped dramatically since 2013, but capital and operating costs have remained high. And while the need to improve returns was already an issue in the high oil price environment three years ago, that need has now become a mandate for all companies in the sector.
In this article we’ll explore the key challenges currently facing the oil and gas industry and show how optimizing internal standards and leveraging industry standards can help companies gain efficiencies and operate more profitably in this challenging business environment.
Addressing Down-Cycle Challenges Head-On
Challenged by a down-cycle that reared its head quickly and that has yet to subside, oil and gas companies are looking for innovative ways to maintain profitability and sustain growth. To achieve these goals, organizations are renegotiating supplier contracts, restructuring internal departments and processes, and reducing overhead. Leading organizations are also examining the standards they use, the impact these standards have on engineering hours, supplier cost, and as a result developing ways to operate more efficiently. For many, the answer lies in optimizing internal standards and moving away from proprietary standards to a more efficient, operationally excellent way of managing standards and specifications across the board.
The problem is that companies active in oil and gas exploration and production (E&P) today rely heavily on industry standards. It is estimated that the 120,000 engineers working for the top 500 energy companies in the world rely on 80,000 different industry standards from over 135 standards bodies. But most oil and gas companies also complement industry standards with their own internal proprietary standards to build, maintain and operate their operations infrastructure. The combination of working with industry standards plus internal standards create what engineers and suppliers at customer sites refer to as the forklift problem. One internal standard will reference 10 or more other internal or international standards, which then reference another 10 each. By the time you add up all of the standard documentation for a particular project, you have a very tall stack of paper.
These internal standards may leverage industry-approved standards as a starting point, but companies then often layer on additional company-specific requirements to ensure reliability and safety, increase efficiency, address challenges seen on past projects, improve maintainability, encapsulate corporate practices, and reflect the perspectives and experience of internal groups. For example, an oil and gas company could decide that all of its electrical equipment boxes be painted orange (to meet equipment color-coding requirements) instead of industry-standard green.
Whatever the reason, these bespoke standards typically add additional costs that often are not justified by the added benefits.
What’s Driving Up Costs?
Engineering costs are being driven up by a number of factors. For example, companies spend $38 billion in unnecessary purchases due to suboptimal internal standards and 30 percent of total research and development (R&D) spend is wasted duplicating research that was previously done. Out-of-date references, over-engineering, lack of supplier feedback are just a few of the factors that contribute to the challenges. Plus, when internal standards are used (versus industry standards), companies experience a 100 percent increase in engineering hours required to do the work.
[insert ‘Standards_Image_1.jpg’] --- run the sidebar in this area too
As you can see from this example, internal standards come at a cost. Companies that want to enable step-change advances in cost performance should go back to the basics and simplify the problem by moving away from proprietary standards and adopting industry standards when possible. If more robust requirements are needed, it is important to follow a structured approach to identifying and prioritizing changes needed and their cost impact.
A Better Approach to Standards
Oil companies are beginning to realize that proprietary standards can significantly drive up costs (e.g., those that rely on internal standards spent 20 to 100 percent more than those that use industry standards), while industry-wide agreement on common standards can spread costs across a larger base of operators and suppliers and thus reduce cost. In the case of the orange electrical equipment box cited above, for example, the color change leads to extra manufacturing time, requires the supplier to carry additional inventory, and leads to custom testing and inspection.
[insert ‘Standards_Image_2.jpg’]
In the case of large, complex E&P projects, engineers at the engineering, procurement and construction (EPC) firms that build upstream infrastructure must get up to speed on different proprietary requirements for every project. This requirement limits knowledge reuse and scale, thereby adding costs and delaying schedules. Across thousands of projects in the industry, the impact is billions of dollars in additional costs and delays.
Internal Standards Optimization in Action
In the quest to sustain growth in a volatile business climate, oil and gas companies must move away from—where feasible and appropriate—proprietary standards (or from custom adaptations on top of industry standards) and toward adoption of pure industry standards. Recently, a global energy company looking to lower costs enterprise-wide asked IHS to review 35 internal standards and list 143 comparable international standards. Through this exercise, research uncovered cost-savings opportunities including 25 percent savings on drilling casing/tubing for $5 million annually and $180 million annually for conformance across all industry standards.
