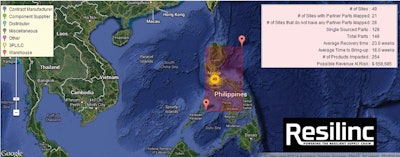
Earthquakes. Tsunamis. Typhoons. Blizzards. Floods. Fires. Droughts. Labor strikes. Political upheaval. Supply shortages. Product recalls. New regulations. Pick your disruption, and most supply chain executives will have a story to share with you. They probably won’t be pleasant tales, either. They’ll be woeful yarns detailing shipping delays, lack of alternate parts or suppliers, inventory write-downs, missed production deadlines, revenue hits and profit plunges.
This is the world today, and complex, global supply chains are fraught with risk. Some risks are known and managed well enough. Many, though, are barely considered until a crisis hits and executives have to do triage work to keep the business running.
Curiously, many companies have implemented sourcing and planning strategies that have boosted their operational agility, supply chain flexibility and overall responsiveness to shifting business conditions. At the heart of many of these improvements sits every company’s not-so-secret weapon: Visibility into supply chain and supplier activities.
Arguably, however (and based on real-life examples of how many companies struggle in a disaster’s aftermath), supply chain visibility solutions haven’t gone far enough in protecting companies from the long tail of negative impact when a disruption occurs. So while an organization may weather through an immediate emergency, many companies are not truly resilient. Often, their long-term ability to walk away from a disruption relatively unscathed is rather limited.
If history is a guide, companies won’t have any shortage of opportunities to strengthen their resiliency muscles. The sheer number of new potential threats and other possible chaos-causing events is steadily increasing. Resilinc last year tracked 293 global supply chain disruptions (which included natural disasters, factory explosions, labor disputes, power outages, chemical spills and geopolitical upheaval) during a 12-month period. That translates roughly to one disruption a day wrecking havoc somewhere in the global supply chain.
A Stress Test
Said simply, globally interconnected supply chains will face more risks globally, and any disruption’s ripple effect will touch more companies and more tiers of the supply chain.
You don’t have to look too far to see examples of this stress. The Japanese earthquake and tsunami a few years back provides plenty of insight into the importance of resiliency, and has triggered many corporate responses to examine and fix vulnerable supply chain links.
One of our high-tech customers, for example, suffered considerably in the tsunami’s aftermath. The disaster negatively impacted the company’s financial results, and did much more damage that was harder to repair. Limited supply chain visibility caused shipment delays and customer satisfaction issues, and the inability to accurately quantify risks in the supply chain and allocate resources resulted in increased costs.
To protect itself from future disruptions, the company prioritized supply chain mapping, business continuity planning, supply chain risk assessment, and mitigation. Within in a few months of taking a focused supply chain resiliency approach, the company's overall supply chain visibility improved substantially. The company also lowered costs related to planning for and reacting to disruptions and it instituted best practices companywide. Improved visibility increased the overall reliability of the company's supply chain operations, which, in turn, allowed it to serve customers more effectively.
That’s what it looks like when your supply chain runs on resiliency. But, to get to this stage, companies have to first consider a few key strategic moves.
Resiliency Planning
Building more resilient supply chain operations requires asking and honestly answering hard questions, such as:
- How far up and down your supply chain can you really see? How much visibility do you have beyond your first and second tier of supply?
- Have you mapped internal and supplier sites and analyzed what percentage of revenue depends on supply from those sites?
- How quickly can your supply chain respond to emergencies or others risks that could disrupt supply chain activity?
- What is your strategy for dealing with crisis when it happens and in the days, weeks and months after it happens?
- Does everyone on your supply team know how to track disruptive events, escalate alerts to avoid ongoing financial impact and respond in a way that protects continuity of supply while sustain operational performance?
As companies work through these questions, they’ll also want to set up an approach that includes three vital elements: plan, monitor and protect.
Plan. To be resilient, companies have to identify ALL their risks. Often because of limited resources and time, companies usually only can spot a risk one or two supply chain tiers away. But what happens when laborers strike at a copper mine or at a port in an important market? Or a specialized component maker quietly goes belly up?
The question quickly goes from “Do you have supply chain visibility?” to “How do you use, analyze and reuse all the data you see?”
Monitor. The Internet has made hearing about disruptive events immensely easier. But, that doesn’t mean, anyone is doing anything with these news alerts as they pop in or escalating them to a stage where action is taken to prevent or slow down the impact.
Resiliency requires discipline in managing and monitoring multiple information inputs, tracking events that could potentially harm their companies and products, and constantly assessing the potential future impact. For the most part, this level of event monitoring only happens superficially at many companies and not in an organized way that can be called a risk management strategy. What’s needed is a smarter, more intuitive way of following the newsfeed and embedding them into the business continuity strategy.
Protect. Even if companies have developed emergency contingency plans and vigilantly track events, many of them don’t have an adequate way to fully protect themselves when the disruption’s impact extends over a long period of time.
To get the most from risk mapping and monitoring activities, companies have to follow through with a more thoughtful and coordinated response designed to protect the company for the long term, not just in the days or week after a disaster strikes. This involves strategically assigning mitigation ownership responsibilities, setting risk thresholds for sourcing and recovery time, defining mitigation action items and tracking various performance metrics, among many other things.
By applying some of these techniques, companies will find that their supply chain can both withstand and quickly recover from disruptions in hours rather than weeks or months. And, that will have them running further and faster than the competition.
Bindiya Vakil is CEO and founder of Resilinc