A second global energy customer of IHS optimized procurement specifications by creating a model of zero-based design with suppliers. The IHS customer found 15 procurement specification steps for custom specifications, and was able to reduce that to six steps using zero-based design. The anticipated savings is 30 percent with their supplier, and a 50 percent reduction in engineering hours removing custom specification, acceptance, potential delays and punch lists.
In the first example, IHS analysts modeled the global energy company’s standards to identify design decisions. They used IHS software to access 1.7 million industry standards, and also IHS Goldfire software to semantically analyze and identify deviations between internal and industry standards. IHS also worked with key individuals from the company as part of a carefully structured value engineering exercise to capture cost variances.
IHS reviewed the O&G company’s 35 internal standards for: BOP equipment; cement; downhole; drilling fluids; rigs/rig equipment; wellhead equipment; and casings, tubing and drill pipe. They compared those 35 internal standards to a list of 143 American Petroleum Institute (API) standards for drilling operations that they gleaned from IHS Standards Expert, which tracks 1.7 million standards from 400 organizations worldwide. This in-depth research revealed that:
- More than one quarter (26 percent) of the company’s drilling standards were outdated, having been replaced or dropped as international standards.
- The company was not complying with more than half (55 percent) of the API standards used by its peers from the International Oil Companies (IOC).
- These deviations from industry standards exposed their company to risks of non-compliance as well as unnecessary added costs.
The chief engineer realized that his company could cut costs by conforming more closely to industry standards. After conducting a detailed analysis of the company’s standards for casing and tubing, IHS gained representative insights into the cost of maintaining proprietary standards versus adopting industry ones. The team then calculated the company’s standards expenses and prioritized areas for improvement— in terms of cost, reliability and performance attributes such as surface casing collapse and burst strength.
The potential cost savings from closer conformity to industry standards added up quickly. For example, if the average cost of casing is $75 to $100 per meter, and if the company’s well holes are typically 3,000 to 5,000 meters deep, the total cost of casing/tubing for one well would range from $225,000 to $500,000. Using industry-standard casing materials, the company could maintain performance, reliability, and risk-mitigation needs while saving 25 percent off the premium materials specified in its current, internal standards.
With an estimated 12 new wells each year, this company will save up to $5 million annually on casing and tubing standards conformity, with additional savings on maintenance of existing wells, once they make the changes to their internal standards.
The company could also realize far greater cost savings by further analyzing its complete set of internal standards in this same manner. These savings include not only material costs, but also a host of other factors, ranging from internal and external engineering and contractor hours, inventory management costs, transportation and labor. In total, the company could save up to $180 million annually by implementing the recommendations across its entire collection of internal standards.
It’s Time for a Change
Historic reductions in the price of oil are rocking the global energy industry in the 21st century. Industry leaders, who were already focused on driving efficiency and operational excellence, are now feeling an even greater sense of urgency as they strive to maintain profit margins despite oil price reductions of more than 50 percent.
The executive-level mandate to cut costs has given the oil and gas industry a compelling reason to drive the difficult-to-achieve consensus needed to develop better and more complete standards. Concurrently, new industry working groups can be created to forge consensus, with senior executives from leading companies providing the impetus for change. And while cost reductions were seen as a priority even before the crash, now they are an absolute necessity.
By driving costs out of their own internal standards, putting governance and process controls in place to ensure standards decisions are made in a business context, and using industry standards where possible, companies can offset the negative impacts of low oil prices and high operating costs to develop more operationally efficient strategies for any economic conditions.
Sidebar:
Consider this example of how internal standards can drive up costs due to over-specification:
API standard pumps cost about three times that of ANSI standard pumps, and are appropriate when pumping flammable oil. However, many internal standards call for using API pumps more broadly, even for pumping cooling water and condensate. Standards call for nickel alloy when 316L stainless steel is appropriate, or tantalum when titanium is appropriate.
Proprietary specs would require customized equipment that can cost five to 10 times more than off-the-shelf equipment, and with unclear benefit. In addition, out-of-date references to industry standards would drive unnecessary customization and rework and lack of clarity in deviations from referenced industry standards, and would create extra engineering time on each project.